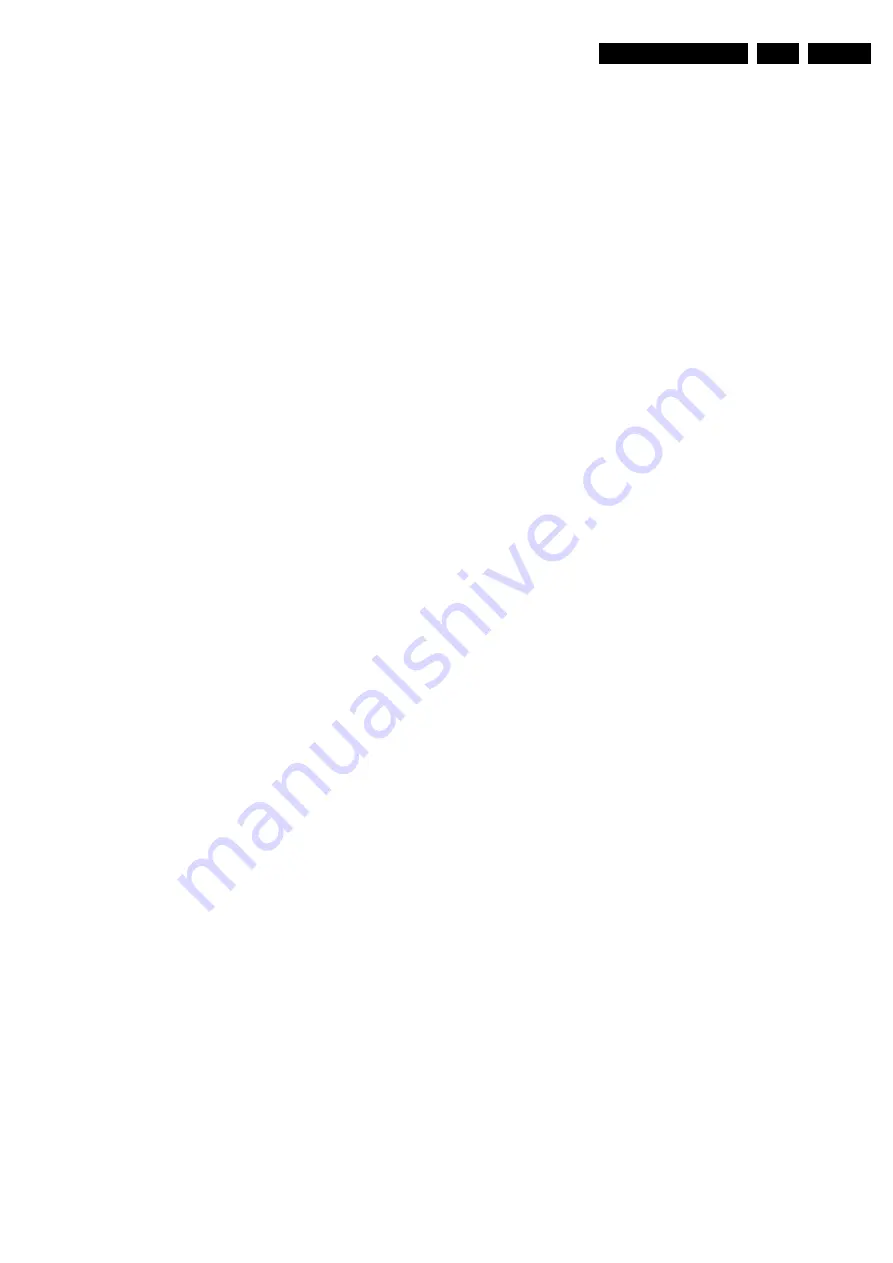
Circuit Description
9.
second half the spot accelerates, the SCAVEM-current is
zero at the end of the slope.
The R/G/B signals are fed into the SCAVEM circuit and
differentiated by C2364/2365/2366 and the input impedance of
7360 stage. Diode 6364 (Schottky diode) is the coring
component, which blocks all the signals below 0.3 V so that the
noise is not amplified and all the signals larger than 0.3V are
differentiated and amplified.
After differentiation, the signal is amplified by Q7360 with 3369
as the collector resistor. The biasing of the 7360 stage is done
by 3369, 3361, 3360, 3362, and 3363.
Items 6367, 2367, 3367, 3361, and 2360 work as the clipping
components that limit the SCAVEM current at a certain level, to
prevent SCAVEM over correction.
After being buffered by 7369, the differentiated signals are
coupled through 2375 and 2380 to the output stage. The output
stage is configured into cascode stage and push-pull operation.
The biasing is done by 3373, 3375, 3376, 3380, 3381, 3383,
3374, and 3384. The working voltage of the transistors is
settled at half the supply voltage.
At the rising portion of the R/G/B signals, cascode 7380 and
7382 will be operating and will pull the current through the
SCAVEM coil. Contrarily, at the falling portion of the R/G/B
signals, cascode 7373 and 7366 will be operating and will push
the current through the SCAVEM coil.
