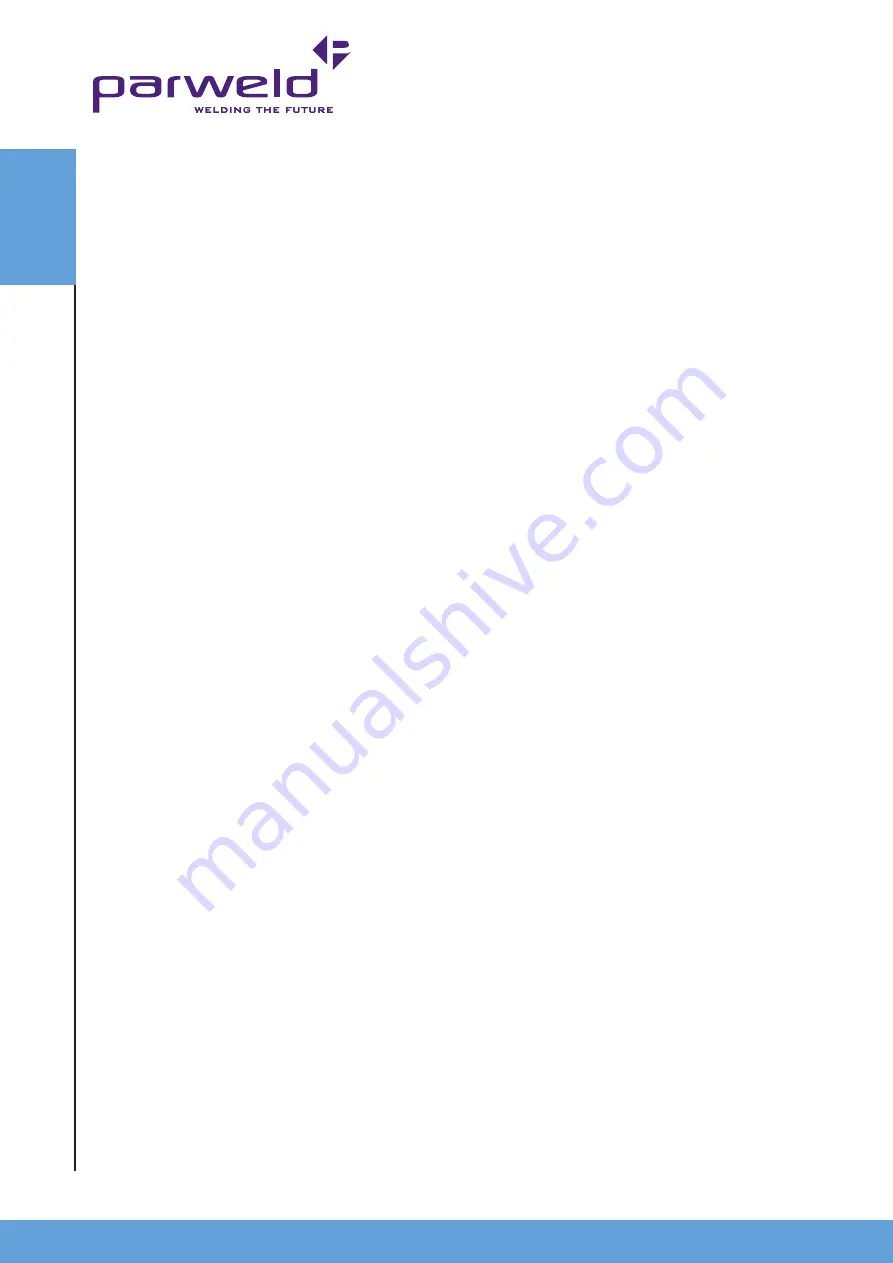
www.parweld.co.uk
4
1.0 Safety Precautions
ELECTRIC SHOCK can kill.
Touching live electrical parts can cause fatal shocks or severe burns.
The electrode and work circuit is electrically live whenever the output
is on. The input power circuit and machine internal circuits are also
live when power is on.
Do not touch live electrical parts.
