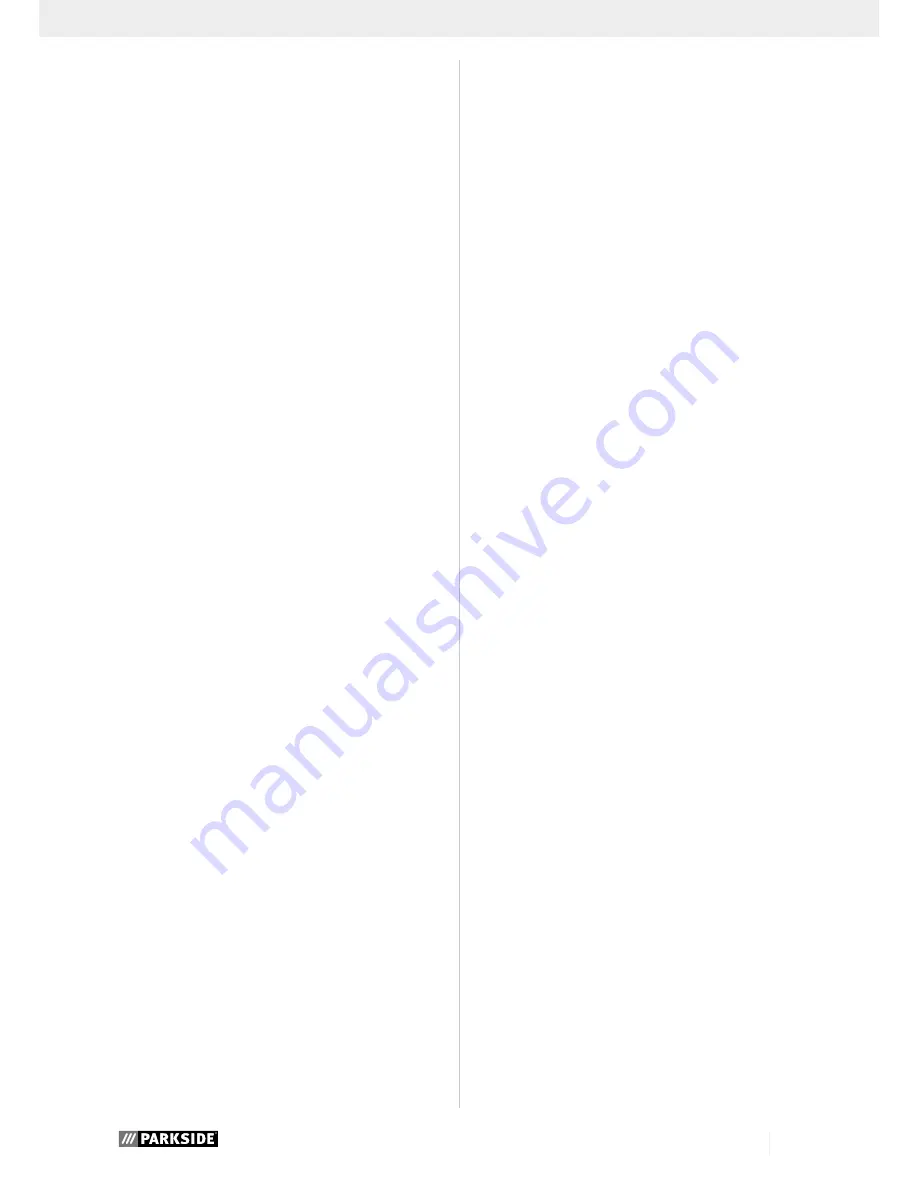
11
GB/IE/NI
The noise emission values were measured in accordance
with EN ISO 3744:2010.
Wear hearing protection.
The effects of noise can cause a loss of hearing.
7. Before starting the equipment
Before you connect the equipment to the mains supply make
sure that the data on the rating plate are identical to the
mains data.
•
Check the equipment for damage which may have oc-
curred in transit. Report any damage immediately to the
transport company which was used to deliver the com-
pressor.
