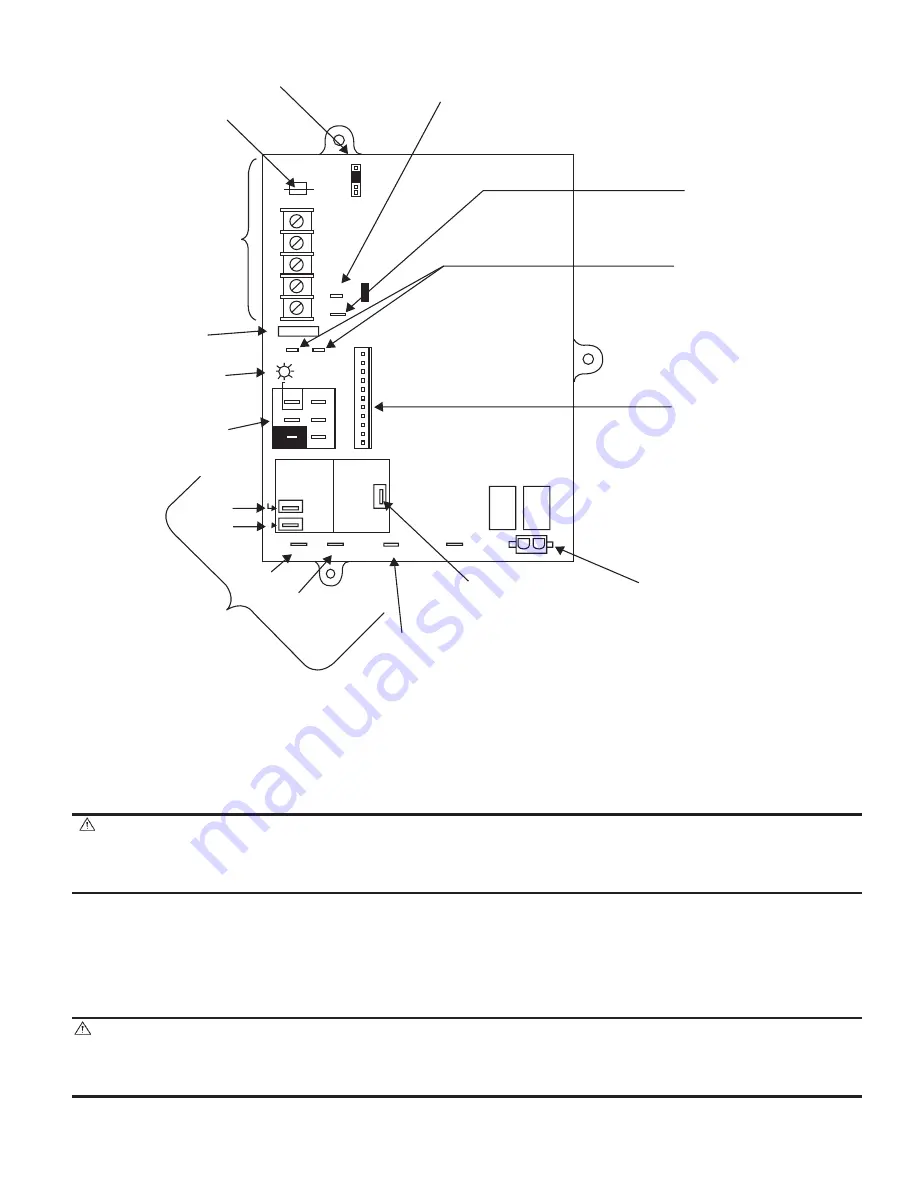
In non-direct vent (1-pipe) system, vent pipe termination must be installed with adequate clearances to building openings and equipment to comply
with national and local codes. See Table 9 for required clearances.
WARNING: CARBON MONOXIDE POISONING HAZARD
Failure to follow this warning could result in property damage, personal injury, or death.
All combustion-air and vent pipes must be airtight and watertight. Pipes must also terminate exactly as shown in Fig. 40 for direct vnet
(2-pipe) system and Fig. 41 for non-direct vent (1-pipe) system.
An abandoned masonry chimney may be used as a raceway for properly insulated and supported combustion-air (when applicable) and vent pipes.
Each furnace must have its own set of combustion-air and vent pipes and be terminated individually, as shown in Fig. 40 for Direct Vent (2-Pipe)
system and Fig. 41 for Non-Direct Vent (1-Pipe) system.
Other gas appliances with their own venting system may also use the abandoned chimney as a raceway providing it is permitted by local code,
the current edition of the National Fuel Gas Code and the vent or liner manufacturer’s installation instructions. Care must be taken to prevent the
exhaust gases from one appliance from contaminating the combustion air of other gas appliances.
CAUTION: UNIT MAY NOT OPERATE
Failure to follow this caution may result in intermittent unit operation.
When vent pipe is exposed to temperatures below freezing, such as when it passes through an unheated space or when a chimney
is used as a raceway, pipe must be insulated as shown in Table 10 with Armaflex-type insulation.
Furnace combustion air and vent pipe connections are sized for 2-in. pipe. Any pipe size change should be made outside furnace casing in vertical
pipe. The transition has to be made as close to the furnce as reasonably possible.
Fig. 35—Control Center
A02100
BL
W
NUETRAL
ST
A
TUS CODE LED
SEC-2 SEC-1
EAC-2 L2
FUSE 3-AMP
0.5 AMP@24VAC
HUM
TEST/TWIN
G Com
W
Y R
24V
120 180
90 150
BLOWER OFF-DELAY
PL
T 1
COOL HEA
T
SPARE-1 SPARE-2
EAC-1
1-AMP@
115VAC
PR-1
L1
PL2 1
24-V THERMOSTAT
TERMINALS
3-AMP FUSE
LED OPERATION &
DIAGNOSTIC LIGHT
115-VAC(L2)NEUTRAL
CONNECTIONS
COOL
HEAT
SPARE-1
SPARE-2
BLOWER SPEED
SELECTION TERMINALS
EAC-1 TERMINAL
(115-VAC 1.0 AMP MAX.)
115 VAC (L1) LINE
VOLTAGE CONNECTION
PL2-HOT SURFACE
IGNITER & INDUCER
MOTOR CONNECTOR
PL1-LOW VOLTAGE MAIN
HARNESS CONNECTOR
TRANSFORMER 24-VAC
CONNECTIONS
HUMIDIFIER TERMINAL
(24-VAC 0.5 AMP MAX.)
TWINNING AND/OR
COMPONENT TEST
TERMINAL
BLOWER OFF-DELAY
J2
J2 JUMPER
PL
T
—35—
→
→
→