The capacitors 2362, 2373, and 2381 ground the high
frequencies, to prevent high frequency amplification. The ferrite
bead 5376 is for EMC purpose. Resistors 3374 and 3384
determine the output SCAVEM current.
Items 2378 and 3378 are for the fine-tuning for different
SCAVEM coil impedances. They also help to suppress high
frequency oscillation. Capacitor 2369 helps to suppress the
high frequency components and also controls the SCAVEM
delay.
9.4
Synchronization
Inside IC 7200 part D, the vertical and horizontal sync pulses
are separated. These 'H' and 'V' signals are synchronized with
the incoming CVBS signal. They are then fed to the H- and V-
drive circuits and to the OSD/TXT circuit for synchronization of
the On Screen Display and Teletext (CC) information.
9.5
Deflection
9.5.1
Horizontal Drive
The horizontal drive signal is obtained from an internal VCO,
which is running at twice the line frequency. This frequency is
divided by two, to lock the first control loop to the incoming
signal.
When the IC is switched 'on', the 'Hdrive' signal is suppressed
until the frequency is correct.
The 'Hdrive' signal is available at pin 30. The 'Hflybk' signal is
fed to pin 31 to phase lock the horizontal oscillator, so that
Q7462 cannot switch 'on' during the flyback time.
The 'EWdrive' signal for the E/W circuit (if present) is available
on pin 15, where it drives transistor 7400 to make linearity
corrections in the horizontal drive.
When the set is switched on, the '+8V' voltage goes to pin 9 of
IC 7200. The horizontal drive starts up in a soft start mode. It
starts with a very short TON time of the horizontal output
transistor. The TOFF of the transistor is identical to the time in
normal operation. The starting frequency during switch on is
therefore about 2 times higher than the normal value. The 'on'
time is slowly increased to the nominal value in 1175 ms. When
the nominal value is reached, the PLL is closed in such a way
that only very small phase corrections are necessary.
The 'EHTinformation' line on pin 11 is intended to be used as a
'X-ray' protection. When this protection is activated (when the
voltage exceeds 6 V), the horizontal drive (pin 30) is switched
'off' immediately. If the 'H-drive' is stopped, pin 11 will become
low again. Now the horizontal drive is again switched on via the
slow start procedure.
The 'EHTinformation' line (Aquadag) is also fed back to the
UOC IC 7200 pin 54, to adjust the picture level in order to
compensate for changes in the beam current.
The filament voltage is monitored for 'no' or 'excessive' voltage.
This voltage is rectified by diode 6447 and fed to the emitter of
transistor 7443. If this voltage goes above 6.8 V, transistor
7443 will conduct, making the 'EHT0' line 'high'. This will
immediately switch off the horizontal drive (pin 30) via the slow
stop procedure.
The horizontal drive signal exits IC 7200 at pin 30 and goes to
7462, the horizontal driver transistor. The signal is amplified
and coupled to the base circuit of 7460, the horizontal output
transistor. This will drive the line output transformer (LOT) and
associated circuit. The LOT provides the extra high voltage
(EHT), the VG2 voltage and the focus and filament voltages for
the CRT, while the line output circuit drives the horizontal
deflection coil.
9.5.2
Vertical Drive
A divider circuit performs the vertical synchronization. The
vertical ramp generator needs an external resistor (R3245, pin
20) and capacitor (C2244, pin 21). A differential output is
available at pins 16 and 17, which are DC-coupled with the
vertical output stage.
During the insertion of RGB signals, the maximum vertical
frequency is increased to 72 Hz so that the circuit can also
synchronize on signals with a higher vertical frequency like
VGA.
To avoid damage of the picture tube when the vertical
deflection fails, the guard output is fed to the beam current
limiting input. When a failure is detected, the RGB-outputs are
blanked. When no vertical deflection output stage is connected,
this guard circuit will also blank the output signals.
These '' and 'V_DRIVE-' signals are applied to the
input pins 1 and 2 of IC 7471 (full bridge vertical deflection
amplifier). These are voltage driven differential inputs. As the
driver device (IC 7200) delivers output currents, R3474 and
R3475 convert them to voltage. The differential input voltage is
compared with the voltage across measuring resistor R3471
that provides internal feedback information. The voltage across
this measuring resistor is proportional to the output current,
which is available at pins 4 and 7 where they drive the vertical
deflection coil (connector 0222) in phase opposition.
IC 7471 is supplied by +13 V. The vertical flyback voltage is
determined by an external supply voltage at pin 6
(50V). This voltage is almost totally available as
flyback voltage across the coil, this being possible due to the
absence of a coupling capacitor (which is not necessary, due
to the 'bridge' configuration).
