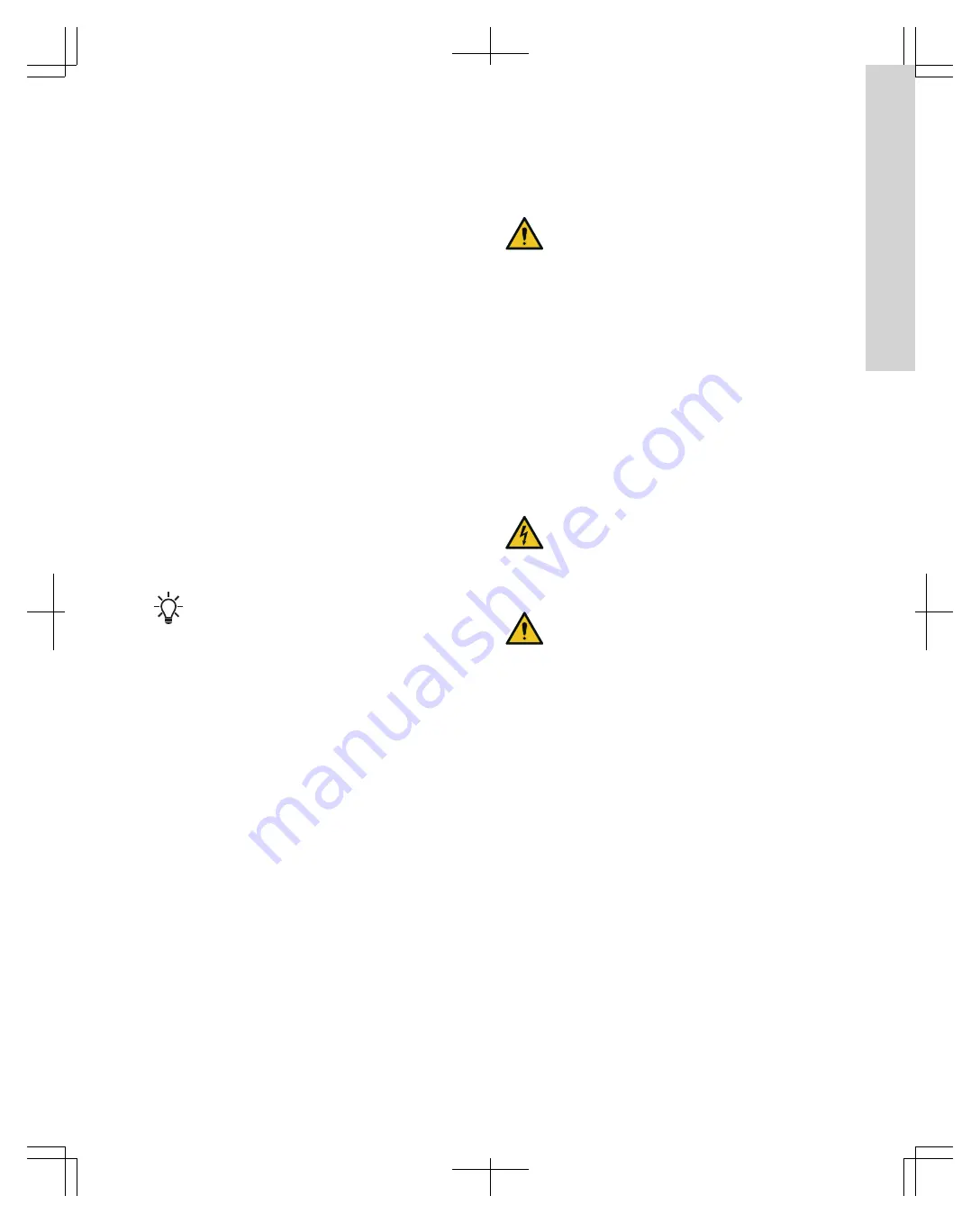
5.
Gauges (if used) of correct range and in good condition.
6.
All foundation, pump, and driver bolts properly tightened. All
external fasteners (nuts, bolts, screws) on pump checked
against recommended torque values.
7.
When possible, turn the pump shaft by hand to make sure that
parts do not bind.
8.
Ensure the suction valve is fully open.
After the pump has run a reasonable time, measure the
temperature of bearing and stuffing box housings. The
temperature of the stuffing box should approximate that of the
pumped liquid. In case of overheating, the packing will become
too tight and must be checked.
5
.4.2
Air in the system
Entrained air reduces pump total head and flow rate. To avoid air in
the system, follow these precautions:
•
Return lines into tanks should terminate a minimum of two pipe
diameters below the low liquid level.
5
.4.3
Checking the driver lubrication
Before running the drivers either separately or connected to the
pump:
1.
Follow the driver manufacturer instructions for lubrication
requirements.
The driver is pre-lubricated from the factory.
2.
Ensure that the grease-lubricated bearings in the driver have
been properly greased with the grade of grease recommended
by the driver manufacturer.
5
.4.4
Driver settings
Refer to the manufacturer's instructions.
5
.4.5
Pump performance
Initial field test data becomes a valuable baseline for
future troubleshooting and maintenance. It may not be
possible to match the factory performance due to
differences in system resistance.
Once the pump is operating, verify the following:
1.
The pipe connections are tight, and no leaks are present.
2.
The following attributes match the pump nameplate:
a. operating speed
b. flow rate
c. inlet and outlet pressure
d. power input, P1.
5
.4.6
Before starting the pump
1.
Never operate or spin the pump unless it is fully primed. (See
"
2.
Turn the shaft by hand to see that it rotates freely.
3.
Check that the voltage and frequency on the motor nameplate
match the current supply.
4.
Be sure the motor is wired for correct voltage.
5.
Check that all thermal overload relays are of the proper size
and "set" for operation.
6.
Be sure the valve in the suction line is open. The discharge
valve should be closed.
7.
Review the remaining instructions.
5
.4.7
After starting the pump
CAUTION
Equipment damage and malfunction
Minor or moderate personal injury
‐
Overheating will result if pump is operated against a
closed valve for more than a few minutes. If closed
valve operation is required, install a by-pass line or a
small relief valve discharging back to the pump
suction. Suction valve should not be used to regulate
flow of the pump. Suction valve should be wide open
during pump operation and flow is to be regulated by
the discharge valve. Failure to adhere to these
precautions can result in equipment damage and
malfunction.
1.
Check the pump rotation with the direction of the arrow on the
pump casing. If necessary, change direction.
2.
Check the pump for evidence of rubbing or binding which may
have been caused by piping strains.
3.
Slowly open the discharge valve.
4.
See that all pipe connections are tight.
6
. Service
6
.1
Maintenance
WARNING
Electric shock
Death or serious personal injury
‐
Never do maintenance work when the unit is
connected to power.
WARNING
Crushing hazard
Death or serious personal injury
‐
Make sure all persons stand clear of the load and the
lifting equipment while product is lifted, lowered,
loaded and unloaded. Do not allow anyone to stand
on, under, or near the load.
6
.2
Maintenance schedule
To ensure the pumping equipment is operating efficiently, perform
frequent inspection and periodic maintenance. An inspection and
maintenance log must be maintained and any issues must be
reported by the inspector immediately. A suggested guide for
preventative maintenance for normal applications is given below.
Unusual applications with abnormal heat, moisture, dust, etc., may
require more frequent inspection and service.
1
5
English (US)