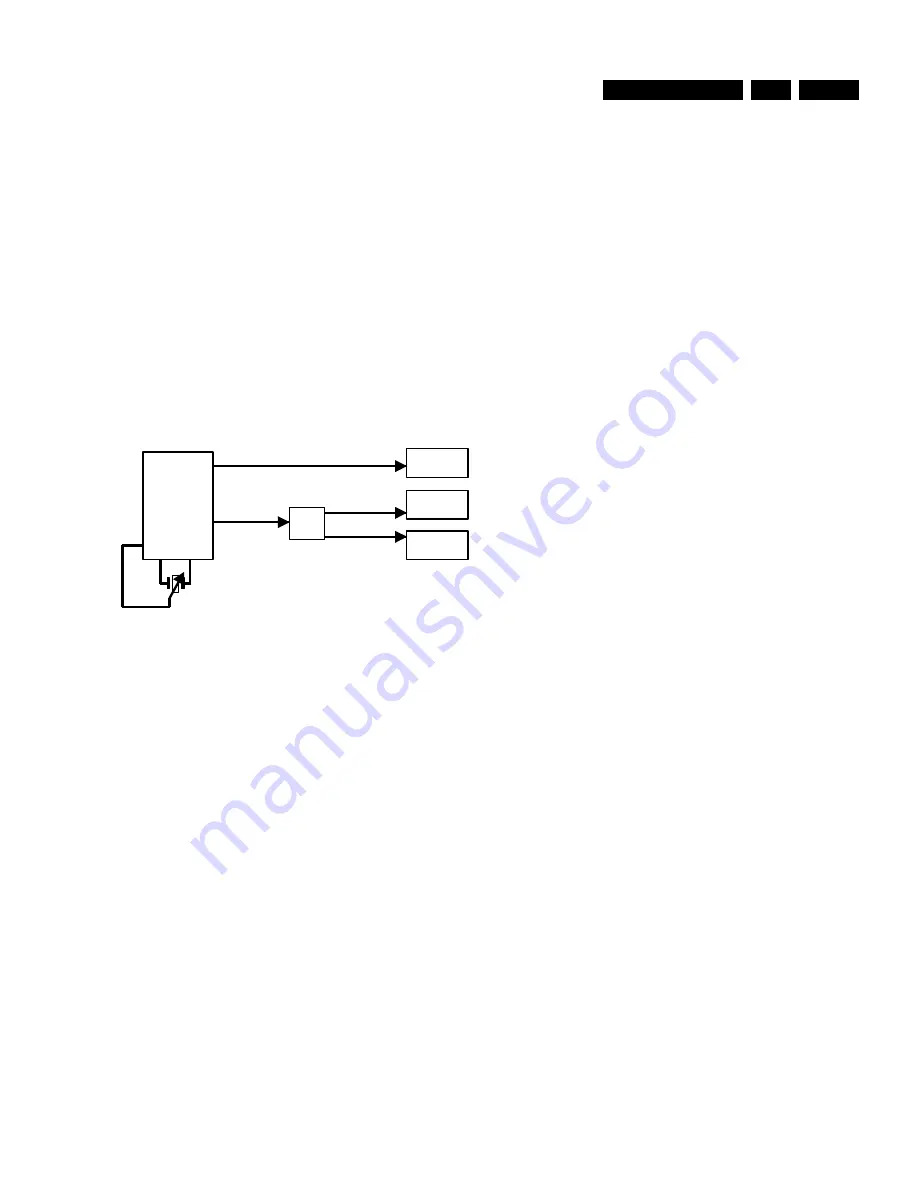
Service modes, repair tips and faultfinding trees
GB 23
CDR 3rd gen.
5.
The clockgeneration
All microprocessors or digital devices need a clock. The clock
is usually made by means of resonators or crystals depending
on the speed and the accuracy that is requested. The clock can
also differ from device to device so that more then one crystal
is needed. The cheapest and “system wise” best way is only 1
crystal. The derived clocks are then Phase related to each
other.
