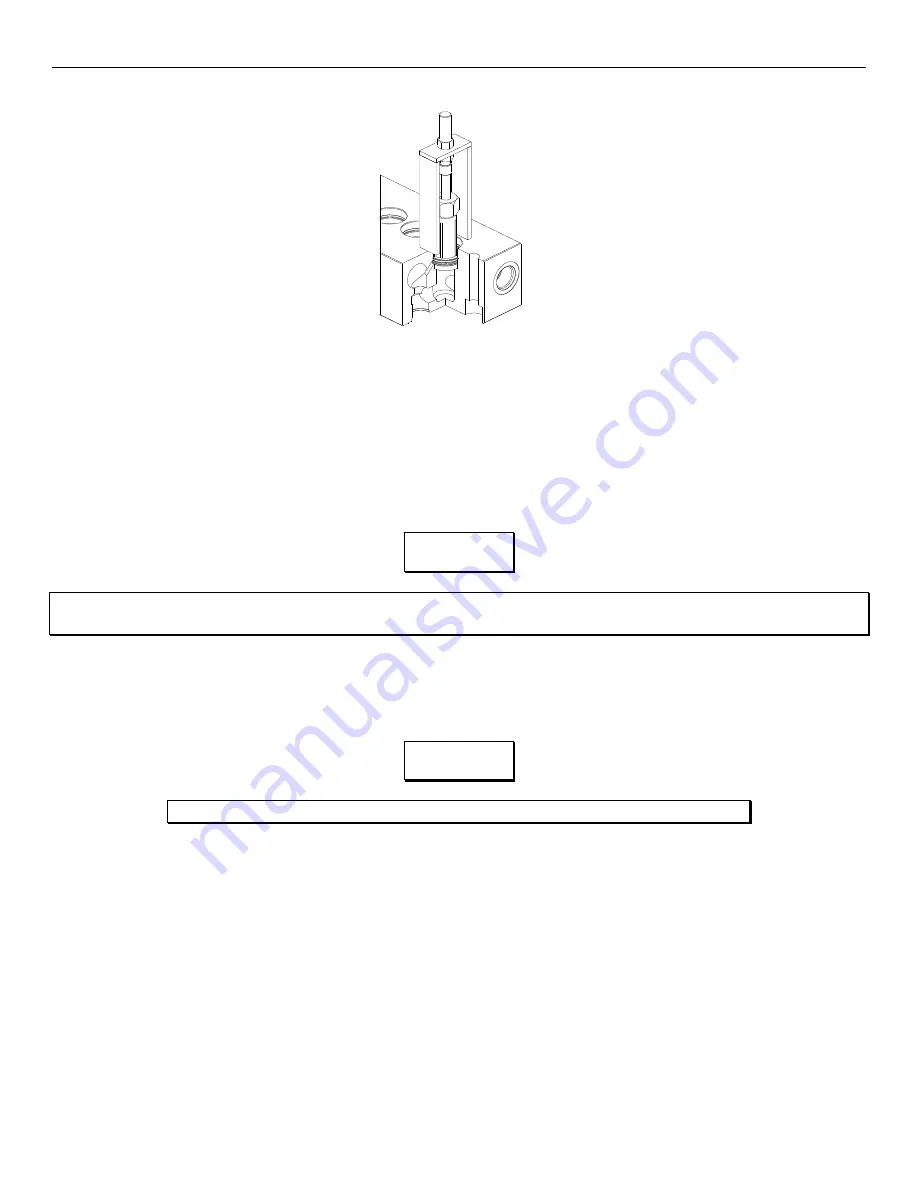
708 Series
High Pressure Titanium Positive Displacement Pump
24
Fig. 10: Weep Ring Extraction
With a flat screwdriver remove the high-pressure seals (40). Manually remove the high-pressure seal spacer (40).
You must clean and inspect the following parts for re-use:
•
Spacer, High-Pressure Seal (39): PN. 70-6016
•
Spacer, Low-Pressure Seal (39): PN. 70-6016
Insert the high-pressure seal spacer (39) into the bore.
Insert the high-pressure seal (40) into the bore until the seal is fully seated on the high-pressure seal spacer (39).
Insert the weep ring (41) into the bore after the installation of the high-pressure seals (39). Install the snap ring (42) using
the snap ring pliers.
