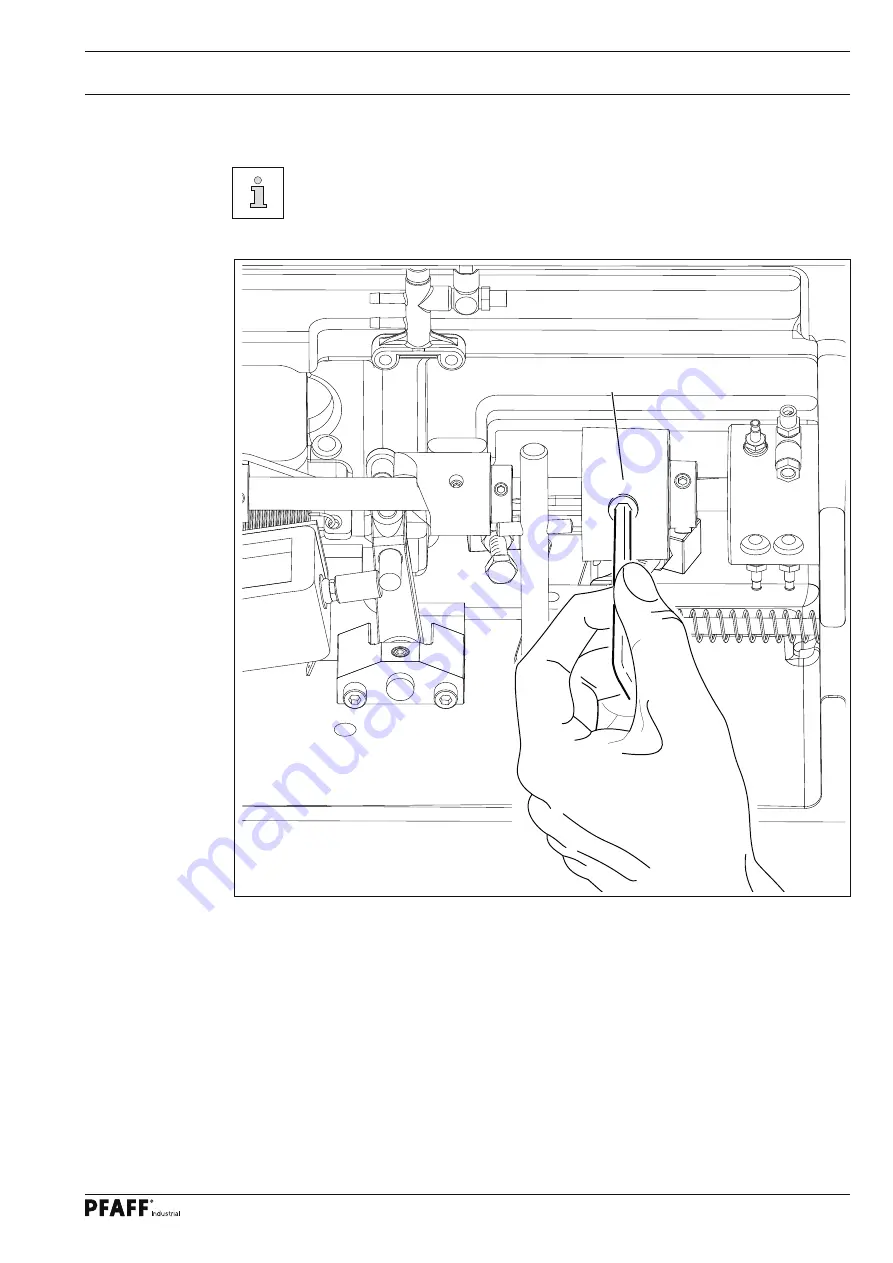
Adjustment
33
1
.05.25
Re-engaging the slip-clutch
Clutch
1
is adjusted at the works. In the case of a thread jamming, clutch
1
will
disengage, in order to avoid damage to the hooks.
The following describes how to re-engage clutch
1
.
●
Remedy jammed thread fault.
●
Hold clutch
1
fi rmly, as shown in Fig.
1
-
19
, and turn the balance wheel until clutch
1
re-engages.
Fig. 1 - 24
1
Содержание 2571ME PREMIUM
Страница 60: ...60 Circuit diagrams...
Страница 61: ...61 Circuit diagrams...
Страница 62: ...62 Circuit diagrams...
Страница 63: ...63 Circuit diagrams...