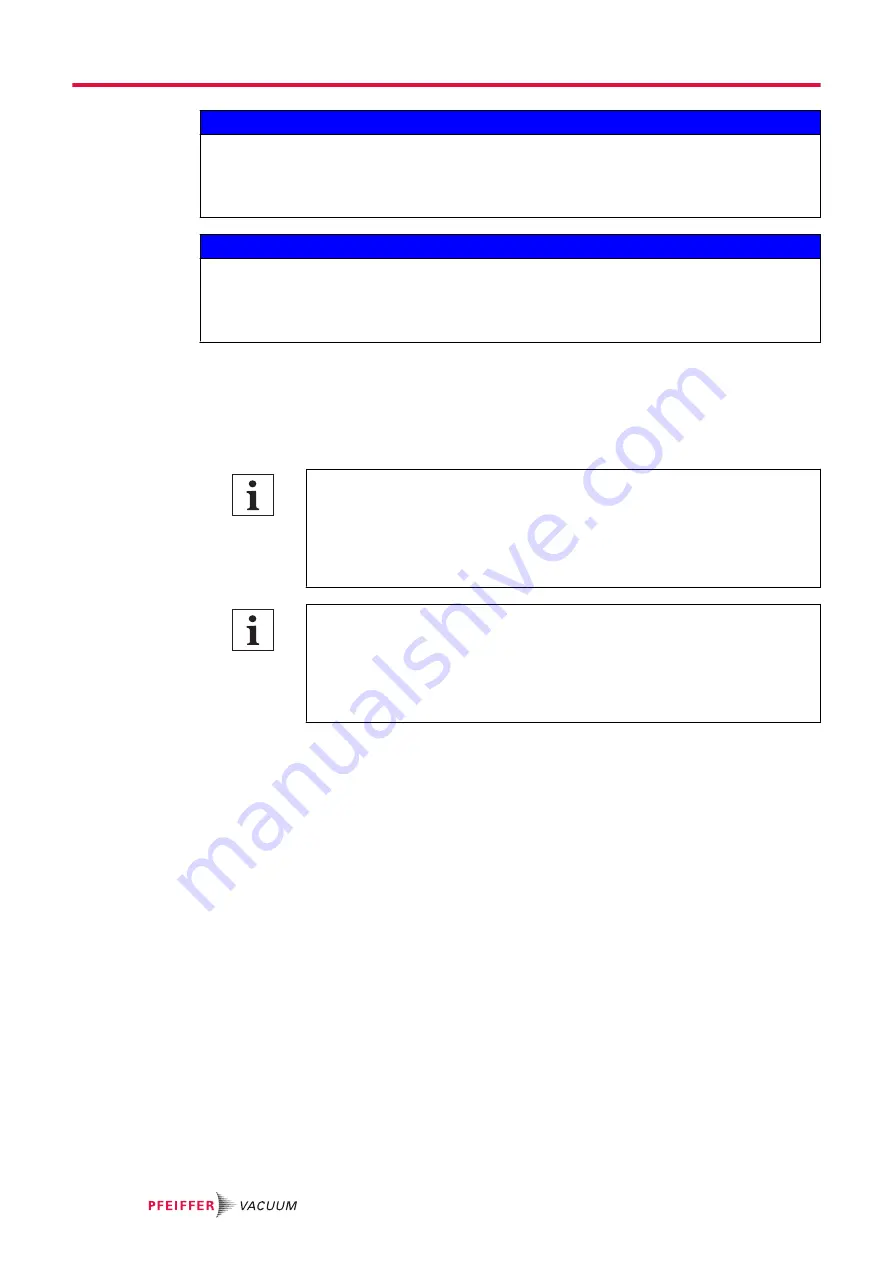
NOTICE
Damage caused by unsuitable cleaning agents
Unsuitable cleaning agents damage pump parts.
► Use only approved cleaning agents to clean pump parts.
► Never use soluble detergents.
NOTICE
Damage caused by unsuitable auxiliary tool
Using unsuitable tools damage the diaphragm and associated components.
► Never use the diaphragm key with auxiliary tools (for example pliers or an Allen key without tor-
que limitation).
2.3 Safety precautions
The product is designed according to the latest technology and recognized safety engineering rules.
Nevertheless, improper use can result in danger to operator all third party life and limb, and product
damage and additional property damage.
Information requirement on possible hazards
The owner or operator of the product is required to make all operating personnel
aware of hazards arising from the use of this product.
Every person who is involved in the installation, operation or maintenance of the
product must have read and understood the safety-relevant parts of this documen-
tation.
Infringement of EU conformity due to modifications to the product
The Declaration of Conformity from the manufacturer is no longer valid if the opera-
tor changes the original product or installs additional equipment.
● Following installation into a system, the operator is required to check and re-
evaluate as necessary the conformity of the overall system in the context of the
relevant EU Directives before commissioning that system.
General safety precautions for working with the pump
► Observe all applicable safety and accident prevention regulations.
► Check that all safety measures are observed at regular intervals.
► Do not expose body parts to the vacuum.
► Always ensure a secure connection to the earthed conductor (PE).
► Never disconnect plug connections during operation.
► Observe the above shutdown procedures.
► Keep lines and cables away from hot surfaces (> 70°C).
► Never fill or operate the unit with cleaning agents or cleaning agent residues.
► Do not carry out your own conversions or modifications on the unit.
► Observe the unit protection class prior to installation or operation in other environments.
► Observe statutory and local regulations regarding solvents handling.
► Never operate an open or faulty unit.
► Before carrying out any maintenance, first allow the unit to cool and disconnect it from the vacuum
equipment.
► Disconnect the pump from the mains prior to every intervention, and wait an additional five sec-
onds until the capacitors have discharged.
► Implement suitable safety precautions where unintentional pump venting can cause hazards.
– Power failures can cause unintentional venting.
2.4 Proper use
● You may use the pump exclusively for vacuum generation.
● You may not operate the pump with accessories not recommended by Pfeiffer Vacuum.
Safety
10/40