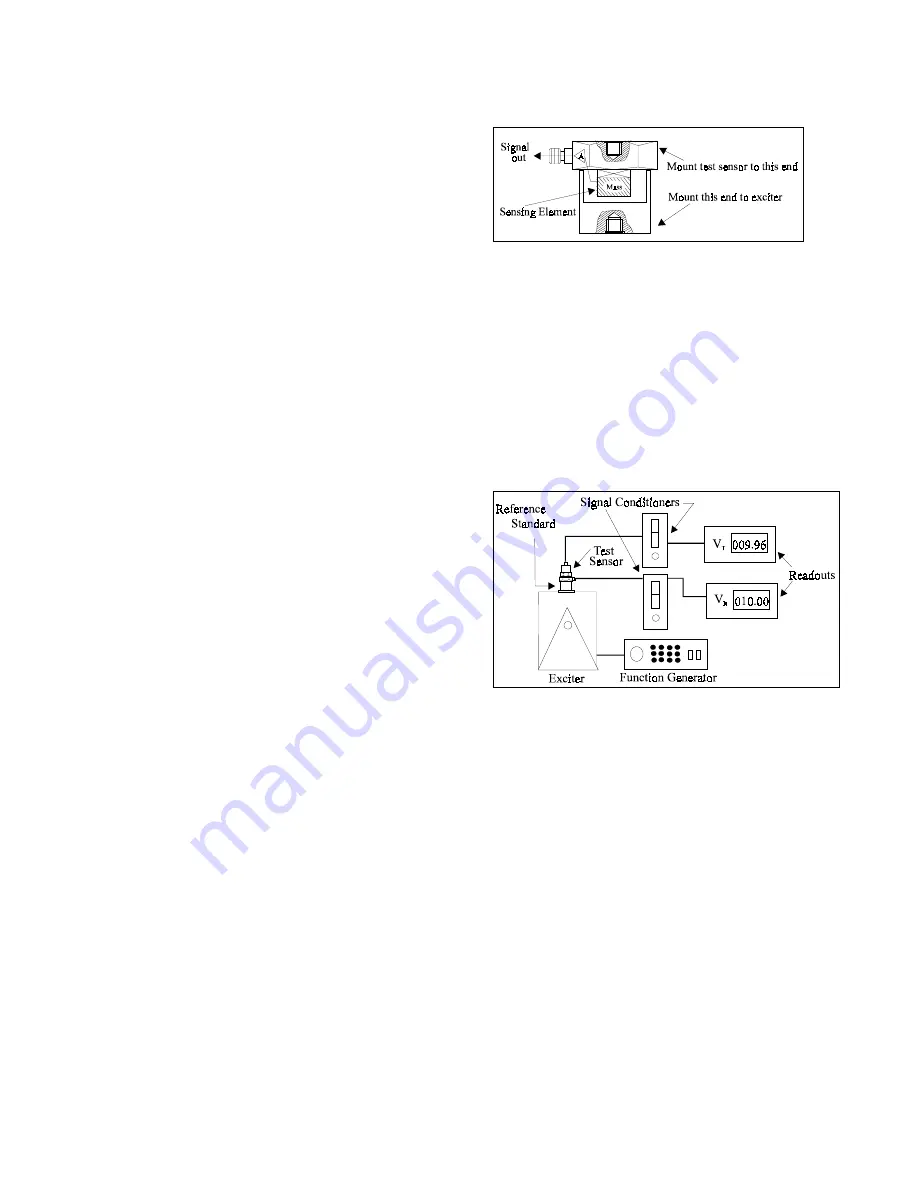
5
For these reasons, it is recommended that a recalibration
cycle be established for each accelerometer.
This
schedule is unique and is based on a variety of factors,
such as extent of use, environmental conditions,
accuracy requirements, trend information obtained from
previous calibration records, contractual regulations,
frequency of “cross-checking” against other equipment,
manufacturer recommendation, and any risk associated
with incorrect readings. International standards, such as
ISO 10012-1, provide insight and suggested methods for
determining recalibration intervals for most measuring
equipment.
With the above information in mind and
under “normal” circumstances, PCB conservatively
suggests a 12- to 24-month recalibration cycle for most
piezoelectric accelerometers.
Note:
It is good measurement practice to verify the
performance of each accelerometer with a Handheld
Shaker or other calibration device before and after each
measurement.
The PCB Model 394C06 Handheld
Shaker operates at a fixed frequency and known
amplitude (1.0 g) to provide a quick check of sensor
sensitivity.
7.1 SENSOR RECALIBRATION
Accelerometer
recalibration
services
are
typically
performed by PCB’s internal metrology laboratory.
(Other international and private laboratories are also
available.) The PCB laboratory is certified to ISO 9001,
accredited by A2LA to ISO 17025, complies with ISO
10012-1 (and former MIL-STD-45662A), and uses
equipment directly traceable to N.I.S.T. This assures an
accurate calibration of relevant specifications.
In addition, many companies choose to purchase the
equipment necessary to perform the recalibration
procedure themselves. While this may result in both a
savings of time and money, it has also been attributed to
incorrect readings and costly errors. Therefore, in an
effort to prevent the common mistakes associated with
customer-performed calibration, this document includes
a broad overview of the Back-to-Back Calibration
technique.
This technique provides a quick and easy
method for determining the sensitivity of a test
accelerometer over a wide frequency range.
7.2 BACK-TO-BACK CALIBRATION THEORY
Back-to-Back Calibration is perhaps the most common
method for determining the sensitivity of piezoelectric
accelerometers.
This method relies on a simple
comparison to a previously calibrated accelerometer,
typically referred to as a reference standard.
Figure 9.
Reference Standard Accelerometer
These
high-accuracy
devices,
which
are
directly
traceable to a recognized standards laboratory, are
designed for stability, as well as configured to accept a
test accelerometer. By mounting a test accelerometer to
the
reference
standard
and
then connecting this
combination to a suitable vibration source, it is possible
to vibrate both devices and compare the data as shown
in Figure 10. (Test set-ups may be automated and vary,
depending on the type and number of accelerometers
being calibrated.)
Figure 10.
Typical Back-to-Back Calibration System
Because the acceleration is the same on both sensors,
the ratio of their outputs (V
T
/V
R
) must also be the ratio
of their sensitivities.
With the sensitivity of the
reference standard (S
R
) known, the exact sensitivity of
the test sensor (S
T
) is easily calculated by using the
following equation:
S
T
= S
R
(V
T
/V
R
)
By varying the frequency of the vibration, the sensor
may be calibrated over its entire operating frequency
range.
The
typical
response
of
an
unfiltered
accelerometer is shown in Figure 11.
Содержание 356A70
Страница 12: ......