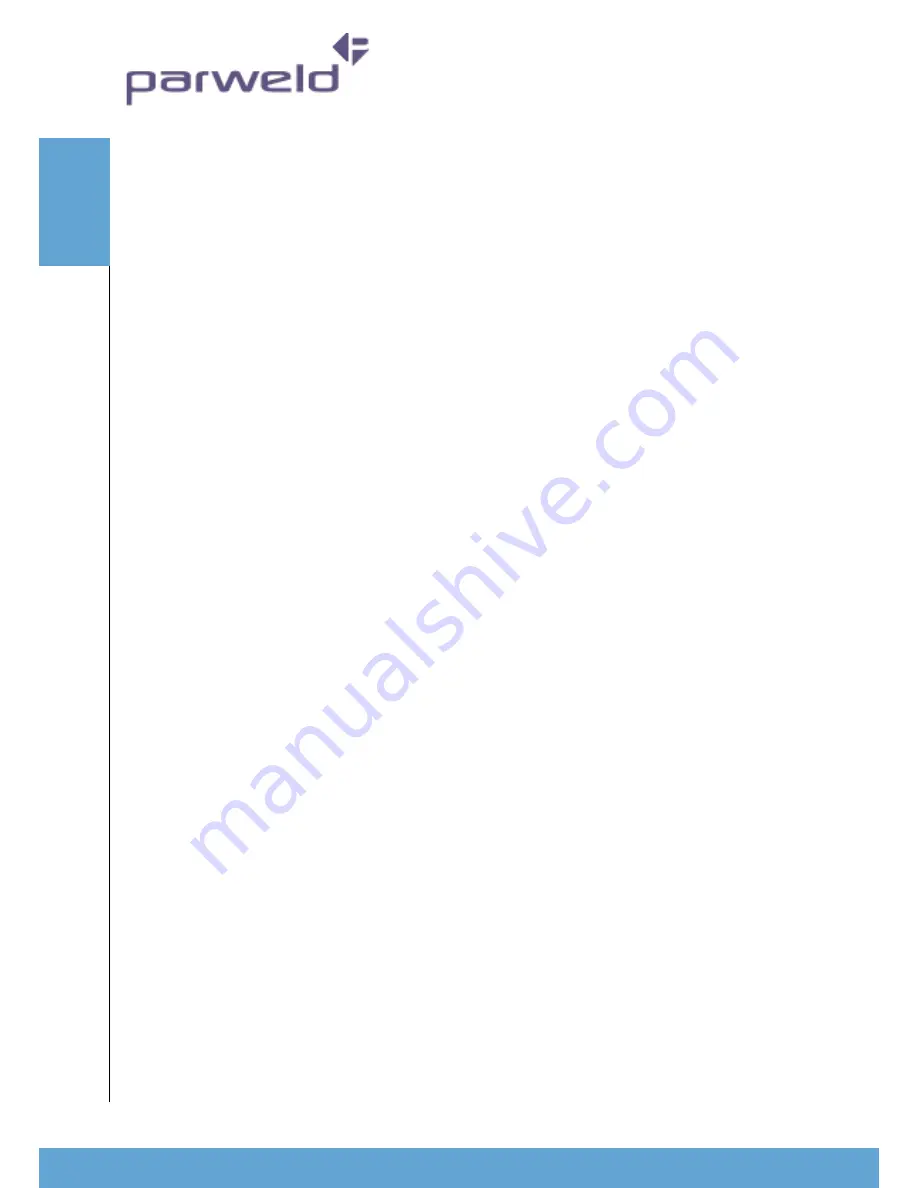
www.parweld.com
8
or aluminium wire, may require less pressure than the factory
setting. The optimum idle roll setting can be determined as
follows:
2. Press end of gun against a solid object that is electrically
isolated from the welder output and press the gun trigger for
several seconds.
