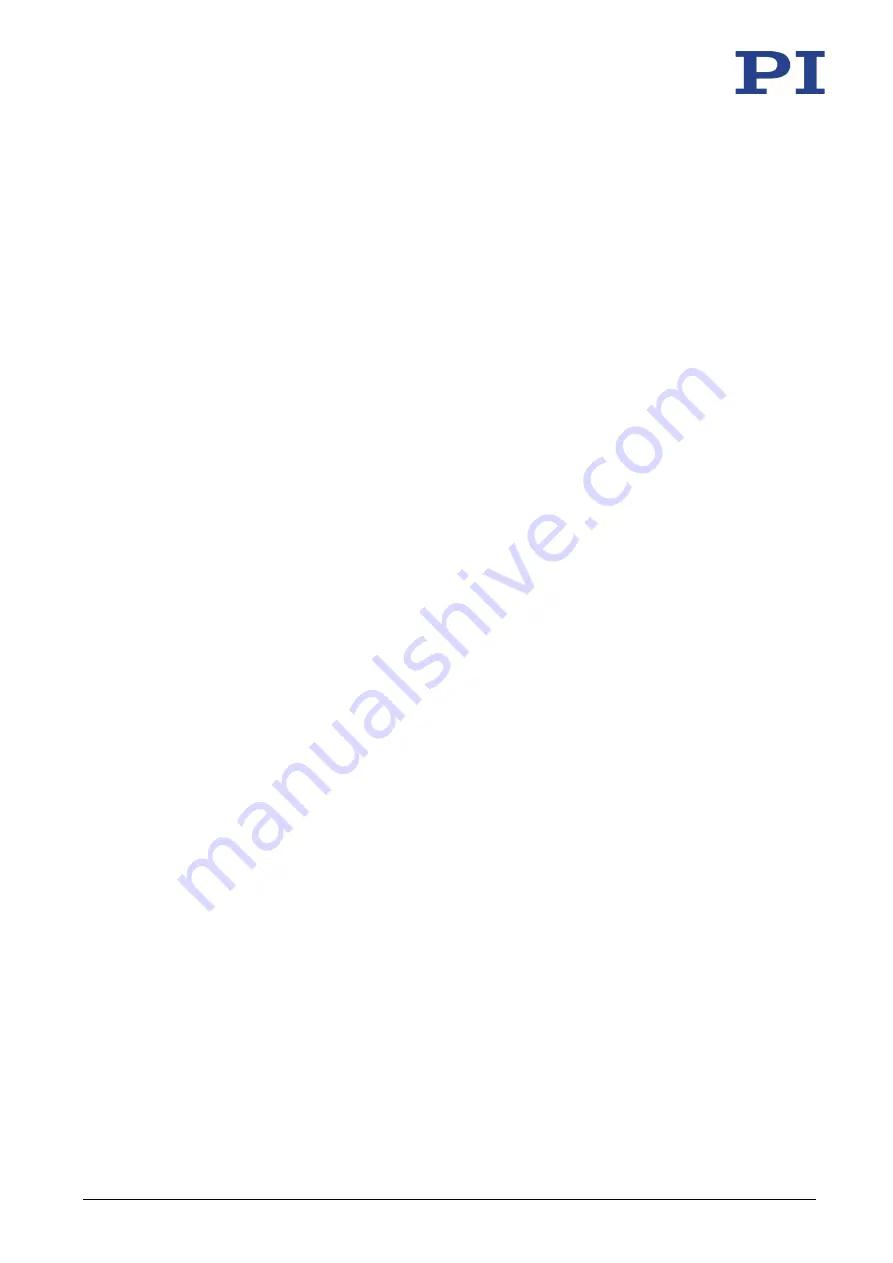
3 Product Description
M-238 High-Load Linear Actuator
MP77E
Version: 1.1.0
7
3.5
Technical Features
3.5.1
Integrated PWM amplifier
The M-238 model is equipped with a PWM amplifier ("ActiveDrive concept").
The integrated PWM amplifier for ActiveDrive DC motors only receives control signals from the
control electronics, whereas the supply voltage is provided via an external power adapter. The
higher motor performance allows better dynamics.
3.5.2
Encoder
The
M-238.5PG
model is equipped with a
rotary encoder
. A rotary encoder is implemented at a
rotating point in the drivetrain, e.g., the motor shaft. The encoder provides a certain number of
signals for each change of position. The controller counts the encoder signals, the so-called
pulses, in order to determine the relative position. The M-234 must be moved to a limit or
reference switch in order to measure the absolute position (referencing).
The
M-238.5PL
model is equipped with an optical
linear encoder
. Optical linear encoders
measure the actual position directly and therefore eliminate drive errors such as nonlinearity,
backlash or elastic deformation.
The resolution of the encoders can be found in the data table (p. 23).
3.5.3
Limit Switches
The limit switches are sensors at each end of the travel range that enable the electronics to
abort motion in order to prevent the pusher from colliding with the mechanical hard stop.
The M-238 is equipped with noncontact Hall effect limit switches (p. 25).
3.5.4
Reference Switch
The reference switch is a sensor whose fixed position serves as the reference point for
incremental sensor signals.
The M-238 is equipped with a magnetic (Hall effect), direction-sensing reference switch (p. 25)
positioned approximately at the midpoint of the travel range. This sensor sends a TTL signal
that indicates whether the positioner is on the positive or negative side of a specified point.
Both the rising and falling edges of the signal can serve as reference (accuracy approx. 0.5 μm,
depending on the controller). The difference between the reference points is approx. 0.2 to 0.4
mm when approached from the positive or negative direction.
The commands that use the reference signal are described in the user manual for the
controller.