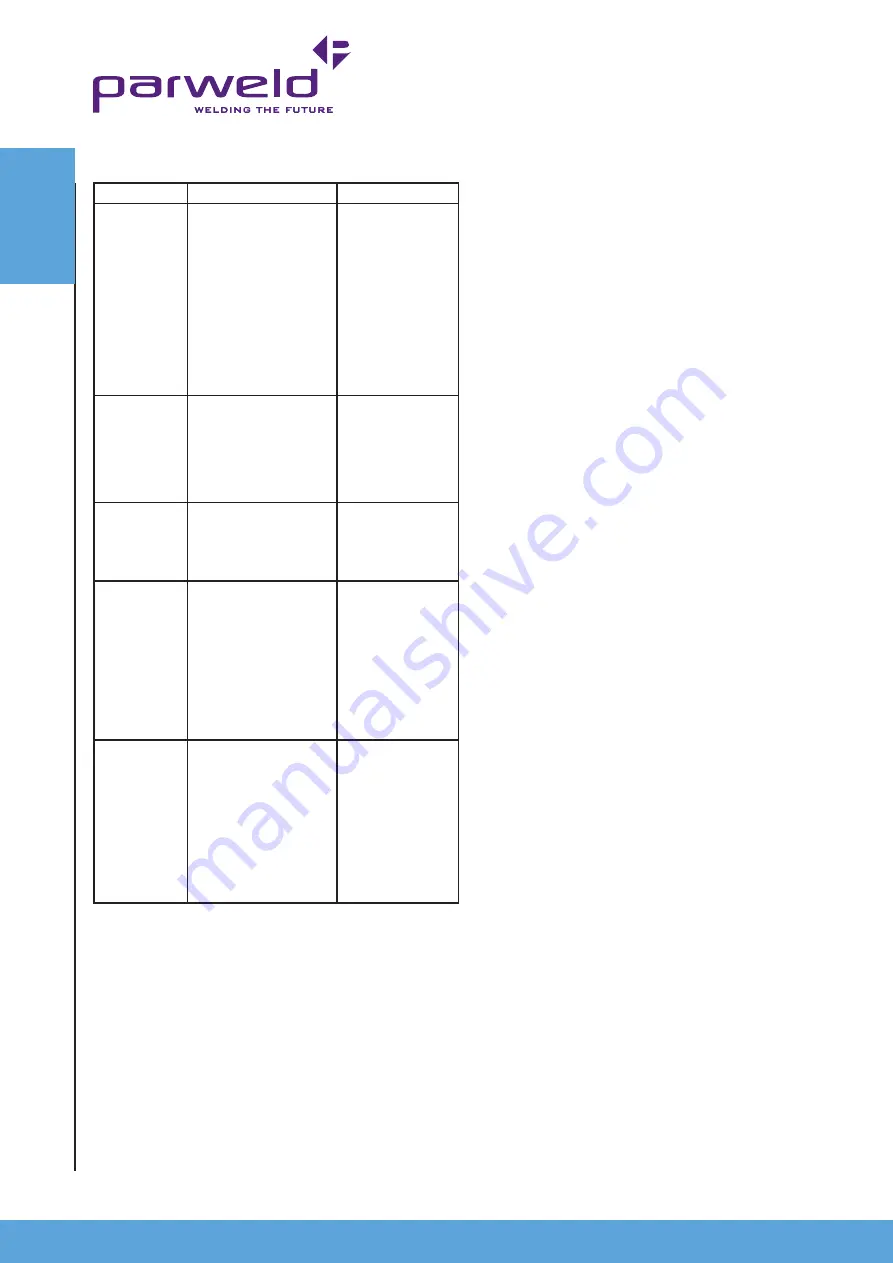
www.parweld.com
12
Faul
t
FI
n
DI
n
G
Power source problems
Description
Possible cause
Remedy
The welding
arc cannot be
established
(a) The primary supply
voltage has not been
switched on
(b) The welding power
source switch is switched
off
(c) The power source is
latched on
(d) Loose connections
internally
(a) Switch on the
primary supply
voltage
(b) Switch on the
welding power
source.
(c) Switch the power
source on and off
(d) Have a
qualified service
engineer repair the
connection
Maximum
output welding
current cannot
be achieved
with nominal
mains supply
voltage
Defective control circuit
Have a qualified
service engineer
inspect then repair
the welder
Welding
current
reduces when
welding
Poor work lead
connection to the work
piece
Ensure that the
work lead has a
reliable electrical
connection to the
work piece
A total loss of
power, pilot
lamp is off,
no output,
the fan is not
operating
(a) Failure of input
voltage
(b) Possible over voltage
(c) Internal fault with the
machine
(a) Re-establish
mains supply
(b) Check voltage
and if necessary
move machine to
alternative supply
(c) Have a qualified
service engineer
inspect then repair
the welder
Fault lamp is
on, no power
output
(a) Machine overheated
(b) Over current state
(c) Internal fault with
machine
(a) Allow to cool
with fan running
(b) Switch off
mains power to the
machine and re start
(c) Have a qualified
service engineer
inspect
then repair the
welder
ROUTINE MAINTENANCE
The only routine maintenance required for the power supply is a
thorough cleaning and inspection, with the frequency depending on
the usage and the operating environment.
Warning
Disconnect primary power at the source before removing the cover.
Wait at least two minutes before opening the cover to allow the
primary capacitors to discharge.
To clean the unit, remove the screws securing the outer cover,
lift off the outer cover and use a vacuum cleaner to remove any
accumulated dirt and dust. The unit should also be wiped clean,
if necessary; with solvents that are recommended for cleaning
electrical apparatus.
Содержание XTT 207 DV P
Страница 1: ...OperatorManual ISSUE 1 XTT 207 DV P...