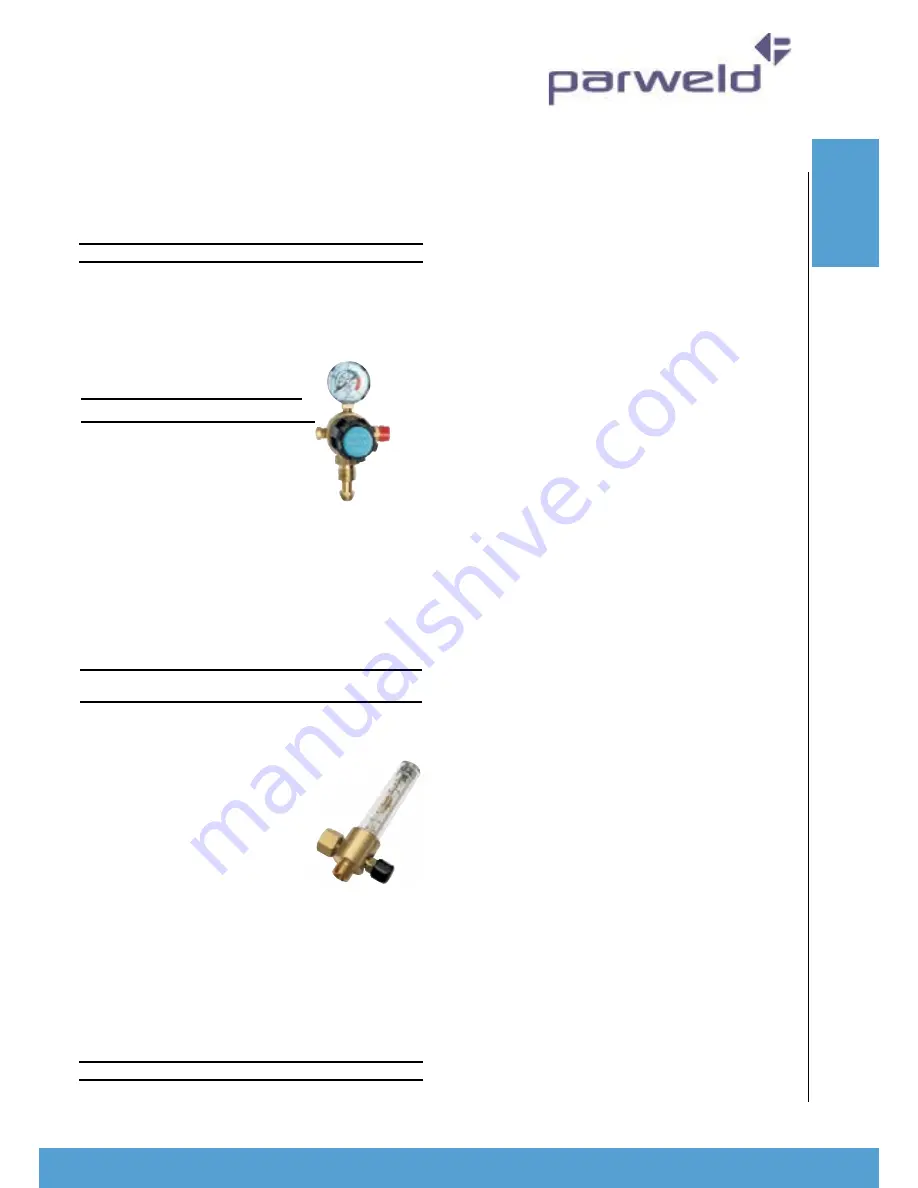
www.parweld.com
www.parweld.com
8.0 Accessories
8.1 Torch spares
Stock Code
Description
CKE403
Electrode Holder with 3m Lead
CKC403
Earth Lead 3m with Clamp
ER26-123KBD18
ERGO Tig Torch with remote
control
WP26AK
Tig Spares
Kit in Plastic Case
8.2 Gas equipment
Everyday Gas Regulators – 300 BAR
Single Stage
Features
Flow rate up to 96m
3
/h (3389 ft
3
/h)
• Full 300 bar capability
• Outlet pressure indicated on the bonnet
• Bottom entry design suited for top outlet
cylinder valves
Fittings
• Fitted with standard 3/8” BSP outlet
• Fitted with
5
/8” BSP inlet connections
Stock Code Description
Maximum Outlet
Pressure
E700140 Argon Preset Regulator
3.0 Bar
E700141 Argon Indicator Regulator 3.0 Bar
E700113 1 Gauge Argon
30 lpm flow
E700123 2
Gauge Argon
30 lpm
flow
Flow Meters
Features
• Designed from brass bar whilst the
tube and cover are moulded from
high quality polycarbonate to ensure high impact
resistance and clarity
• Calibrated to operate at an inlet pressure
of 30PSI
• Sensitive needle valve provides easy adjustment and
the downward facing outlet connection eliminates
hose kinking.
Fittings
• Fitted with standard 3/89 BSP inlet and outlet
connections
Stock Code
Description
706100
Flow Meter Mixed Gas 15 lpm
a
CC
eSSO
rY
9.0 Statement of Warranty
Limited Warranty:
Parweld Ltd, hereafter, “Parweld” warrants its
customers that its products will be free of defects
in workmanship or material. Should any failure
to conform to this warranty appear within the
time period applicable to the Parweld products
as stated below, Parweld shall, upon notification
thereof and substantiation that the product has
been stored, installed, operated, and maintained in
accordance with Parweld’s specifications, instructions,
recommendations and recognized standard industry
practice, and not subject to misuse, repair, neglect,
alteration, or accident, correct such defects by suitable
repair or replacement, at Parweld’s sole option, of any
components or parts of the product determined by
Parweld to be defective.
Parweld makes no other warranty, express or
implied. This warranty is exclusive and in lieu of all
others, including, but not limited to any warranty of
merchantability or fitness for any particular purpose.
Limitation of Liability:
Parweld shall not under any circumstances be liable for
special, indirect or consequential damages, such as, but
not limited to, lost profits and business interruption.
The remedies of the purchaser set forth herein are
exclusive and the liability of Parweld with respect to
any contract, or anything done in connection therewith
such as the performance or breach thereof, or from the
manufacture, sale, delivery, resale, or use of any goods
covered by or furnished by Parweld whether arising
out of contract, negligence, strict tort, or under any
warranty, or otherwise, shall not, except as expressly
provided herein, exceed the price of the goods upon
which such liability is based. No employee, agent, or
representative of Parweld is authorized to change this
warranty in any way or grant any other warranty.
Purchaser’s rights under this warranty are void if
replacement parts or accessories are used which in
Parweld’s sole judgement may impair the safety or
performance of any Parweld product.
Purchaser’s rights under this warranty are void if the
product is sold to purchaser by non-authorized persons.
The warranty is effective for the time stated below
beginning on the date that the authorized Distributor
delivers the products to the purchaser. Notwithstanding
the foregoing, in no event shall the warranty period
extend more than the time stated plus one year
from the date Parweld delivered the product to the
authorized distributor.
15
Содержание XTI-201
Страница 1: ...INSTRUCTION MANUAL...
Страница 2: ...Operator Manual ISSUE 2 XTI 201 AC DC...