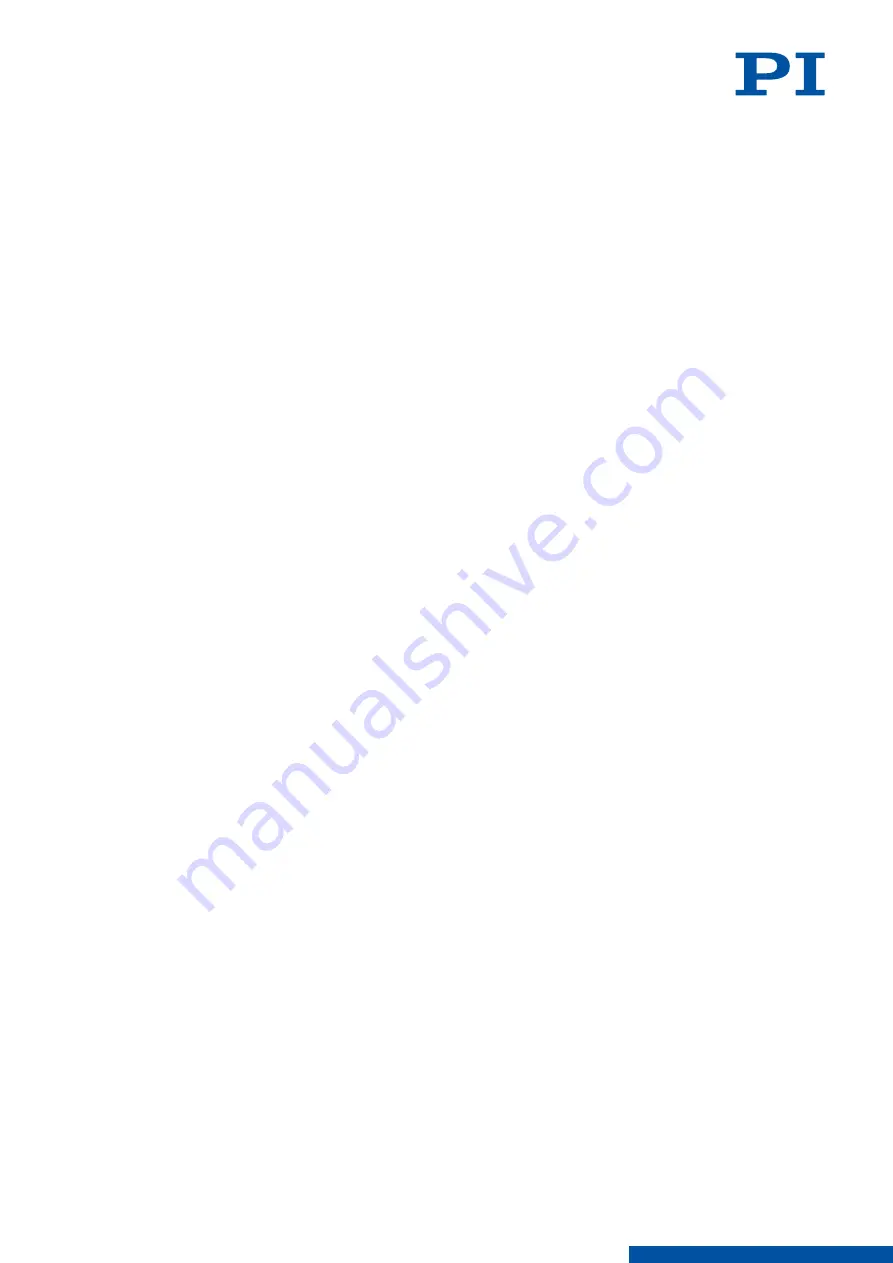
Glossary
Backlash
Position error caused by mechanical play in that drivetrain that occurs when changing the
direction. Backlash is caused by mechanical play in drivetrain components such as
gearheads, bearings or by friction in the guides. In contrast to hysteresis, backlash can lead
to instability in position-controlled systems because it causes dead time in the servo loop.
Backlash depends on the temperature, acceleration, load, leadscrew position, positioning
direction, wear etc. Backlash is suppressed by preloading the drivetrain. A position
measuring method that can detect the position of the platform directly, eliminates all errors
in the drivetrain (direct measuring).
Design Resolution
The theoretical minimum movement that can be made. Design resolution must not be
confused with minimum incremental motion. In indirect position measurement methods,
values for drive screw pitch, gear ratio, motor or sensor/encoder resolution, for example, are
included in the calculation of the resolution. Normally, the design resolution is considerably
below the minimum incremental motion of the mechanics. In direct measurement methods,
the resolution of the sensor system is specified.
Lateral Force
Also: Lateral load capacity
Maximum permissible force orthogonally to the positioning direction. This value is directly
valid for the motion platform or the slider with mounting rails at the product. The value is
reduced when the force acts above the platform/slider.
Limit Switch
Each limit switch sends its signal to the controller on a dedicated line. The controller then
interrupts the motion avoiding that the positioner moves until the hard stop and gets
damaged. PI positioners have mechanical, noncontact optical or Hall effect limit switches.
Load Capacity
Maximum load in the vertical direction when the L-412.xx9025E1 is mounted horizontally.
The contact point of the load is at the center of the motion platform.
Reference Switch
Many of the positioners are equipped with a direction sensing reference switch positioned
approx. in the middle of the travel range. It is recommended to approach the reference
switch always from the same direction to obtain best position repeatability.
Function: Optical, magnetic
Sensor Resolution
The sensor can be the critical element of position resolution so it may be necessary to
specify the sensor resolution separately. Rotary encoder: Impulses per screw rotation. Linear
encoder: Smallest motion still detected by the sensor system.
L412UM0002EN
‒
10/24/2022
41
M O T I O N | P O S I T I O N I N G