•
Install the compressor near the point of consumption.
•
Avoid long air lines and supply lines (extension cables).
•
Make sure that the intake air is dry and dustfree.
•
Do not install the compressor in a damp or wet room.
•
The compressor may only be used in suitable rooms (with
good ventilation and an ambient temperature from +5 °C
to 40 °C). There must be no dust, acids, vapors, explosive
gases or inflammable gases in the room.
•
The compressor is designed to be used in dry rooms. It is
prohibited to use the compressor in areas where work is
conducted with sprayed water.
•
The oil level in the compressor pump has to be checked
before putting the equipment into operation.
8. Attachment and operation
m
Important!
You must fully assemble the appliance before using it
for the first time!
You will require the following tools for assembly and instal-
lation: Open-ended wrench size 12, 13 and 14 mm (not
included)
8.1 Fitting the wheels (Fig. 4,5)
•
Fit the supplied wheels as shown.
8.2 Fitting the supporting feet (Fig. 4,6)
•
Fit the supplied supporting foot as shown.
8.3 Fitting the air filter (Fig. 7,8)
•
Remove the transportation stop (B) and screw the air filter
(15) to the equipment.
8.4 Changing the transportation cover (A) (Fig. 9,10)
•
Remove the transportation cover (A) from the oil filter
opening (20) and insert the supplied oil sealing plug (16)
into the oil filler opening.
8.5 Mains connection
•
The compressor is equipped with a mains cable with
shock-proof plug. This can be connected to any 220 -
240 V
~
50 Hz shock-proof socket.
•
Before you use the machine, make sure that the mains
voltage is the same as the operating voltage (see the rat-
ing plate).
•
Long supply cables, extensions, cable reels etc. cause a
drop in voltage and can impede motor start-up.
•
At low temperatures below +5°C, sluggishness may make
starting difficult or impossible.
8.6 ON/OFF switch (Fig. 2)
•
Pull the ON/OFF switch (17) upwards to switch on the
compressor. To switch off the compressor, press the ON/
OFF switch down.
8.7 Setting the pressure (Fig. 1,3)
•
Use the pressure regulator (5) to set the pressure on the
pressure gauge (4).
•
The set pressure can be drawn from the quick lock cou-
pling (3).
•
The vessel pressure can be read off the pressure gauge
(6).
•
The vessel pressure is drawn from the quick lock cou-
pling (7).
8.8 Setting the pressure switch (Fig. 1)
•
The pressure switch (2) is set at the factory.
Cut-in pressure approx. 8 bar
Cut-out pressure approx. 10 bar.
8.9 Fitting the compressed air hose (Fig. 1, 3)
•
Use the compressed air hose (14) if you intend to carry
out work at a greater distance from the compressor. To
do so, connect the nipple (H) on the compressed air hose
to one of the quick release couplings (3, 7). Then attach
the compressed air tool to the quick-release coupling (I)
on the compressed air hose.
8.10 Overload switch (Fig. 14)
The motor is fitted with an overload switch (26). If the com-
pressor overloads, the overload switch switches off the
equipment automatically to protect the compressor from
overheating. If the overload switch triggers, switch off the
compressor using the ON/ OFF switch (17) and wait until
the compressor cools down. Then press the overload switch
(26) and restart the compressor.
9. Electrical connection
The electrical motor installed is connected and ready
for operation. The connection complies with the appli-
cable VDE and DIN provisions.
The customer‘s mains connection as well as the exten-
sion cable used must also comply with these regula-
tions.
Important information
In the event of an overloading the motor will switch itself off.
After a cool-down period (time varies) the motor can be
switched back on again.
Damaged electrical connection cable
The insulation on electrical connection cables is often dam-
aged.
Содержание PKO 270 A4
Страница 4: ...10 11 6 7 12 13 8 9 9 B A D E C C D F 15 max min 18 16 20 24 22 25 22 14 26 G ...
Страница 63: ......