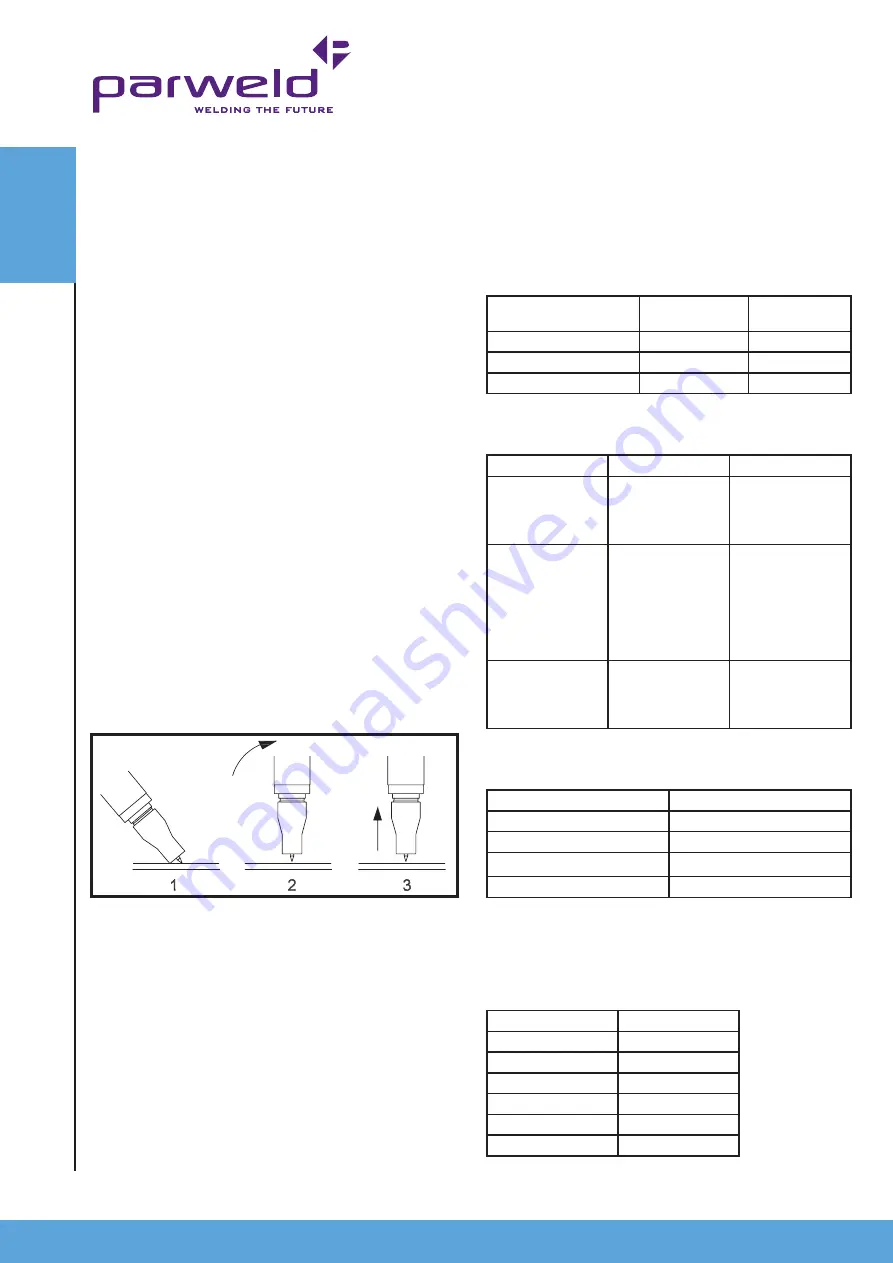
www.parweld.com
8
Torch starting in Lift TIG mode
Ensure the gas supply is switched on to the machine. Briefly contact
the tip of the tungsten electrode down onto the work piece with the
torch at around 70
0
from vertical. Depress the trigger to start the gas
flow and switch on the power, lift the torch up from the work piece
to draw out an arc. To prevent melting of the end of the tungsten the
machine will increase the output current when it detects the rise in
arc voltage as the tungsten is lifted from the work piece. At the end
of the weld release the torch trigger and the power will slope down
and switch off.
Torch starting in HF mode
Ensure the gas supply is switched on to the machine. Hold the torch
with the tip of the tungsten approx 2-3 mm from the job. Depress the
trigger to start the gas flow and switch on the power. At the end of
the weld release the torch trigger and the power will slope down and
switch off. (Note in 4T position you must press and release to start
Types of electrodes
Arc welding electrodes are classified into a number of groups
depending on their applications. There are a great number of
electrodes used for specialized industrial purposes which are not of
particular interest for everyday general work. These include some
low hydrogen types for high tensile steel, cellulose types for welding
large diameter pipes, etc. The range of electrodes dealt with in this
publication will cover the vast majority of applications likely to be
encountered; are all easy to use and all will work on even the most
basic of welding machines.
Metals being joined & electrode comments
Mild steel
6013 ideal electrodes for all general purpose work. Features include
outstanding operator appeal, easy arc starting and low spatter.
Mild steel
7014 all positional electrode for use on mild and galvanized steel
furniture, plates, fences, gates, pipes and tanks etc. Especially
suitable for vertical down welding.
Cast iron
99% nickel suitable for joining all cast irons except white cast iron
Stainless steel
318l-16 high corrosion resistance. Ideal for dairy work, etc. On
stainless steels.
6.2
Basic TIG Welding guide
Tig welding cable connection
Connect the TIG torch to the - terminal and the work lead to the +
terminal for direct current straight polarity. Direct current straight
polarity is the most widely used polarity for DC TIG welding. It allows
limited wear of the electrode since 70% of the heat is concentrated
at the work piece.
the process and press and release again to stop the process. When
stopping in 4T mode holding down the trigger button will activate the
slope down, releasing the button will switch off the arc) when starting
the arc the HF will only fire for a few seconds so if the arc is not
started withing this tine the starting process should be repeated by
releasing the trigger and depressing again.
TIG welding guide ranges
Electrode diameter
AC current
(amps)
DC current
(amps)
0.040” (1.0mm)
15-30
20-60
1/16” (1.6mm)
60-120
75-150
3/32” (2.4mm)
100-180
150-250
Tungsten electrode types
Type
Application
Colour
Thoriated 2%
DC welding of mild
steel,
Stainless steel and
Copper
Red
Ceriated 2%
DC welding of mild
steel, Stainless
steel, Copper
AC welding
of aluminium,
magnesium and
their alloys
Grey
Zirconiated
AC welding
of aluminium,
magnesium and
their alloys
White
Guide for selecting filler wire diameter
Filler wire diameter
Current range
1/16” (1.6 mm)
20 - 90
3/32” (2.4 mm)
65 - 115
1/8” (3.2 mm)
100 - 165
3/16” (4.8 mm)
200-350
The filler wire diameter specified is a guide only, other diameter
wires may be used according to the welding application.
Shielding gas selection
Alloy
Shielding gas
Aluminium & alloys
Pure Argon
Carbon steel
Pure Argon
Stainless steel
Pure Argon
Nickel alloy
Pure Argon
Copper
Pure Argon
Titanium
Pure Argon
O
pera
tIO
n
Содержание XTT 207 DV P
Страница 1: ...OperatorManual ISSUE 1 XTT 207 DV P...