Insert the low-pressure seal spacer (39) and press in the new low-pressure seal (43). The manifold seal servicing is
complete.
ATTACHING THE MANIFOLD TO THE CRANKCASE
You will need these tools and parts to do the following:
9/16” Socket/ Socket Wrench (for 708-5)
1/2” Socket/ Socket Wrench (for 708-3)
3/16” Allen Wrench (for 708-1)
Dead Blow Hammer
Dead Blow Hammer
Manifold Bolt (58): PN. 70-6055 (for 708-5)
Manifold Bolt (58): PN. 70-6008 (for 708-3)
Manifold Screw (58): PN. 70-6046 (for 708-1)
Ceramic Lubricant: PN. 85-0087
Anti-Seize Lubricant: PN. 85-0094
NOTE
A light coating of silicon grease (PN. 21-1122) should be used on all new o-rings and seals.
Use of any other type of grease may result in o-ring or seal failure.
NOTE
Ensure that the snap ring (42) is fully seated in the snap ring groove before continuing.
Содержание Pure Water Series
Страница 2: ......
Страница 3: ...THE PURE WATER SERIES 400 2000 GPD USER GUIDE REFERENCE MANUAL ...
Страница 4: ......
Страница 7: ......
Страница 9: ......
Страница 62: ...TROUBLESHOOTING Figure 8 0 Troubleshooting Flow Diagram T ...
Страница 63: ...TROUBLESHOOTING Figure 8 0 Troubleshooting Flow Diagram CONTINUED T ...
Страница 64: ...DRAWINGS AND DIAGRAMS 38 VMT v JUNE 2008 9 0 DRAWINGS AND DIAGRAMS ...
Страница 65: ......
Страница 66: ......
Страница 67: ......
Страница 68: ...Pure Water Semi Modular 600 PWSM 600 Plumbing Diagram Village Marine Tec Freshwater From the Sea November 2004 ...
Страница 71: ...Pure Water Modular 400 PWM 400 Plumbing Diagram Village Marine Tec Freshwater From the Sea November 2004 ...
Страница 72: ...Pure Water Modular 600 PWM 600 Plumbing Diagram Village Marine Tec Freshwater From the Sea November 2004 ...
Страница 74: ...Pure Water Modular 1600 2000 PWM 1600 2000 Plumbing Diagram Village Marine Tec 2008 Freshwater From the Sea ...
Страница 75: ......
Страница 76: ......
Страница 77: ......
Страница 78: ......
Страница 79: ......
Страница 80: ......
Страница 81: ......
Страница 82: ......
Страница 83: ......
Страница 84: ......
Страница 85: ......
Страница 86: ......
Страница 87: ......
Страница 88: ......
Страница 89: ......
Страница 90: ......
Страница 91: ...PARTS REFERENCE 62 VMT v JUNE 2008 Drawing upgrade as of 4 1 2015 ...
Страница 92: ......
Страница 93: ......
Страница 94: ......
Страница 95: ......
Страница 96: ......
Страница 97: ......
Страница 98: ......
Страница 99: ......
Страница 100: ......
Страница 101: ......
Страница 102: ......
Страница 103: ......
Страница 104: ...PARTS REFERENCE 39 VMT v JUNE 2008 10 0 PARTS REFERENCE ...
Страница 105: ......
Страница 106: ......
Страница 107: ......
Страница 108: ......
Страница 109: ......
Страница 110: ......
Страница 111: ......
Страница 112: ......
Страница 113: ......
Страница 114: ......
Страница 115: ......
Страница 116: ......
Страница 117: ......
Страница 118: ......
Страница 119: ......
Страница 120: ......
Страница 121: ......
Страница 122: ......
Страница 123: ......
Страница 124: ...MANUFACTURER S LITERATURE 92 VMT v JUNE 2008 Drawing upgrade as of 4 1 2015 ...
Страница 135: ...MANUFACTURER S LITERATURE 40 VMT v JUNE 2008 11 0 MANUFACTURER S LITERATURE ...
Страница 136: ......
Страница 139: ...LIST OF TABLES Table 1 Approximate Horsepower Required 3 Table 2 Tool List For Pump Service 12 ...
Страница 165: ...708 Series High Pressure Titanium Positive Displacement Pump 26 ...
Страница 166: ...708 5 DRAWINGS ...