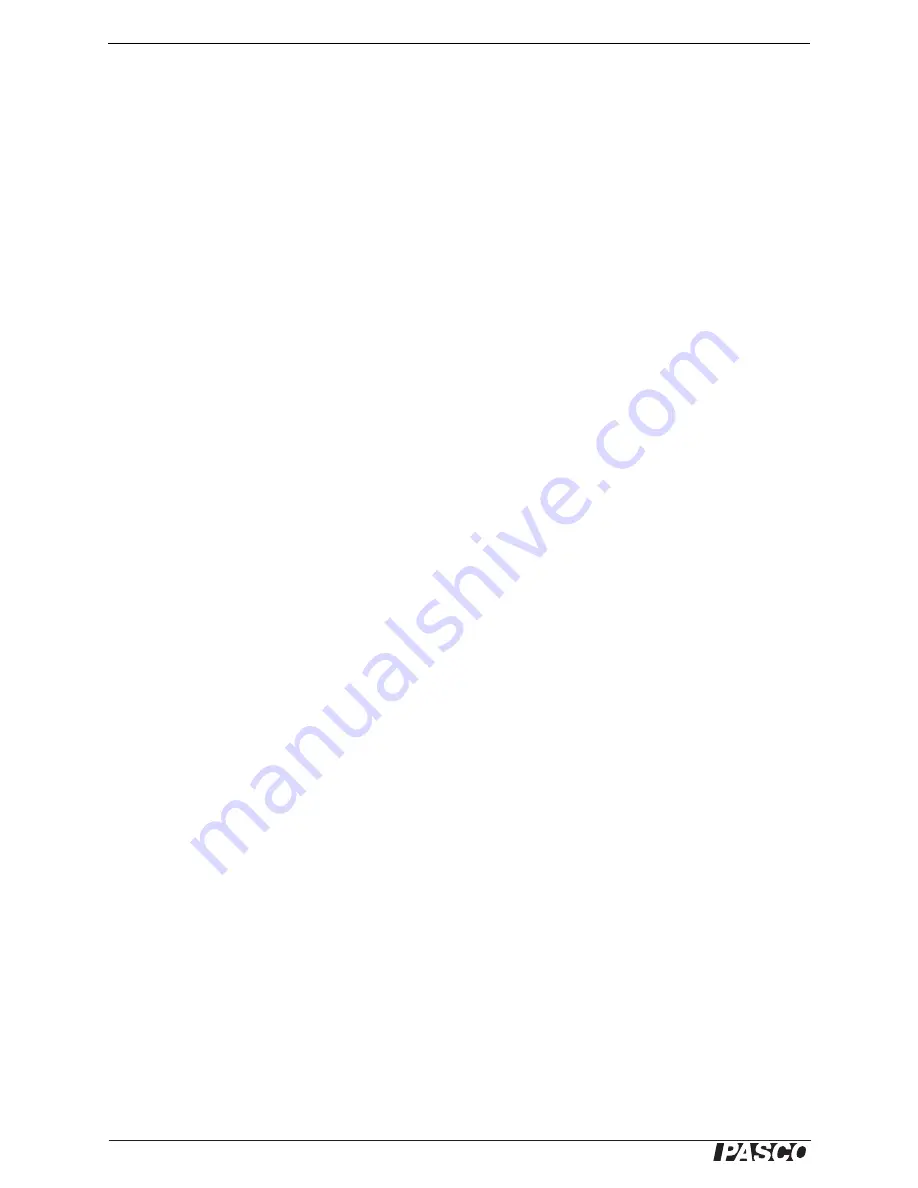
®
S tr e s s / St r a i n A p p a r a t u s
A p p a r a t u s C a l i b r a t i o n
4
4.
Plug the sensors into the interface
.
•
ScienceWorkshop interface:
Connect the Force Sensor to Channel A.
Connect the yellow plug of the RMS to Channel 1 and the black plug to
Channel 2.
•
PASPORT interface:
Connect the Force and Motion sensors to a multi-port
interface or two single-port interfaces.
5.
Prepare DataStudio
. Start DataStudio and open the activity file
Stress Strain SW.ds
(for
ScienceWorkshop
) or
Stress Strain PS.ds
(for PASPORT)
located on the included CD-ROM.
Apparatus Calibration
During the experiment, as you turn the crank, force will be applied to the test coupon
causing it to stretch. However, this force will also cause the apparatus platform and
the Force Sensor to bend. The displacement registered by the RMS will be the combi-
nation of the coupon stretching and the rest of the apparatus bending.
Regardless of how much the coupon stretches, the deformation of the rest of the appa-
ratus is constant for a given force. You can measure this deformation directly by using
the calibration bar (which does not stretch significantly) in place of a coupon. In the
resulting Displacement versus Force graph, the displacement is due only to bending
of the apparatus. Later, you will subtract this calibration plot from a similar plot made
with a coupon, in which the displacement results from both bending of the apparatus
and stretching of the coupon. The difference will be a plot in which the displacement
is due only to stretching of the coupon.
Follow these steps to acquire calibration data:
1.
Install the Calibration Bar
.
a.
Remove the nuts and clips from the apparatus platform (Figure 3).
b.
Turn the crank to adjust the position of the bolts and slip the bolts through
the holes in the calibration bar.
Do not replace the nuts when using the
calibration bar
.
2.
Place the lever arm in the starting position
. Turn the crank counter-clockwise
and pull the lever arm away from the Force Sensor (Figure 4).
3.
Plot Position versus Force
.
a.
Press the Tare or Zero button on the Force Sensor.
b.
Click the Start button.
c.
Turn the crank clockwise. Starting just before the lever arm comes into
contact with the Force Sensor, turn the crank very slowly. DataStudio will
start recording when the force applied to the coupon reaches 2.5 N, or 1% of
maximum (as shown in the “% Max Force” digits display).
d.
Continue to turn the crank until the force reaches 100% of maximum. At this
point, DataStudio will stop recording automatically.
e.
Change the name of the data run containing the calibration data to “Cal”.*
* To rename a data run,
click the run name (e.g.
“Run #1”) where it
appears in the Data List.
Wait about 1 second then
click it again. Enter the
new name. A dialog box
will appear. Select Yes. (If
a window titled “Data
Properties” appears, you
didn't wait long enough
after the first click; close
that window and try
again.)