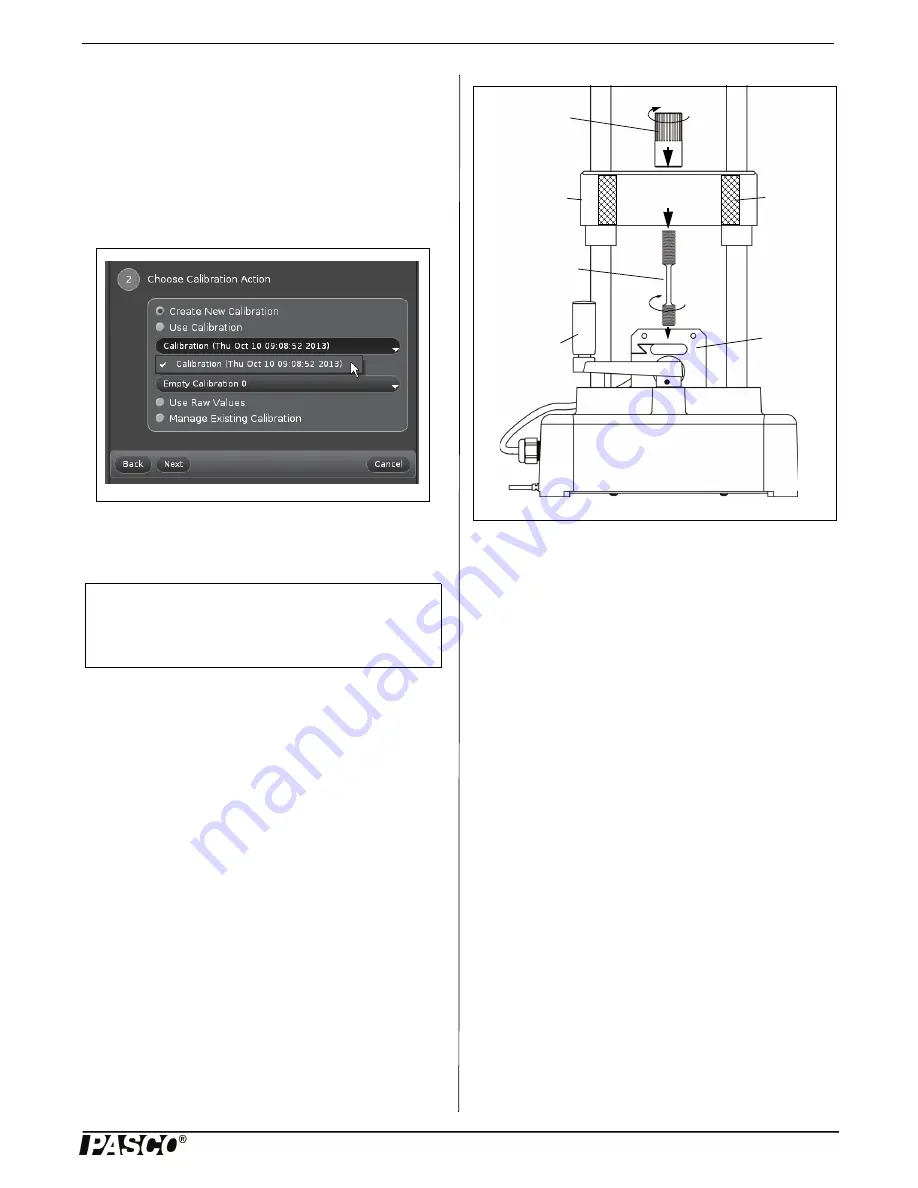
Model No.ME-8236
Operation
7
012-13762C
Finishing Step
•
Click “Finish” to store the calibration as part of the Cap-
stone file.
NOTE: The “Calibration” window goes back to Step One.
When you click “Next”, the “Choose Calibration Action”
window (Step Two) will show a menu of the stored calibra-
tion(s). Click “Use Calibration” to select a specific stored
calibration.
•
Click the “Calibration” icon in the Tools palette to close
the “Calibration” window. Save the Capstone file for
future use.
Mount a Tensile Sample
Select a tensile sample to mount onto the Materials Testing
Machine. Put the end of the sample with the short threaded
section into the threaded hole in the top of the load cell.
Screw in the sample until the top edge of the short threaded
section is flush with the top of the load cell.
Lower the load bar so that the longer threaded section of the
sample goes up through the hole in the center of the load bar.
Adjust the load bar until the bottom edge of the longer
threaded section is flush with the bottom of the load bar.
While holding the tensile sample so it does not turn, screw
the sample nut onto the longer threaded section until the
sample is held tightly in place.
Attach the Safety Shields
Attach the Velcro® hook material on the two safety shields
to the Velcro® loop material on the front and back of the
Load Bar. Adjust the position of the shields so that they will
block any fragments that may come from the sample.
Record Data
Prepare PASCO Capstone software to record data. (If there is
a stored calibration file that is to be used, select it in the
“Calibration” window.)
Start data recording in the software. Turn the crank in a
clockwise direction to apply a tension force to the tensile
sample. Observe the graph display of force and position.
(Note that the default for the Materials Testing Machine in
the software shows force and position as ‘negative’ when a
tension force is applied.)
When the sample breaks, or is stretched the maximum
amount, stop data recording.
Materials Bending Accessory (ME-8237)
The Materials Bending Accessory includes a plunger, a
adjustable support anvils, and a small hex key (allen
wrench). The plunger is mounted on the bottom of the load
bar using the sample nut. The base for the adjustable anvils
is screwed onto the top of the load cell.
The spacing between the two triangular support anvils can be
adjusted. Use the hex key to loosen the screws holding the
anvils and slide them closer together or farther apart. Tighten
the screws securely.
Figure: Use Calibration
NOTE
: Information about the calibration proce-
dure is included in the Appendix of this manual
and in the Experiment Guide that can be down-
loaded from the PASCO web page.
Load Bar
Sample
Nut
Tensile
Sample
Crank
Handle
Load
Cell
Figure: Mount Tensile Sample
Loop
Material
for Safety
Shield
Load Bar
(crosshead)