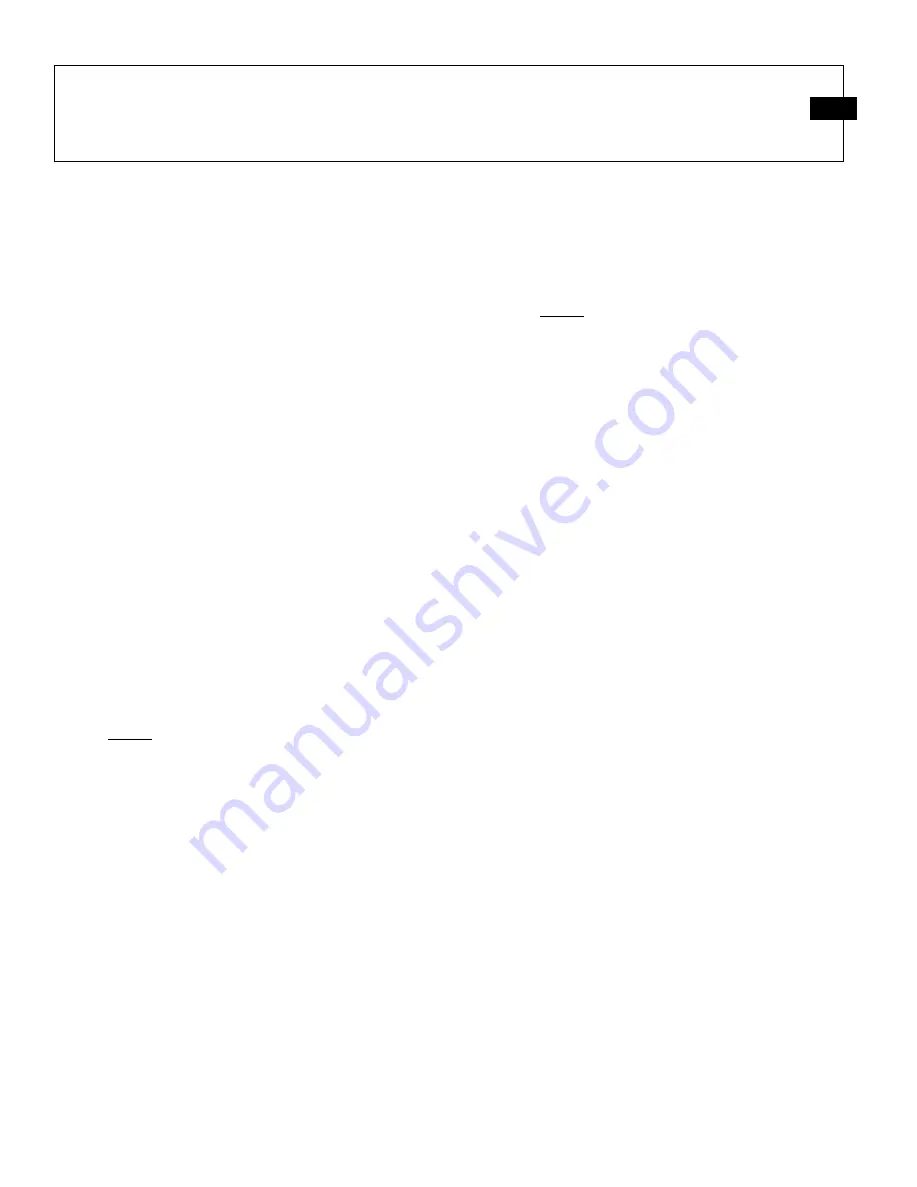
Drawing Number: 21086
Revision: NR
OPERATION MANUAL FOR
CONFORMAL BALLISTICS PRESSURE SENSOR
Series 117B
2
the curvature. In these latter cases, the
sensor forward side is identified with the
legend
“
FWD
”
etched on the guide collar to
which the slotted clamp is attached. The
clamp must be removed to find this legend.
If it does not appear, the sensor may be
mounted with either side toward the muzzle.
2.
Loosen slotted clamp, but do not remove
clamp.
3.
Select the middle thickness (.014) spacer
from the set of nine (065A19) supplied and
place it around sensor barrel.
4.
Begin threading the sensor clamp nut into
the threaded mounting port, sliding slotted
clamp fore and aft as needed to allow guide
pin to fully enter hole.
Continue to turn clamp nut into hole by hand
or using 5/16 open end wrench.
Do not tighten when sensor bottoms.
5.
Now tighten the screw closing slotted clamp.
6.
Using open end wrench, tighten sensor
clamp nut.
NOTE: It is not necessary to put large amounts of
torque on this nut since a pressure seal is not
necessary. Approximately 5 to 10 ft. lbs. is
sufficient.
7.
Now inspect flushness of diaphragm with
inside surface of chamber. This can be
accomplished visually in most cases.
If the diaphragm extends too deeply into the
chamber, select a thicker spacer and repeat
mounting procedure.
If the diaphragm is too deeply recessed,
select a thinner spacer and remount.
Once the proper thickness is found for
perfect flushness, the sensor may be
removed and reinstalled using this same
spacer and the proper depth will be achieved
each time.
NOTE: For best accuracy of results, use
same charge amplifier for calibration and for
actual
operation.
Use
long
TC
for
calibration, medium or short TC for best
drift free operation.
4.0
POLARITY
Polarity of the Model 117B is negative i.e., the
charge output is negative for increasing pressure
input, making it compatible with inverting type
charge amplifiers.
5.0
CALIBRATION
Calibration of the Models 117B is facilitated by a
calibration adaptor which exactly matches the
chamber dimensions of the cartridge under test. An
actual cartridge case is hydraulically pressurized with
reference pressure to obtain a point-by-point sensor
calibration.
These calibration adaptors can be fabricated by the
user or can be purchased from PCB as our Model
090B calibration adaptor. Simply specify caliber and
longitudinal location of sensor.
For most rimfire applications, the sensor is located
.25 inches forward of the boltface.
For center fire cartridges a location .175 inches back
from the cartridge shoulder is preferred. Consult PCB
for recommendations on sensor locations if questions
arise.
Since most cartridge cases are tapered and diameter is
dependent upon longitudinal location, this location
may not be changed after the sensor is fabricated
since it is essential for proper operation that the
sensor curvature exactly match chamber curvature.