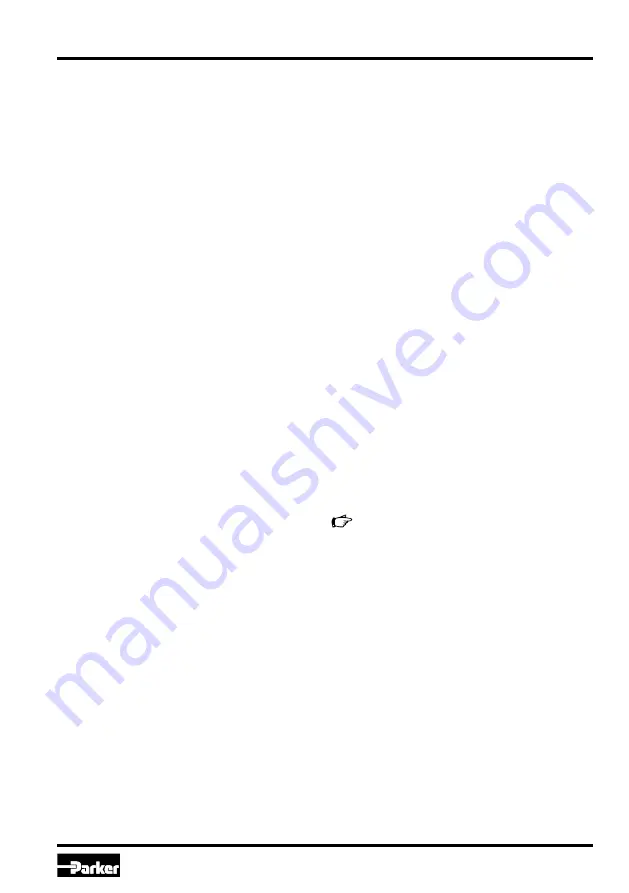
37
Electronics for Closed Loop Control
Series PID00A-40X
Operation Manual
PID00A_10 5715-616 UK.indd CM 14.11.14
Parker Hannifin Corporation
Hydraulics Group
Guarantee of control functionality
Before the tuning of the control loop can com-
mence, the functionality of the control circuit must
be ensured. As previously mentioned, the control-
ler compares command and feedback signal and
adjusts the electrical input to the valve amplifier to
ensure the required velocity. To ensure this func-
tionality, the polarities of command and feedback
signal must be equal.
How can the functionality of the control loop
be achieved?
Firstly you should set off the control loop (set pa-
rameter E2 to value 0 = open loop and transmit
to the electronic) and cause the drive via manual
control to a medium velocity. Subsequently adjust
the first control coefficients as described in chap-
ter “Simple tuning of a velocity control loop” (P16 at
10%) as well as the parameter E2 at 2 = external
closed loop and transmit to the electronic. If this re-
sults in a jump of the drive into its minimum or max-
imum velocity, the polarities are incorrect. Access
now the parameter P12 = feedback signal polari-
ty, change the value and transmit the data. By now
the drive should be adjustable and must remain on
its actual value when you switch on the closed loop
control via parameter E2. Now you should preset
velocity commands and supervise the drive move-
ment. If the drive even tough is running in closed
loop mode, but the direction of the rise and fall of
velocity is not as required, you have to change the
polarities of both command and feedback signal via
the parameters P11 and P12. After that the closed
loop control is running as desired, you can contin-
ue with tuning of the loop.
Tuning of the closed loop control
1. Create a suitable tuning test profile – this will
enable you to evaluate your system response (A
test profile may be generated by an up-streamed
electronic module PZD00A-400). The test profile
should caus e the drive to move from the start
position with the required maximum accelera-
tion to the re quired velocity. At the commanded
velocity the drive should dwell at that rate, this
will give you the opportunity to observe the load
velocity for oscillation. This should be followed
by returning of the drive with a different velocity
to evaluate also the opposite drive direction.
2. Check once more to be sure that P17 and P18
are set to zero.
3. Adjust P16 to a low value, i.e. 10%, and try the
system on the test profile.
Observe the result of the test. There are three pos-
sible outcomes:
• The drive oscillates continuously
Stop the system quickly. Reduce the P16-value
to ½ of the initial guess, and try again.
• The Velocity overshoots the commanded value,
but stops after one or two oscillations
Reduce the P16-value to ¾ of the initial guess,
and try again.
• The drive reaches the commanded position
with no overshoot
The system is usable with the estimated value
of P-gain. You should experiment with stepwise
increasing of the P16-value to see how high a
value the system will tolerate. Accuracy and
response are improved by high values, but do
not allow permanent oscillation!
4. You have now completed the basic tuning for
your control loop. The next step is to test the
performance of the system to see if it meets
your requirements. If not, the electronic has ad-
ditional control features you can use to improve
performance, as explained below.
The parameters P28, E50, E70, E73, E74
will be needed for closed loop velocity
control systems and should therefore be
adjusted accordingly (s. section “Generat-
ing feedback signals”).
Содержание PID00A-40 Series
Страница 44: ......