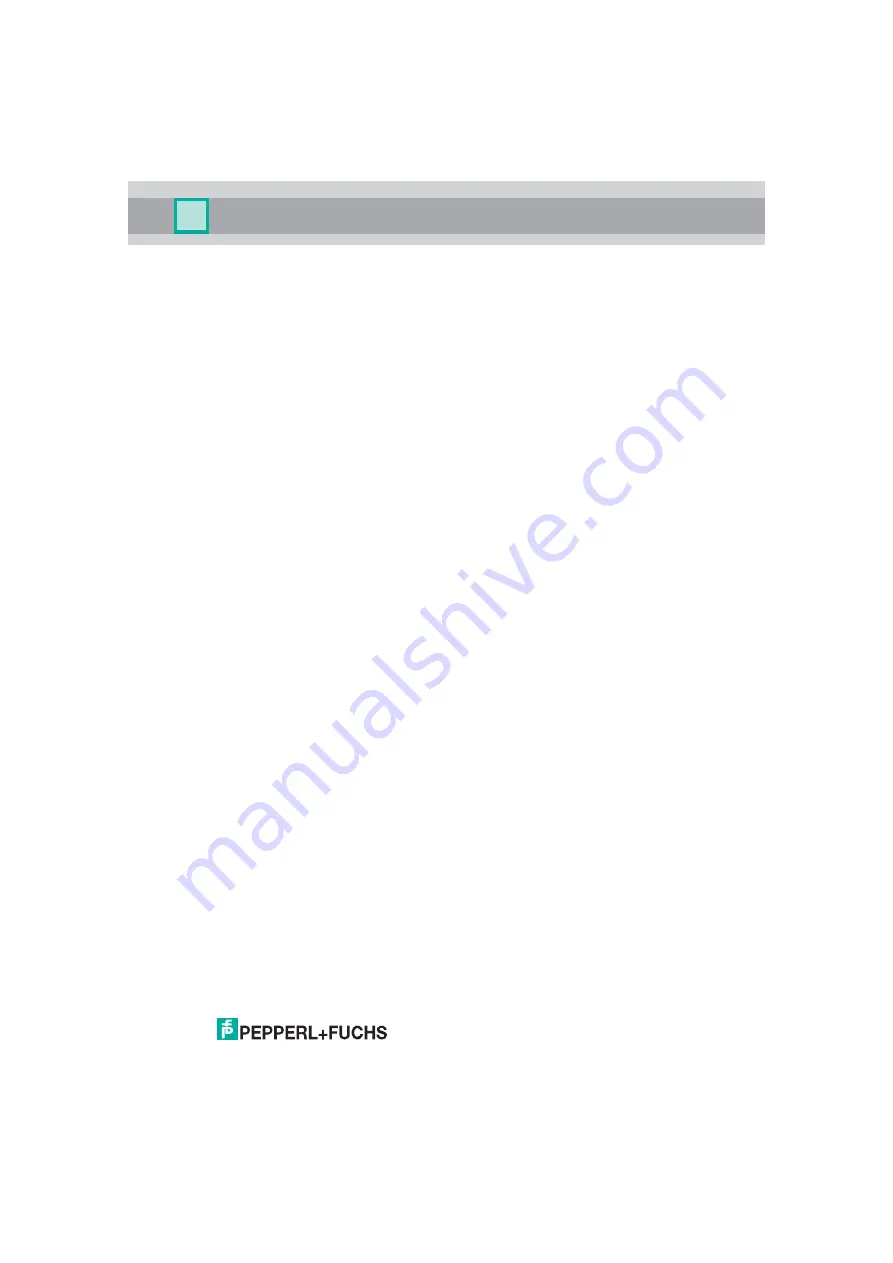
Functional Safety HiD2035, HiD2036
Planning
20
16-
06
13
3.5
Useful Life Time
Although a constant failure rate is assumed by the probabilistic estimation this
only applies provided that the useful lifetime of components is not exceeded.
Beyond this useful lifetime, the result of the probabilistic estimation is
meaningless as the probability of failure significantly increases with time. The
useful lifetime is highly dependent on the component itself and its operating
conditions
–
temperature in particular. For example, the electrolytic capacitors
can be very sensitive to the operating temperature.
This assumption of a constant failure rate is based on the bathtub curve, which
shows the typical behavior for electronic components.
Therefore it is obvious that failure calculation is only valid for components that
have this constant domain and that the validity of the calculation is limited to the
useful lifetime of each component.
It is assumed that early failures are detected to a huge percentage during the
installation and therefore the assumption of a constant failure rate during the
useful lifetime is valid.
However, according to IEC/EN 61508-2, a useful lifetime, based on general
experience, should be assumed. Experience has shown that the useful lifetime
often lies within a range period of about 8 ... 12 years.
As noted in DIN EN 61508-2:2011 note N3, appropriate measures taken by the
manufacturer and plant operator can extend the useful lifetime.
Our experience has shown that the useful lifetime of a Fuchs product
can be higher
• if there are no components with reduced life time in the safety loop (for
example electrolytic capacitors, relays, flash memories, optocoupler) which
can produce dangerous undetected failures and
• if the ambient temperature is significantly below 60
°
C.
Please note that the useful lifetime refers to the (constant) failure rate of the
device. The effective life time can be higher.