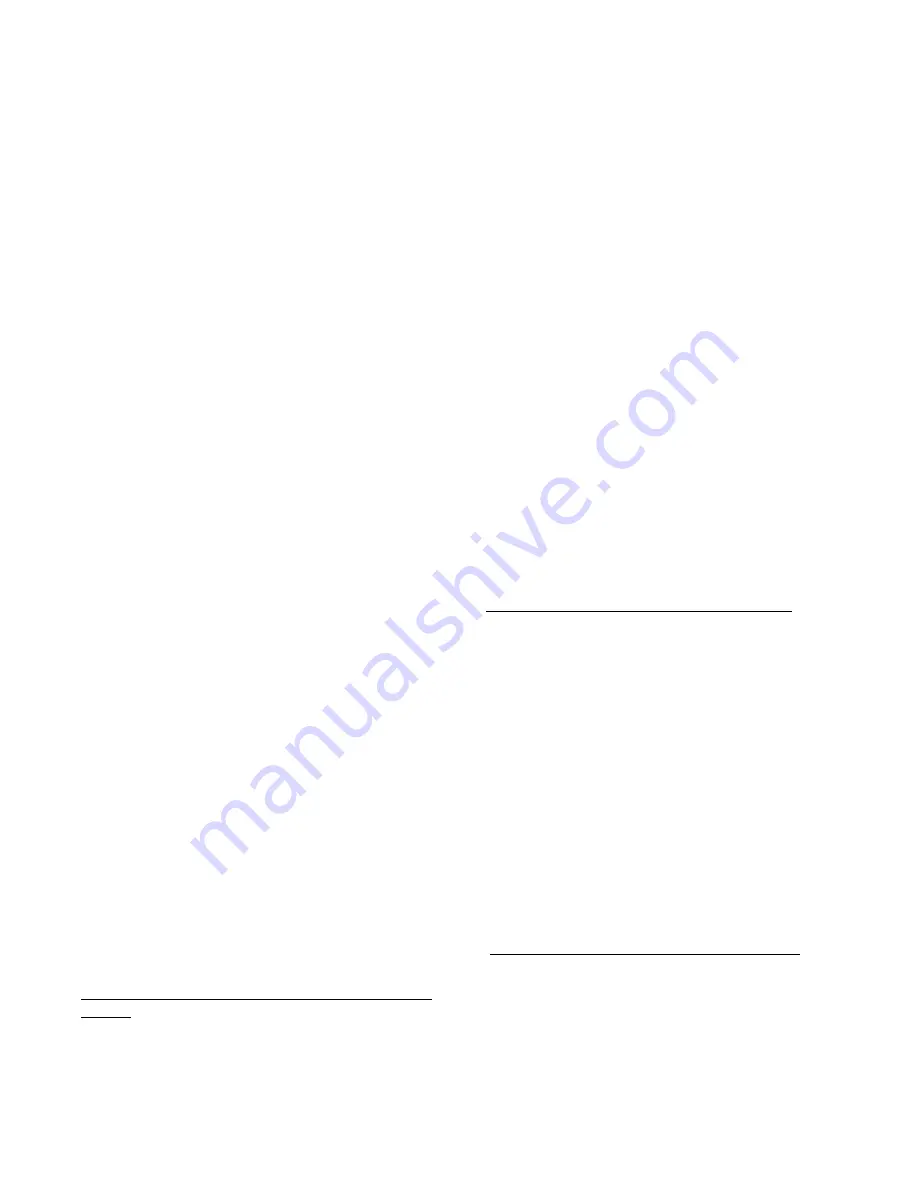
1
General
OPERATING GUIDE
for use with
High Sensitivity DC ACCELEROMETERS
SPECIFICATION SHEET, INSTALLATION DRAWING
AND CALIBRATION INFORMATION ENCLOSED
PCB ASSUMES NO RESPONSIBILITY FOR DAMAGE CAUSED TO THIS PRODUCT AS A RESULT OF PROCEDURES THAT ARE
INCONSISTENT WITH THIS OPERATING GUIDE.
1.0 INTRODUCTION
Congratulations on the purchase of a quality, DC
acceleration sensor. PCB’s high sensitivity DC
accelerometers
provide
optimal
performance
characteristics in a high quality package. In order to
ensure the highest level of performance for this product, it
is imperative that you properly familiarize yourself with
the correct mounting and installation techniques before
attempting to operate this device. If, after reading this
manual, you have any additional questions concerning this
sensor or its application, feel free to call a factory
Application Engineer at 716-684-0001 or your nearest
PCB sales representative.
2.0 HIGH SENSITIVITY DC ACCELEROMETERS
High sensitivity DC accelerometers are devices which
require stable power. Unlike standard non-amplified
piezoresistive accelerometer designs, this stable power is
provided by an internal voltage regulator. Therefore
PCB’s high sensitivity DC accelerometers may be
supplied with a positive unregulated DC supply voltage,
provided it falls within the specified range of the
particular model number. The change in the silicon strain-
sensing element is approximately proportional to the
applied acceleration. The sensor element is electrically
connected in a Wheatstone-bridge circuit. The integral
amplifier provides a low impedance output to follow-on
instrumentation. These particular accelerometers provide
a dc or steady state acceleration measurement capability
as opposed to a predetermined low frequency cut off
associated with charge or ICP
®
type accelerometers.
Examples where High Sensitivity DC accelerometers may
be used:
Automotive Crash Simulation Sleds
Automotive Road / Load Rigs
Aircraft Flutter, Load Testing
Whole-Body Vibration Studies
Lower range, higher sensitivity DC accelerometers, allow
for simple 2 g turn-over testing as a means of determining
the health of the unit prior to use. By simply placing the
unit in a +1g position and noting the output, then turning
the unit on its side to the null position and noting the 0g
output error, followed by the same technique, only in the
-1g position, the user can verify the health of the
accelerometer. The +1g, null and -1g values are now
apparent to the user.
General High Sensitivity DC Accelerometer Terms
Excitation-
+ 10 V dc typical.
Sensitivity-
mV/g
ZMO-
Zero Measurand Output
(mV output with
no acceleration applied)
TSS-
Thermal Sensitivity Shift
(sensitivity
variation due to temperature change)
TZS-
Thermal Zero Shift (
ZMO variation due to
temperature change)
Resolution
Minimum acceleration measurement
level based on output sensitivity and
inherent noise floor of accelerometer
High Sensitivity DC Accelerometers typically have:
Low-impedance output signal
Steady-state acceleration measurement capability
Stable operation over temperature
Low cross axis sensitivity