9.5.3
Deflection Corrections
The Linearity Correction
A constant voltage on the horizontal deflection coil should
result in a sawtooth current. This however is not the case as the
resistance of the coil is not negligible. In order to compensate
for this resistance, a pre-magnetized coil L5457 is used. R3485
and C2459 ensure that L5457 does not excite, because of its
own parasite capacitance. This L5457 is called the 'linearity
coil'.
The Mannheim Effect
When clear white lines are displayed, the high-voltage circuit is
heavily loaded. During the first half of the flyback, the high
www.freeservicemanuals.info
22/11/2016
Published in Heiloo Holland
Содержание L01.1U
Страница 10: ...Directions for Use EN 10 L01 1U AC 3 www freeservicemanuals info 22 11 2016 Published in Heiloo Holland ...
Страница 11: ...Directions for Use EN 11 L01 1U AC 3 www freeservicemanuals info 22 11 2016 Published in Heiloo Holland ...
Страница 12: ...Directions for Use EN 12 L01 1U AC 3 www freeservicemanuals info 22 11 2016 Published in Heiloo Holland ...
Страница 13: ...Directions for Use EN 13 L01 1U AC 3 www freeservicemanuals info 22 11 2016 Published in Heiloo Holland ...
Страница 14: ...Directions for Use EN 14 L01 1U AC 3 www freeservicemanuals info 22 11 2016 Published in Heiloo Holland ...
Страница 15: ...Directions for Use EN 15 L01 1U AC 3 www freeservicemanuals info 22 11 2016 Published in Heiloo Holland ...
Страница 16: ...Directions for Use EN 16 L01 1U AC 3 www freeservicemanuals info 22 11 2016 Published in Heiloo Holland ...
Страница 17: ...Directions for Use EN 17 L01 1U AC 3 www freeservicemanuals info 22 11 2016 Published in Heiloo Holland ...
Страница 18: ...Directions for Use EN 18 L01 1U AC 3 www freeservicemanuals info 22 11 2016 Published in Heiloo Holland ...
Страница 19: ...Directions for Use EN 19 L01 1U AC 3 www freeservicemanuals info 22 11 2016 Published in Heiloo Holland ...
Страница 20: ...Directions for Use EN 20 L01 1U AC 3 www freeservicemanuals info 22 11 2016 Published in Heiloo Holland ...
Страница 21: ...Directions for Use EN 21 L01 1U AC 3 www freeservicemanuals info 22 11 2016 Published in Heiloo Holland ...
Страница 22: ...Directions for Use EN 22 L01 1U AC 3 www freeservicemanuals info 22 11 2016 Published in Heiloo Holland ...
Страница 23: ...Directions for Use EN 23 L01 1U AC 3 www freeservicemanuals info 22 11 2016 Published in Heiloo Holland ...
Страница 24: ...Directions for Use EN 24 L01 1U AC 3 www freeservicemanuals info 22 11 2016 Published in Heiloo Holland ...
Страница 26: ...Directions for Use EN 26 L01 1U AC 3 www freeservicemanuals info 22 11 2016 Published in Heiloo Holland ...
Страница 27: ...Directions for Use EN 27 L01 1U AC 3 www freeservicemanuals info 22 11 2016 Published in Heiloo Holland ...
Страница 28: ...Directions for Use EN 28 L01 1U AC 3 www freeservicemanuals info 22 11 2016 Published in Heiloo Holland ...
Страница 29: ...Directions for Use EN 29 L01 1U AC 3 www freeservicemanuals info 22 11 2016 Published in Heiloo Holland ...
Страница 30: ...Directions for Use EN 30 L01 1U AC 3 www freeservicemanuals info 22 11 2016 Published in Heiloo Holland ...
Страница 31: ...Directions for Use EN 31 L01 1U AC 3 www freeservicemanuals info 22 11 2016 Published in Heiloo Holland ...
Страница 32: ...Directions for Use EN 32 L01 1U AC 3 www freeservicemanuals info 22 11 2016 Published in Heiloo Holland ...
Страница 33: ...Directions for Use EN 33 L01 1U AC 3 www freeservicemanuals info 22 11 2016 Published in Heiloo Holland ...
Страница 34: ...Directions for Use EN 34 L01 1U AC 3 www freeservicemanuals info 22 11 2016 Published in Heiloo Holland ...
Страница 35: ...Directions for Use EN 35 L01 1U AC 3 www freeservicemanuals info 22 11 2016 Published in Heiloo Holland ...
Страница 36: ...Directions for Use EN 36 L01 1U AC 3 www freeservicemanuals info 22 11 2016 Published in Heiloo Holland ...
Страница 37: ...Directions for Use EN 37 L01 1U AC 3 www freeservicemanuals info 22 11 2016 Published in Heiloo Holland ...
Страница 38: ...Directions for Use EN 38 L01 1U AC 3 www freeservicemanuals info 22 11 2016 Published in Heiloo Holland ...
Страница 39: ...Directions for Use EN 39 L01 1U AC 3 www freeservicemanuals info 22 11 2016 Published in Heiloo Holland ...