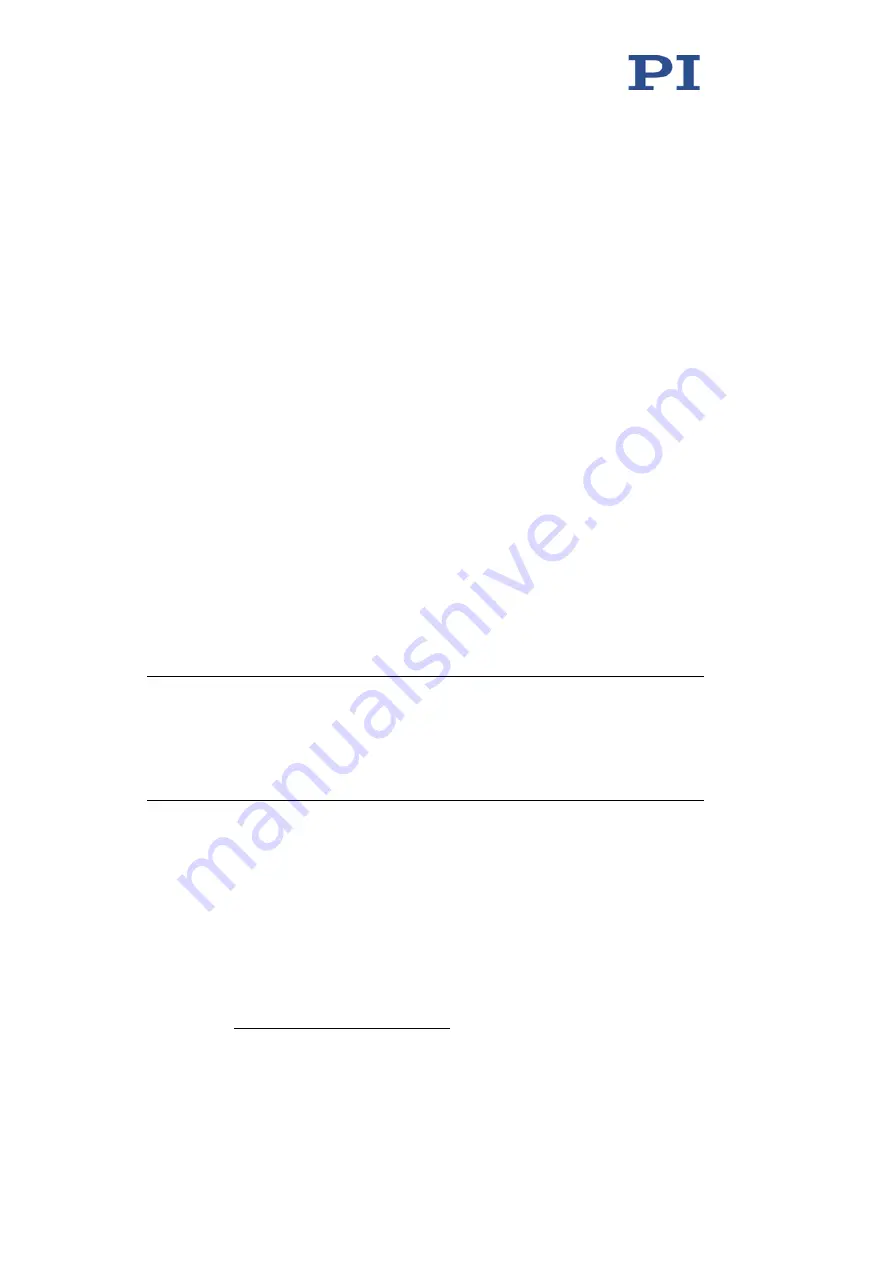
Calibration
www.pi.ws
E-651 / E-614 Controller / Amplifier PZ129E Release 6.1.0 Page 14
5
Calibration
Note that upon delivery the system is ready for operation: all of
PI's positioning systems with a piezo actuator are delivered with
performance test documents to verify the system performance,
and calibration of the controller is done prior to delivery in our
lab. Actuators and assigned controller channels are matched
and should be kept together as a unit. The serial number of the
actuator assigned to each channel is marked on the individual
controller.
Normally there is no need for you to recalibrate the system.
Only exchanging the actuator, the mechanical setup, replacing
the cables on the actuator or making a large change in the
operating temperature, may make recalibration necessary.
The only procedure which is necessary from time to time is the
zero-point adjustment (see below). All other calibration
procedures—static gain adjustment
and dynamic calibration
require special equipment and should only be done by qualified
personnel and are required only in special circumstances. See
the user manuals for the sensor processing and servo-control
submodules (E-801 and E-802) for details regarding those
procedures.
5.1
Equipment Needed
Zero-point adjustment requires a voltmeter and a small straight-
bladed screw driver.
5.2
Zero-Point Adjustment
Proper zero-point adjustment ensures that the full output
voltage swing of the amplifier can be used without reaching the
output voltage limits of the amplifier and causing overflow
conditions, both in open-loop and closed-loop operation. If an
overflow condition occurs (OFL LED lights up for the channel), it
can often be prevented by re-adjusting the ZERO point.
The zero-point of each channel is adjusted with the appropriate
ZERO potentiometer (E-651: ZERO potentiometer for each
1
The objective of static gain adjustment is to ensure that the actuator
expands to its nominal expansion in "positive" direction when a control signal
input of +5 V is applied (with DC-offset disabled).
2
Dynamic calibration optimizes step response and suppresses resonance,
overshoot, and oscillation.