Wear dry, sound insulating gloves and body protection.
Insulate yourself from work and ground using dry insulating mats
or covers big enough to prevent any physical contact with the work
ground.
Additional safety precautions are required when any of the following
electrically hazardous conditions are present: in damp locations
or while wearing wet clothing; on metal structures such as floors,
gratings, or scaffolds; when in cramped positions such as sitting,
kneeling, or lying; or when there is a high risk of unavoidable or
accidental contact with the work piece or ground.
Disconnect input power before installing or servicing this equipment.
Lockout/tagout input power according to Safety Standards.
Properly install and ground this equipment according to national and
local standards.
Always verify the supply ground - check and ensure that input power
cable ground wire is properly connected to ground terminal in the
receptacle outlet.
When making input connections, attach proper grounding conductor
first - double-check connections.
Frequently inspect input power cable for damage or bare wiring -
replace cable immediately if damaged - bare wiring can kill.
Turn off all equipment when not in use.
Do not use worn, damaged, under sized, or poorly spliced cables.
Do not drape cables over your body.
If earth grounding of the work piece is required, ground it directly
with a separate cable.
Do not touch electrode if you are in contact with the work, ground, or
another electrode from a different machine.
Use only well-maintained equipment. Repair or replace damaged
parts at once. Maintain unit according to manual.
Wear a safety harness if working above floor level.
Keep all panels and covers securely in place.
Clamp work cable with good metal-to-metal contact to work piece or
worktable as near the weld as practical.
Insulate work clamp when not connected to work piece to prevent
contact with any metal object.
Welding produces fumes and gases. Breathing these fumes and
gases can be hazardous to your health.
FUMES AND GASES can be hazardous.
Keep your head out of the fumes. Do not breathe the fumes.
If inside, ventilate the area and/or use local forced ventilation at the
arc to remove welding fumes and gases.
If ventilation is poor, wear an approved respirator.
Read and understand the Material Safety Data Sheets (MSDS’s) and
the manufacturer’s instructions for metals, consumable, coatings,
cleaners, and de-greasers.
Work in a confined space only if it is well ventilated, or while wearing
an air-supplied respirator. Always have a trained watch person
nearby. Welding fumes and gases can displace air and lower the
oxygen level causing injury or death. Be sure the breathing air is
safe.
Do not weld in locations near de-greasing, cleaning, or spraying
operations. The heat and rays of the arc can react with vapours to
form highly toxic and irritating gases.
Do not weld on coated metals, such as galvanized, lead, or cadmium
plated steel, unless the coating is removed from the weld area, the
area is well ventilated, and while wearing an air-supplied respirator.
The coatings and any metals containing these elements can give off
toxic fumes if welded.
ARC RAYS can burn eyes and skin.
Arc rays from the welding process produce intense, visible and
invisible (ultraviolet and infrared) rays that can burn eyes and skin.
Sparks fly off from the weld.
Wear an approved welding helmet fitted with a proper shade of filter
lense to protect your face and eyes when welding or watching
Wear approved safety glasses with side shields under your helmet.
Use protective screens or barriers to protect others from flash, glare
and sparks; warn others not to watch the arc.
Wear protective clothing made from durable, flame resistant material
(leather, heavy cotton, or wool) and foot protection. Welding on
closed containers, such as tanks, drums, or pipes, can cause them
to blow up. Sparks can fly off from the welding arc. The flying sparks,
hot work piece, and hot equipment can cause fires and burns.
Accidental contact of electrode to metal objects can cause sparks,
explosion, overheating, or fire. Check and be sure the area is safe
before doing any welding.
WELDING can cause fire or explosion.
Remove all flammables within 10m of the welding arc. If this is not
possible, tightly cover them with approved covers.
Do not weld where flying sparks can strike flammable material.
Protect yourself and others from flying sparks and hot metal.
Be alert that welding sparks and hot materials from welding can
easily go through small cracks and openings to adjacent areas.
SAFETY
Содержание XTT 250 DC P
Страница 1: ...OPERATORMANUAL ISSUE 4 XTT 250 DC P ...