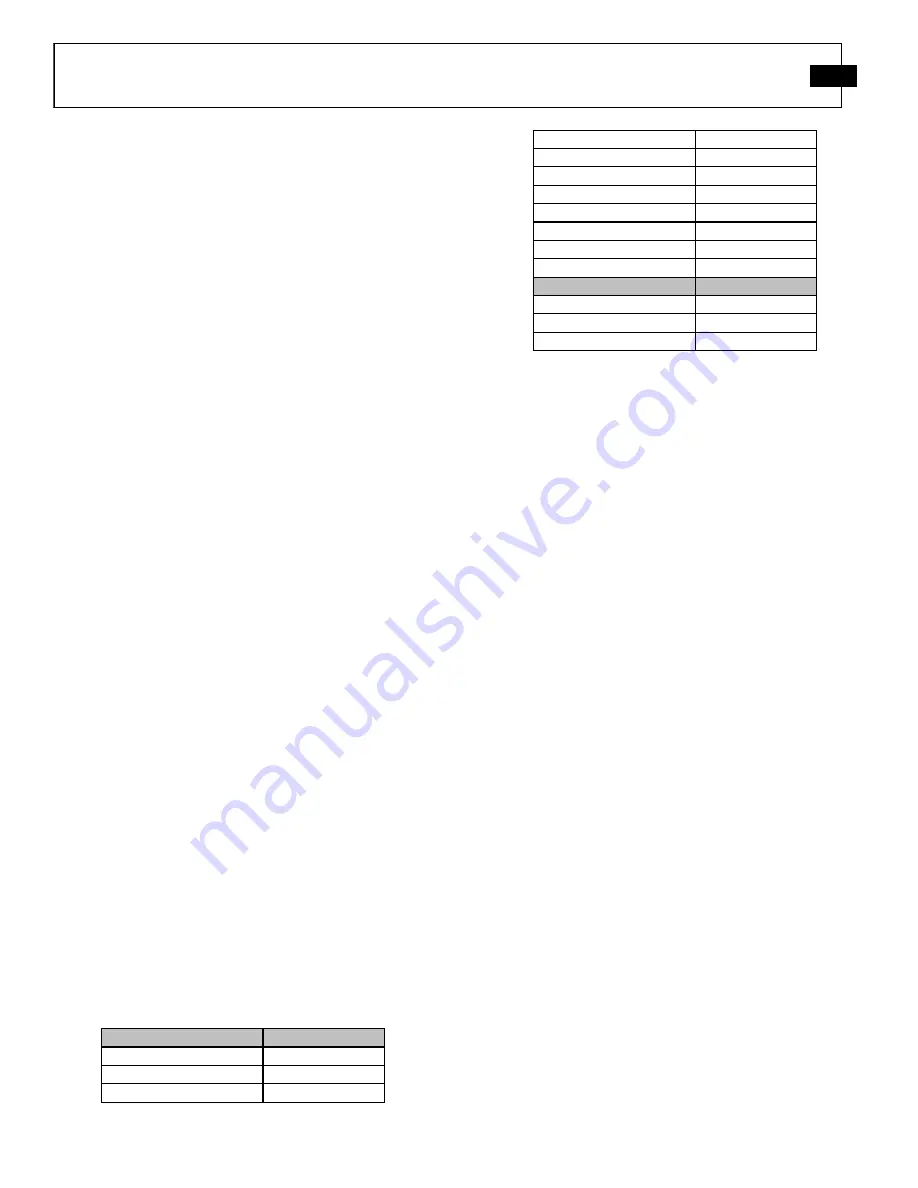
ICP
FORCE SENSOR OPERATION MANUAL
7
traceable reference sensor. Generally, a preload of 20% (full
scale operating range of the force ring) is applied before
recording of measurement data. Allow the static component of
the signal to discharge before calibration.
3-component force sensors must be preloaded to achieve proper
operation, particularly for the shear x-, and y-axis. This preload
provides the sensing crystals with the compressive loading
required to achieve an output in response to shear direction
input forces. The recommended applied preload in the z-axis
for 3-component force sensors is 10 times the desired
measurement range in the x or y-axis. This higher level z-axis
preload is required as the resultant output in the x and y axis is
a result of friction generated on the internal crystals specifically
cut to provide output in the x or y axis.
As an example, to maximize the sensors output in all three
(3ea) axis of a 1000 lb (4500 N) triax load cell, a preload of
5000 lbs (22K) should be applied, This will enable
measurements in the x and y axis to be 500 lbs (2225 N).
Please refer to the specific model specifications for the
recommended preload. A preload chart in Figure 14 is also
provided for quick reference.
As with force rings, the sensitivity achieved from a 3-
component force sensor is dependent upon the applied preload
and the elasticity characteristics of the mounting bolt or stud
used. If the unit is to be installed with a stud or bolt other than
the supplied elastic, beryllium copper stud, a calibration using
the actual mounting hardware is recommended to be performed.
Errors in sensitivity of up to 50% can result by utilizing studs
or bolts of different materials.
When installing ICP
ring and 3-component type sensors, a
PCB signal conditioner with at least one channel of DC
coupling capability is recommended to properly monitor sensor
output voltage as it corresponds to the desired preload. A DC-
coupled signal conditioner will provide a longer system
discharge time constant, which will result in slower signal
decay. When used with a DVM or similar readout device, the
installer can monitor the sensor output voltage directly for
correct preloading.
Monitor the output from the Z-axis connector when preloading
3-component type sensors. These sensors require a preload in
the Z-axis that is 10 times their shear range. Some models
require this to be accomplished in steps, not to exceed the usable
voltage. To prevent
“
clipping
”
of the signal, increments should
not exceed 10 VDC.
Force Ring Models
Pre-Load (lbs)
201B01
60
201B02
100
201B03
200
201B04
400
201B05
1,000
202B
2,000
203B
4,000
204C
8,000
205C
12,000
206C
16,000
207C
33,750
3-Component Models
260A01
5,000
260A02
10,000
260A03
40,000
Figure 14 - ICP
Force Sensor Preload Requirements
WORKING RANGE, PRELOAD, AND MAXIMUM
LOAD RELATIONSHIP IN RING STYLE and Triaxial
FORCE SENSORS
The
Working Range
is the ideal dynamic working load that
may be applied to a sensor during operation. In most sensors,
the product of the working range and the sensor sensitivity
will provide a 5 Volt output, following the equation;
5Volts = range x sensitivity.
The
Sensor Preload
is the load applied to the sensor before
the sensor is used in an operation. In ring and triax models,
preload is essential to match PCB’s calibrated sensitivity as
well it assure sensor linearity at the lower measurement range.
The
Maximum Load
is the dynamic load that may be applied
before the sensor approaches physical damage. In some
sensors this value is a result of a mechanical limitation. In
ICP® models this may be an electrical limitation (applying an
excessive load under sudden dynamic condition outside the
specified range may damage the internal electronic circuitry).
With most sensors, the specified dynamic working range and
maximum compression is riding ON TOP OF the applied
preload. As an example, triax force sensor Model 260A01
has a specified preload of 5000 lbs (22kN), a working range of
1000 lb (4500N), and a maximum compression range of 1320
lbs (6000 N). To provide the best linear response of the sensor,
a 5000 lbs (22kN) preload should be loaded on it. From there
one may take dynamic measurements through the entire 1000
lb (4500N) working range of the sensor. Dynamically one
should not take measurements above 1320 lbs (6000) as this
total load value approaches physical damage to the sensor.
5.0 OPERATION
APPLICATION OF A FORCE