On the CDR MAIN 99 the DASP is generating all clock signals.
Not only the systemclock for the processor itself, but also for
the basic engine processor and even the systemclock for the
ADDA part which is directly related to the 44.1kHz. sample
frequency. To be able to do this a 33.8688Mhz. crystal with
25ppm accuracy is connected to the internal oscillator of the
DASP. Internal the clock signal is multiplied by means of a PLL.
This gives the systemclock on which the processor runs
internally. This systemclock is then again devided internally to
have the systemclock for the ADDA, which is 11.2896Mhz, and
the 16,9344Mhz. which divided by 2 gives the systemclock for
the BE part. In this way only 1 crystal is required. The same
8.4672MHz. is also routed to the CD-module in case of a
CDR775 player.
Figure 5-14
PC help on mainboard diagnostics
A couple of the diagnostics are only possible with the help of a
PC. The DASP micro controller will contain an interface with
the external world; this interface is realised via a serial RS232
connector that is accesible inside the player. It can be
accessed from the outside world by means of test pins and
connector 1818 and interface board 7104 086 91111.
Via those test pins a terminal emulator can be connected. Then
menus will come up that give the opportunity to enter all Audio
Engine commands. This includes the commands on Bit Engine
Level (transparant). This terminal emulator functionality is part
of the embedded software, so no external software is needed.
It can also read out the User Profile Logging of Bit Engine. This
can show the hours that the loader really was in recording
mode.
This diagnostic tool is activated if communication is detected
on the RS232 interface during power up. The baud rate for both
is 19k2 baud.
Details of the diagnostic tool are given in chapter 5.2.3 of this
publication: Menu Driven Diagnostics.
Also in preparation is the interactive COMPAIR tool. Then the
PC communicates in an active form with the set and compares
the result for making the next decision. With MDD the
technician has to take the next active step from his experiences
onwards.
5.2.3
Menu Driven Diagnostics
In this paragraph the specification of the software requirements
for the Menu Driven Fault Finding Diagnostics is given. It will
give a clear and unambiguous description of what the Menu
Driven Diagnostics (MDD) do.
NOTICE:THE TESTS, AS PROVIDED BY THE MENU
DRIVEN DIAGNOSTICS, ARE NOT SUPPOSED TO BE
MIXED RANDOMLY, ESPECIALLY TESTS LIKE ‘LASER ON’
AND ‘FOCUS ON’. IT IS ASSUMED THAT THE PERSON
THAT USES THE MDD KNOWS IN WHICH ORDER THESE
TESTS CAN BE EXECUTED.
The MDD module communicates with two entities:
the terminal emulator on the PC. The MDD receives
instructions (test to be executed) and transmits the menu to be
shown and the test results;
the Audio Engine module. It instructs the Audio Engine via the
interface field which test should be executed. The test result is
retrieved from the interface field.
Requirements
The functionality of the Menu Driven Diagnostics module is to
implement Menu Driven Diagnostics for service purposes.
When the CDR recorder is connected to a PC via an interface
board 7104 086 91111, connection cable 3104 157 11122 and
a RS232 cable (available at PC shop), the service technician
can select via a menu on the PC screen which test should be
perfomed. The result of the test is also shown on the PC
screen. No special test tool is needed for the PC; any terminal
emulation program can be used (for example, HyperTerminal
under Windows95/NT).
The last occurred error during a test session can be retrieved
via the menu.
The RS232 connector should be soldered to pins:
1818-1 = Rx
1818-4 = Gnd
1818-2 = Tx
General Constraints
It is advised to connect the connection cable 3104 157 11122
to the Mainboard connector 1818 mounted just under the
loader (topview). Via this cable also the powersupply for the
interface board 7104 086 91111 is arranged when it is
connected to connector 1000 on interfaceboard. To start this
application at powering on; for 5 seconds the Rx and Tx output
pin of the mainboard connector should be short circuited. This
temporarily short circuit indicates the internal CDR software
program to switch onto Menu Driven Diagnostics. This short cut
can easily be done via the switch (1009) on the interface board.
