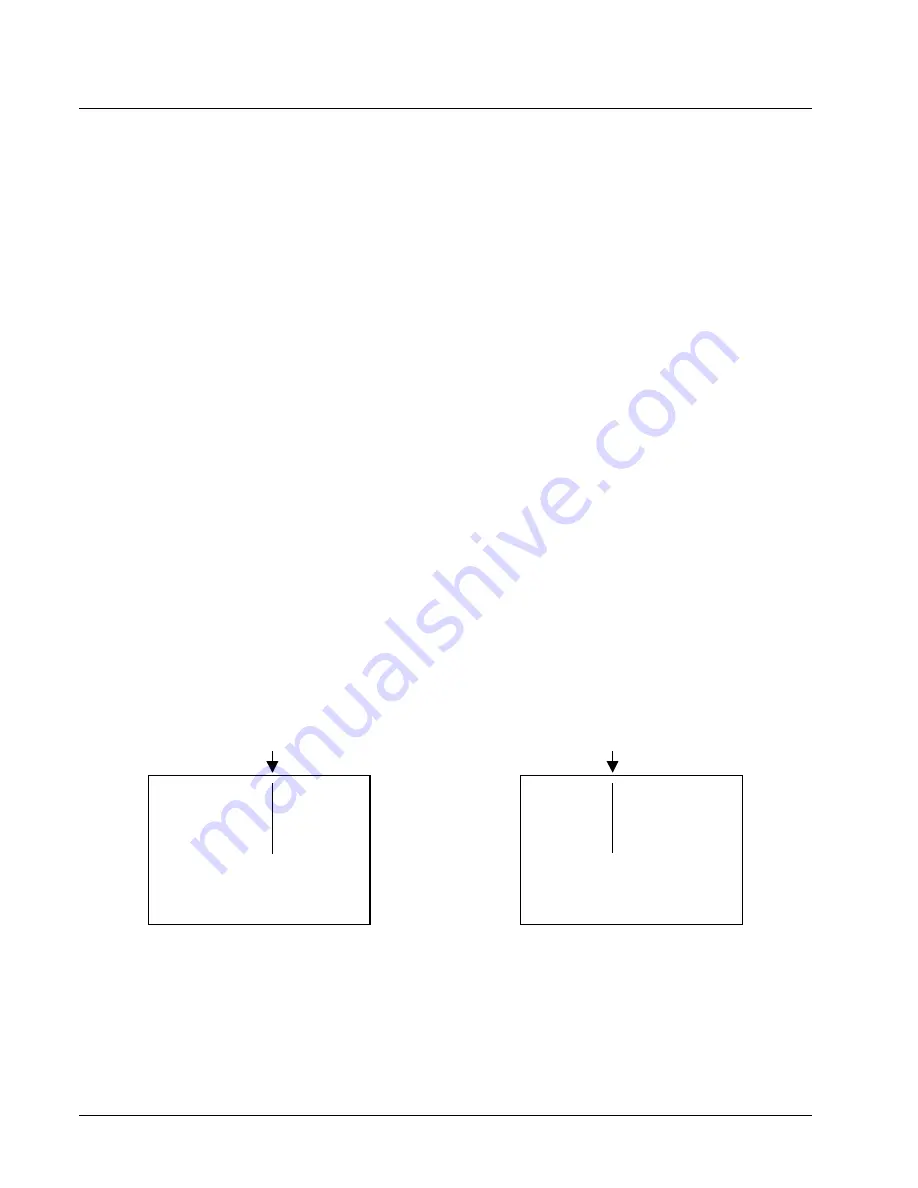
34
•
Printer Operation / Adjustments
Users Manual Model 545™
Printer Setup
From time to time it may be necessary or desirable to reset the printer to a known
state of print / cut. The following procedure can be used to make the necessary
changes. Only adjust the adjustments that are needed in the order that follows;
1) Clean the machine as needed.
2) Check and adjust the unwind and web guides as needed for the fabric width that is
loaded on the machine.
3) Using a 5/64” hex key adjust station 1’s head swing arm stop screw to produce
print on the back of the label that has neither a gap or overlap in the center of the
print image. Rotating the screw counter clockwise will decrease the overlap or
increase the gap. Rotating it clockwise will decrease the gap or increase the
overlap. Once adjusted properly the image on the back of the label should appear
square with no gap or overlap in the center.
4) Adjust station 2’s head swing arm stop screw the same as station 1 to produce
print on the front of the label that has neither a gap or overlap in the center of the
print image.
5) Using the print line label format adjust the mount angle of the knife as needed to
produce a square cut. Loosen the two mount screws securing the knife module
and rotate the entire module then retighten the mount screws.
6) On the front panel adjust the PRINT POSITION STATION 1 to cause the inboard
half of the feed print line on the back of the label to be at 1.0”.
NOTE
: PRINT POSTION STATION 1 adjustment is opposite from all the other
adjustment. Using the module view a more negative number moves the
print to the right; a more positive number moves the print to the left.
-20
+20
7) On the front panel adjust the PRINT POSITION STATION 2 to cause the inboard
half of the feed print line on the front of the label to be at 1.0”.
Содержание 545
Страница 2: ...This page intentionally blank ...
Страница 78: ...76 Electrical Drawings Users Manual Model 545 Electrical Drawings Printer Wiring ...
Страница 90: ......
Страница 91: ...Users Manual Model 545 Assembly Drawings 89 Assembly Drawings ...
Страница 94: ...92 Assembly Drawings Users Manual Model 545 Frame Assembly Drawing ...
Страница 96: ...94 Assembly Drawings Users Manual Model 545 Sub Frame Assembly Drawing ...
Страница 98: ...96 Assembly Drawings Users Manual Model 545 Power Unwind Assembly Drawing ...
Страница 100: ...98 Assembly Drawings Users Manual Model 545 Unwind Support Assembly Drawing ...
Страница 102: ...100 Assembly Drawings Users Manual Model 545 Unwind Nip Roller Assembly Drawing 9 9 10 2 1 11 4 5 3 6 7 8 8 ...
Страница 104: ...102 Assembly Drawings Users Manual Model 545 Unwind Snubber Assembly Drawing ...
Страница 106: ...104 Assembly Drawings Users Manual Model 545 Print Module Assembly Drawing ...
Страница 108: ...106 Assembly Drawings Users Manual Model 545 Cartridge Support Deck Assembly Drawing ...
Страница 110: ...108 Assembly Drawings Users Manual Model 545 Feed Assembly Drawing ...
Страница 114: ...112 Assembly Drawings Users Manual Model 545 Knife Assembly Drawing ...
Страница 116: ...114 Assembly Drawings Users Manual Model 545 Stacker Assembly Drawing Part 1 ...
Страница 118: ...116 Assembly Drawings Users Manual Model 545 Stacker Assembly Drawing Part 2 ...
Страница 120: ...118 Assembly Drawings Users Manual Model 545 Rewind Assembly Drawing ...