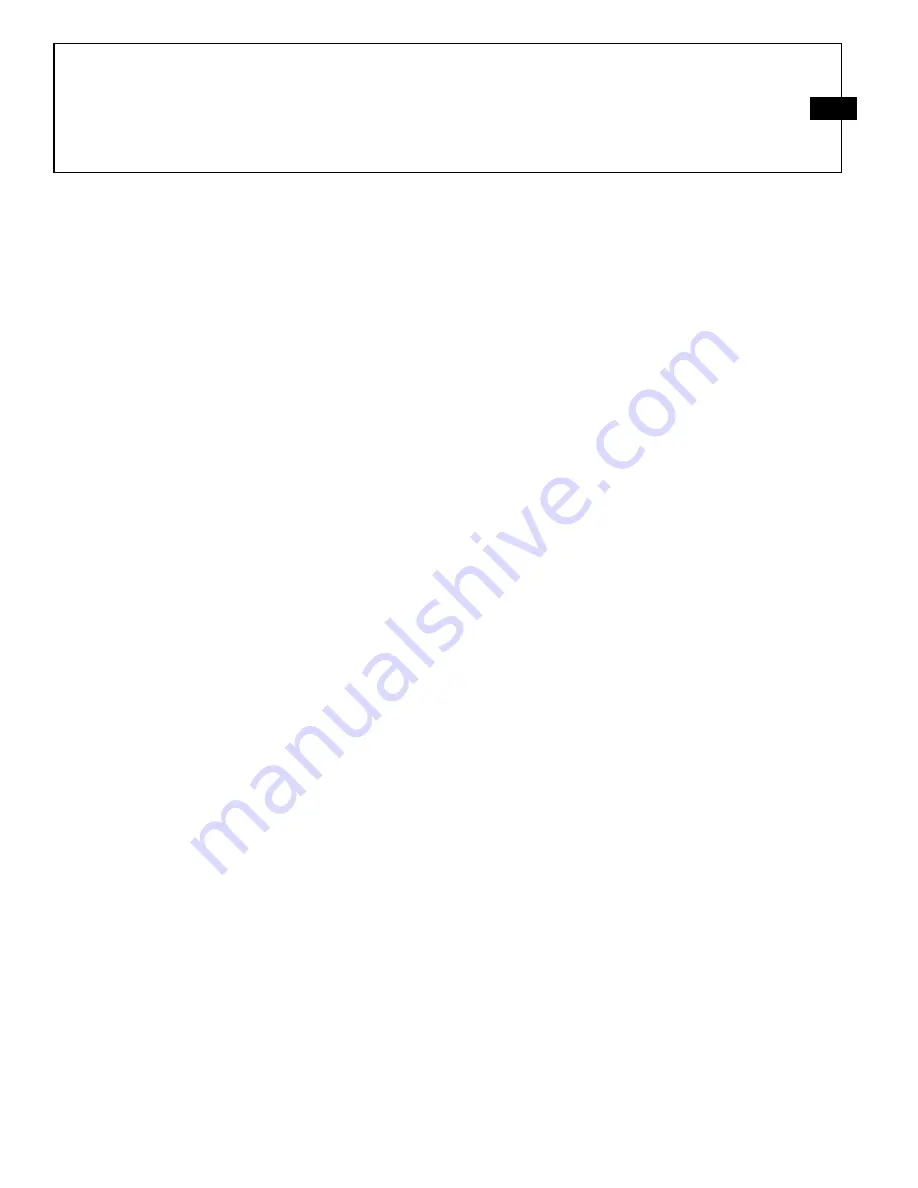
Drawing Number: 21091
ECO: 52570
Revision: B
OPERATION MANUAL FOR
HELIUM BLEED WATER-COOLED
PRESSURE SENSORS
123 Series
3
level to zero out quickly without effect on the
dynamic level indicated.
Also, the influx of large amounts of thermal energy,
as in rocket combustion measurements, can cause the
sensor to generate spurious transient outputs of
considerable magnitude. Using the charge amplifier
on "SHORT" TC alleviates this problem by shunting
these longer term charge outputs to ground while
measuring the faster dynamic pressure pulses.
4.3
OPERATION - ICP
MODELS
Consult Guide G-0001B for a complete description of
the low-impedance concept in instrumentation.
All PCB power units designed for ICP
use contain
built-in fault monitor meters to aid in locating circuit
faults (shorts or opens) and to identify normal
operation of the miniature impedance-converting
amplifier built into the sensor.
Do not attempt to apply voltage directly to the input
pin of the sensor from any other power source. The
input current must be limited to 20 mA maximum and
the input voltage must not be higher than 28 VDC.
Consult the factory if it is desired to build a power
unit rather than to use one of those available from
PCB.
NOTE: Full-scale range is 1imited by the helium
source pressure. The applied helium source pressure
level must be at least twice the peak combustion
pressure (not to exceed 15,000 psi), and not more
than 10 times the lowest expected peak combustion
pressure. This is true for all models, charge or ICP
.
5.0
CALIBRATION
5.1
CHARGE MODEL
To calibrate this model, install in pressure port of
dead weight tester and apply various static pressures,
recording corresponding outputs at each pressure of
interest.
Discharge the charge amplifier before each reading
and return pressure to zero before each new pressure
input. Use the charge amplifier on “LONG” time
constant and keep cables and connections clean to
avoid drift. A DC digital voltmeter is ideal for
readout during calibration.
NOTE: The helium tube must be plugged with a
pressure-tight seal before attempting to calibrate to
avoid losing pressure through the helium tube.
If a hydraulic calibration system is used, be sure to
remove all traces of oil from the diaphragm passage
after calibration. Pneumatic systems are preferred for
calibration.
5.2
ICP
MODELS
Because of the shorter time constants built into these
models, static calibration methods are much more
difficult to use. Pressures must be applied rapidly
and readout must be made with fast recording devices
such as light beam oscillographs or storage
oscilloscopes.
A pneumatic (compressed air or hydrogen) system
with quick opening valve and reference gage is an
excellent method of calibrating these sensors.
MAINTENANCE
The sealed construction and miniature size of these
sensors make field repair impractical.
The helium filter element should be cleaned should
the flow rate decrease. Remove the element and
ultrasonically agitate in solvent for 15 minutes, then
dry.
Should the orifice become plugged, back pressure the
orifice by applying air pressure to diaphragm end of
sensor with filter off and helium tube vented to
atmosphere.
The only maintenance possible on the probe is
maintaining of insulation resistance of the charge
mode models. Clean connectors with suitable solvent
and dry.
Contact factory for assistance should problems arise.
ICP is a registered trademark of PCB Piezotronics