To communicate with the PC the RS232 cable has to be
connected to output connector 1010 on the interface board and
the switch (1009) should be released.
When switching on the CDR, two possibilities exist:
the RS232 cable is not connected. The application is executed
(no MDD mode);
the RS232 connector is connected; Rx and Tx are short
circuited for more than 5 seconds then the Menu Driven
Diagnostics is started. By connecting via connection cable to
interface and from there via the RS232 cable onto the PC, so
the MDD can transmit the main menu to the PC.
User Interfaces
RS232 interface
The CDR recorder transmits the menu to be shown and the test
results to the PC via connection cable 3104 157 11122,
interface board 7104 086 91111 and a RS232 cable. It receives
the selection of the user, chosen in the menu.
Hardware Interfaces
RS232 interface
The communication via RS232 should be set to the following
settings:
Baudrate:19200
Databits:8
Stopbits1
Parity:none
Handshaking:none
DASP
Master
processor
ADDA
Basic
engine
CD-
loader
/2
11.2896MHz.
(SYS_CLK_11M)
16.9344MHz.
(SYS_CLK_16M)
8.4672MHz.
(SYS_CLK_BE)
8.4672MHz.
(SYS_CLK_8W)
33.8688MHz.
25ppm.
CL96532133_028.eps
131299
Содержание CDR-775
Страница 5: ...Safety and Maintenance instructions warnings and notes GB 5 CDR 3rd gen 2 CL 96532086_023 eps 080999 ...
Страница 10: ...Mechanical instructions GB 10 CDR 3rd gen 4 Clamper Figure 4 7 CL06532018_007 eps 210200 ...
Страница 35: ...Circuit description GB 77 CDR 3rd gen 9 9 2 List of Abbreviations CL06532018_026 eps 290200 ...
Страница 36: ...Circuit description GB 78 CDR 3rd gen 9 CL06532018_027 eps 290200 ...
Страница 37: ...Circuit description GB 79 CDR 3rd gen 9 CL06532018_028 eps 290200 ...
Страница 38: ...Circuit description GB 80 CDR 3rd gen 9 CL06532018_029 eps 290200 ...
Страница 39: ...Circuit description GB 81 CDR 3rd gen 9 CL06532018_030 eps 290200 ...
Страница 40: ...Circuit description GB 82 CDR 3rd gen 9 CL06532018_031 eps 290200 ...
Страница 41: ...Circuit description GB 83 CDR 3rd gen 9 CL06532018_032 eps 290200 ...
Страница 42: ...Circuit description GB 84 CDR 3rd gen 9 CL06532018_033 eps 290200 ...
Страница 68: ...Electrical diagrams and PWB s GB 44 CDR 3rd gen 7 CDR MAIN BOARD TOP VIEW CL06532018_044 eps 290200 ...
Страница 69: ...Electrical diagrams and PWB s GB 45 CDR 3rd gen 7 CDR MAIN BOARD BOTTOM VIEW CL06532018_045 eps 030300 ...
Страница 80: ...Electrical diagrams and PWB s GB 56 CDR 3rd gen 7 CDR MAIN BOARD 7 TOP VIEW CL06532018_056 eps 290200 ...
Страница 81: ...Electrical diagrams and PWB s GB 57 CDR 3rd gen 7 CDR MAIN BOARD 7 BOTTOM VIEW CL06532018_057 eps 290200 ...
Страница 92: ...Electrical diagrams and PWB s GB 68 CDR 3rd gen 7 CDR MAIN BOARD 8 TOP VIEW CL06532018_069 eps 010300 ...
Страница 93: ...Electrical diagrams and PWB s GB 69 CDR 3rd gen 7 CDR MAIN BOARD 8 BOTTOM VIEW CL06532018_070 eps 010300 ...
Страница 98: ...Electrical diagrams and PWB s GB 74 CDR 3rd gen 7 CDR MAINBOARD SURVEY OF TESTPOINTS CL06532018_086 eps 010300 ...