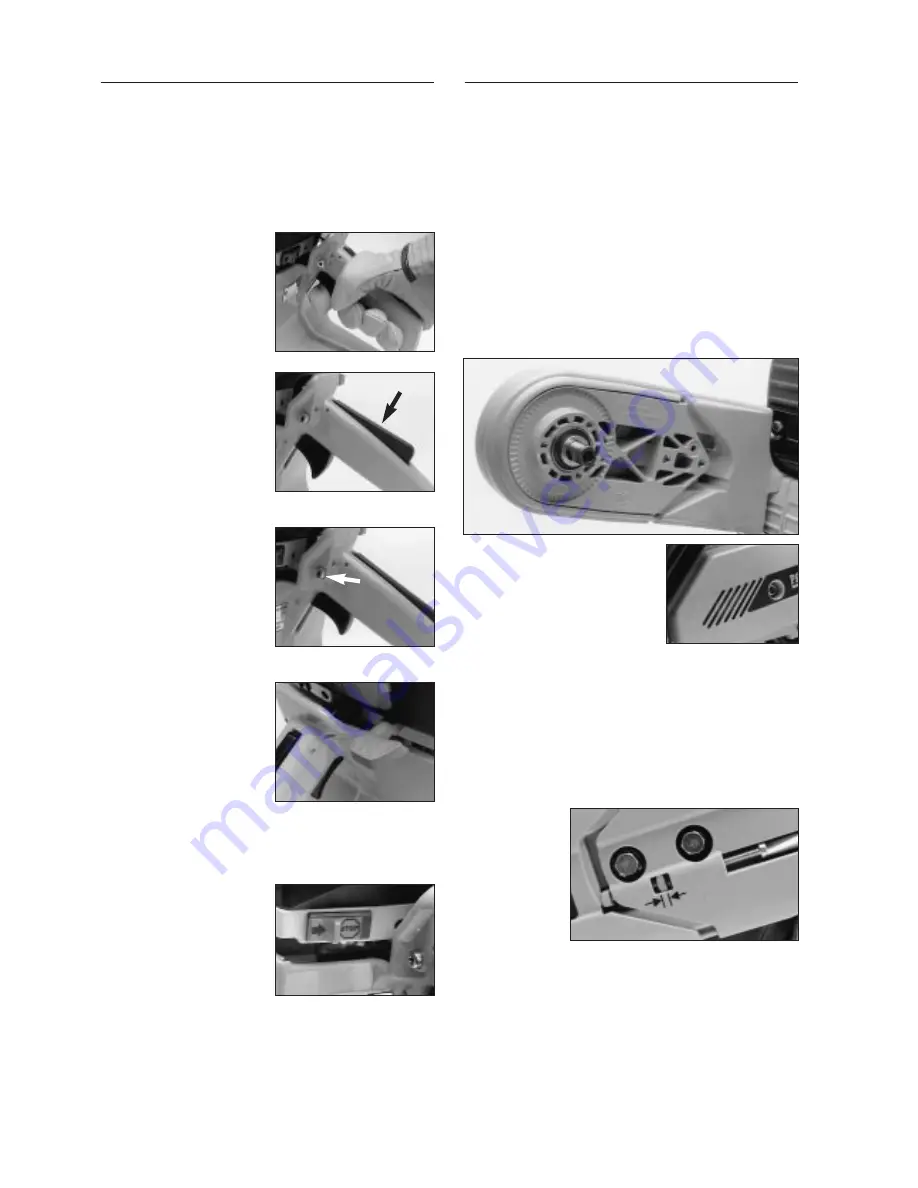
Controls
The basic principle behind the controls needed while the
machine is running is that the operator should not need
to release his grip on the handle. Therefore, all the con-
trols are gathered together on the rear handle – for both
safe and comfortable operation.
The size and the shape of the controls make them
easy to operate with thick gloves on – gloves should
always be used for cutting operations.
Throttle control
The throttle control has
been thoroughly tested.
The spring-loaded counter-
balance, its stroke, design
and precise positioning are
all optimised for best
“finger-tip comfort”.
Throttle trigger lockout
The throttle control is block-
ed in the idling position – a
safety device to prevent
accidental acceleration. The
inhibitor, on the upper face
of the handle, is released
when the driver grasps the
handle.
Starting throttle catch
The throttle control can be
locked in a partially open
setting which ensures the
correct throttle opening for
starting, with either a cold
or warm engine. As soon as
the throttle control is pres-
sed, the catch is released.
Choke
On the K950/K1250 Active,
the choke control is pulled
outwards, a more easily
noticeable indication that
the choke is engaged. The
choke control does not act
on the throttle shutter;
instead, the partial-throttle
setting is governed by the
starting throttle catch during
start-up.
Stop control
The stop control can be
operated with the thumb
without the operator having
to release the handle. The
control cuts the ignition.
8
Cutting unit
Belt drive
The cutter blade on the K950/K1250 Active, as on most
other Partner cutters, features one drive belt leading
from a pulley on the crankshaft to the pulley on the
spindle shaft. This design has the multiple advantages of
simplicity, reliability and low weight.
It is also important from the safety viewpoint. If the
cutter blade comes to a sudden stop, the drive belt will
slip and allow the engine to come to a halt more slowly.
The cutter arm is split to permit convenient belt replace-
ment and adjustment of belt tension.
Fully sealed transmission casing
Large machines like the K950 and K1250 Active are
often used for wet-cutting operations. Water on the belt
functions as a lubricant but also increases the risk of
belt slip. These machines are therefore equipped with a
sealed casing that prevents
water from reaching the belt.
Dust is also kept away from the
belt, thus reducing wear. In order
for the transmission to be suffici-
ently cooled, the casing features
cooling-air vents at the clutch.
Semi-automatic belt tensioning
Opinions as to what is the “correct” belt tension vary
from one operator to another. Partner’s semi-automatic
belt tensioning system solves this problem – a standard-
ised spring provides the correct tensioning force.
In precisely controlled experiments in the laboratory,
Partner has computed the optimum belt tension which
gives the belt maximum service life allied to perfect
application pressure before it slips against the pulley.
Belt tension
has to be ad-
justed occasion-
ally owing to
stretching and
wear of the belt.
This is done
quickly in three
stages.
Drive belt
The drive belt in a cutting machine is subjected to se-
vere and uneven loads and sometimes also to immense
load peaks. The drive belt also operates on relatively
small-diameter pulleys, which imposes particular
demands on the belt. To the naked eye, original-specifi-
cation Partner belts may look like any other drive belt,
but they are specially designed for their specific func-
tion. The belt-tensioning rating, which is determined by
the adjustment spring, is tested using genuine Partner
belts.