3. If the wire “bird nests”, jams or breaks at the drive roll, the idle
roll pressure is too great. Back the adjustment knob out 1/2
turn, run new wire. If the only result was drive roll slippage,
loosen the Hand nut on the central connector and pull the gun
forward about 6” (15cm) away from the power source. There
should be a slight waviness in the exposed wire. If there is no
waviness, the pressure is too low. Tighten the adjustment knob
1/4 turn, reinstall the gun cable and repeat the above steps.
6.1.1 Feeding wire electrode
1. When triggering, the electrode and drive mechanism are
electrically “LIVE” relative to work and ground and remain
“LIVE” several seconds after the gun trigger is release
d.
WarnInG
When using an open arc process, it is necessary to use correct
eye, head, and body protection.
2. Position wire over joint. The end of the wire may be lightly
touching the work.
3. Lower welding helmet, operate gun trigger, and begin welding.
Hold the gun so the contact tip to work distance is about 3/8”
(10 mm).
4. To stop welding, release the gun trigger and then pull the gun
away from the work after the arc goes out.
5. When no more welding is to be done, close valve on gas
cylinder (if used), momentarily operate gun trigger to release
gas pressure and turn off the machine.
6.1.1 Optimising weld parameters
NOTE These settings are guidelines only. Material and wire
type, joint design, fit up, position, shielding gas, etc. affect
settings. Produce test welds to be sure they comply to
specifications.
Material thickness determines weld parameters.
1. Convert Material Thickness to Amperage (A) (0.25mm= 1 Amp)
3.2mm = 125 A
2. Select Wire Size
Amperage Range Wire Size
40 - 145 A
0.8 mm
50 - 180 A
1.0 mm
3. Select Wire Speed (Amperage)
Wire Size
Feed speed
0.8 mm
0.05m/min per Amp
1.0 mm
0.04m/min per Amp
So based on 3.2 mm material thickness amperage should be 125A if
using 1.0mm wire then the wire feed speed should be
damage to the gas nipple O-ring a very light application of
grease to the O Ring is beneficial.
4. Keeping the torch as straight as possible, use the torch trigger
to feed the electrode wire 50mm from the end of the liner
conduit.
5.
Once the electrode wire has stopped, refit the tip adaptor,
diffuser, contact tip and gas nozzle.
6. Trim the electrode wire to within 5mm of the face of the nozzle,
this will facilitate jolt free arc initiation.
7.
Press the gas purge button and check the gas flow is adequate
for your application.
8.
An inexpensive flow meter is available from Parweld reference
806001.
5.4.4 Work return lead connection
Insert the work return lead connector into the Negative dinse
receptacle on the front panel of the machine and twist it clockwise
until tightly secured.
Connect the earth clamp to the work piece as close as possible to
the point to be welded and ensure that a good electrical connection
is created to bare metal.
5.4.4 Shielding gas connection
1. Using the gas hose supplied connect the hose to the gas inlet
connection on the rear of the machine and tighten it with a
spanner.
2. Connect the opposite end of the gas hose to the output
connection of a gas regulator capable of supplying the correct
gas flow for the welding operation.
Note The gas cylinder should be secured to ensure it cannot
fall.
6.0 Operation
WarnInG
When using an open arc process, it is necessary to use correct
eye, head, and body protection.
6.1 MIG Welding
Controls used
2T/4T sets the trigger to momentary or latching for longer
welding runs.
Voltage adjustment knob, allows the adjustment of welding
voltage
Current adjustment knob which controls the wire feed speed
Inductance control which controls the smoothness of the arc
Note: Check that drive rolls, and torch parts are correct for the
wire size and type being used.
1.
The optimum idle roll pressure varies with type of wire, wire
diameter, surface conditions, lubrication, and hardness. As a
general rule, hard wires may require greater pressure, and soft,
Faul
t
FI
n
DI
n
G
Содержание XTI-160 M
Страница 1: ...Operator Manual ISSUE 1 XTI 160 M...