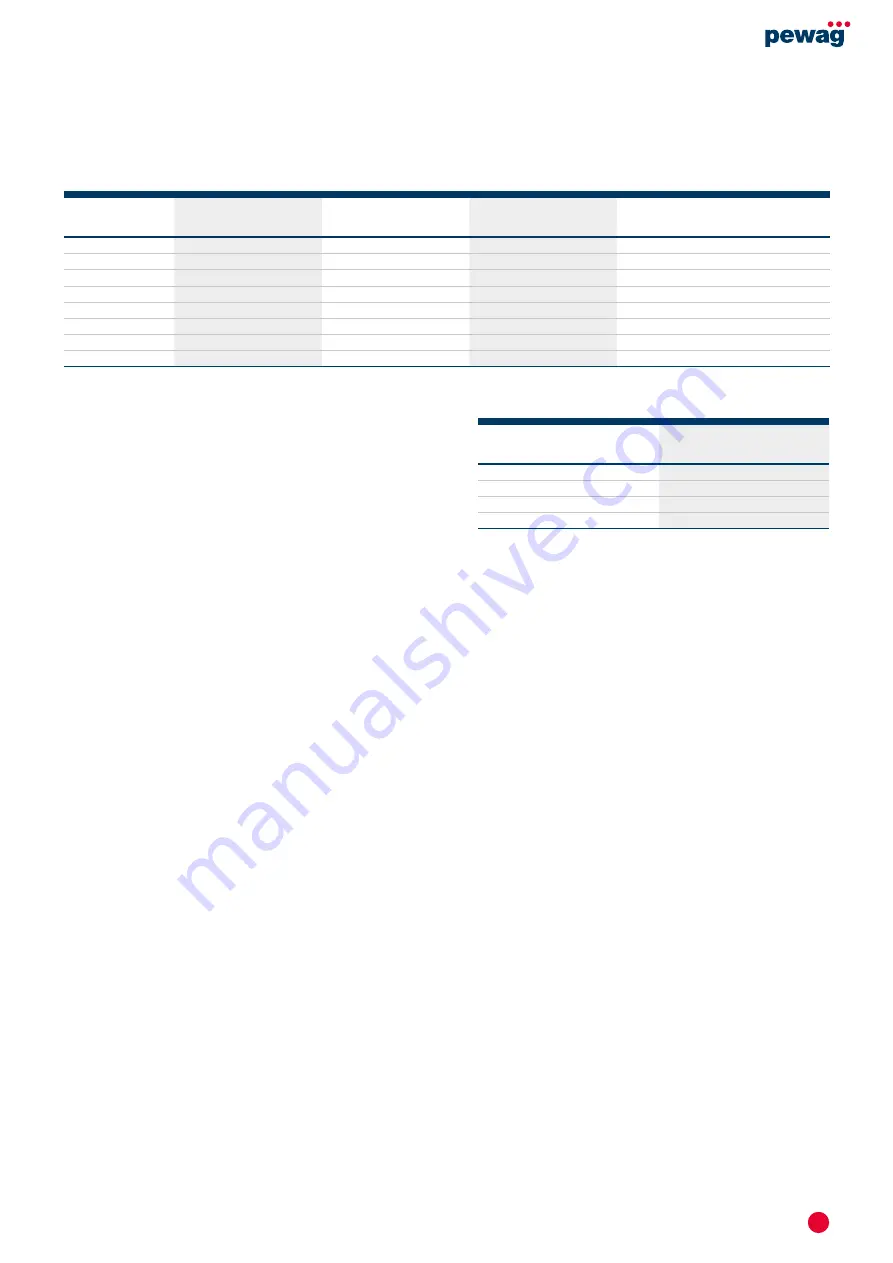
2
January 2016
Operating Manual pewag AOR lifting point – Grade 8
8. Maintenance
Check the AOR Lashing points visually at regular intervals.
The results of the inspection shall be entered into a register to
be prepared when the lifting point is first used.
This register includes characteristics of the lashing point as
well as identification particulars (Statement of compliance/
Inspection certificate).
An inspection must be carried out at least once a year or
more frequent if the AOR Lashing points are in heavy-duty
service. After three years at the latest the AOR Lashing points
shall be examined for cracks.
The condition of lashing point and its components must be
documented during these inspections. When making repairs
to AOR Lashing points note down the cause of the defect and
the remedial action that has been taken.
Immediately stop using AOR Lashing points that show the
following defects:
• deformation
• cuts, notches, cracks, incipient cracks
• AOR Lashing points cannot freely rotate or turn
• AOR Lashing points have been heated beyond permissible
limits
• severe corrosion
• wear exceeding 10 %, e.g. in the suspension link diameter
area
• identification marks are unreadable
• defect screws/bolts
Only use original spare parts and original screws and bolts
because these are made to meet special requirements. If
defects are detected make sure to repair the lashing point
before it is used again.
5. Characteristics
6. Mounting
Make sure the attachment faces are flat and dry and the
tapped hole is made perpendicular to the attachment face.
Mount the lifting point so that
• no areas of danger are created,
• structural parts cannot cause the suspension gear to be
deflected when the load is lifted
• the suspension gear cannot be damaged, e.g. by sharp
edges
The useful depth of the thread must enable the AOR Lashing
points to be safely screwed in. Make sure the tapped hole
is arranged at right angle to the attachment face on the
component. The depth of thread „L“ in the component must
at least be as follows:
L = 1 x d in steel
L = 1.25 x d in castings
L = 2 x d in aluminium
L = 2.5 x d in aluminium-magnesium alloys
(where L = depth of thread; d = thread diameter)
Make sure the threads of the lifting point and in the
component are clean and dry.
Tighten the screws at the tightening torques specified in
Chapter 5. If the AOR Lashing points are to remain on the
component make sure to use liquid agents to secure and
safeguard the screws. In case of through-bolting secure the
nuts by suitable locking means.
7. Application
The attachment link must always be freely movable. It
must not rest on or be supported by other structural parts.
When attaching the components make sure the position
of the lashing point always enables forces to be exerted in
longitudinal direction. Check the correct positioning of the
AOR Lashing points each time the load is lifted, especially
when the load is applied parallel to the screw-on surface.
The permissible carrying capacity of the AOR Lashing points
reduces at elevated temperatures. The reduced carrying
capacity figures shown in the following table shall only apply
for short-term use at the temperatures indicated.
In case the points shall be used under the influence of
chemicals please consult with the manufacturer.
Code
Working load limit
[t]
Fastening torque
[Nm]
Usable thread
Screw dimension
AOR 10
3.15
170
M16 x 25
M16 x 45 DIN 7984-10.9
AOR 13
5.3
350
M20 x 36
M20 x 60 DIN 7984-10.9
AOR 16
8
950
M30 x 50
M30 x 80 DIN 7984-10.9
AOR 22
15
1,900
M36 x 53
M36 x 90 DIN 7984-10.9
AOR 26
21.2
2,100
M42 x 67
M42 x 100 DIN 7984-10.9 – Special
AOR 28
25
2,400
M45 x 67
M45 x 110 DIN 7984-10.9 – Special
AOR 32
31.5
3,200
M56 x 88
M56 x 135 DIN 7984-10.9 – Special
AOR 34
32
3,200
M56 x 88
M56 x 135 DIN 7984-10.9 – Special
Temperature range [°C]
Remaining carrying capacity
-20 °C up to 100 °C
100 %
100 °C
up to
200 °C
85 %
200 °C
up to
250 °C
80 %
250 °C
up to
300 °C
75 %