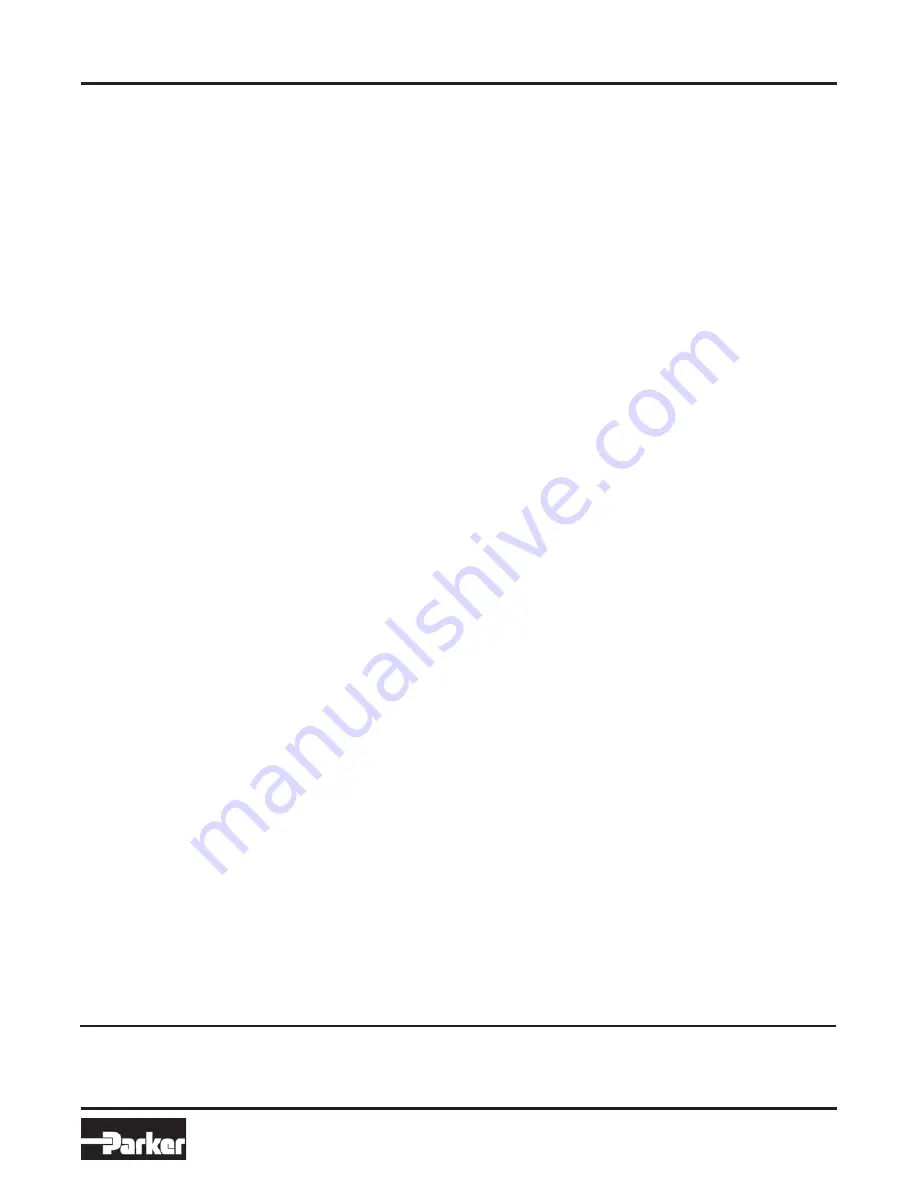
Parker Hannifin Corporation
Hose Products Division
Wickliffe, OH
21
Technical Manual
Parkrimp 1
Bulletin 4480-T20-US
MSDS’S (Available upon request.)
Federal OSHA regulation 29 CFR 1910.1200 requires that we transmit to our customers Material Safety Data Sheets for all material
covered under the law. If you are an employer in SIC 20-39 who has not yet received them, you are required to obtain them from us and
provide the information to employees as directed in Secton (b) of the requlation. Please contact the Hose Products Division - Technical
Services Department: (PH) 440- 943-5700 (FAX) 440- 943-3129.
3.7
Minimum Bend Radius
: Installation of a Hose at less than the minimum listed bend
radius may significantly reduce the Hose life. Particular attention must be given to preclude
sharp bending at the Hose to Fitting juncture. Any bending during installation at less than
the minimum bend radius must be avoided. If any Hose is kinked during installation, the
Hose must be discarded.
3.8
Twist Angle and Orientation
: Hose Assembly installation must be such that relative
motion of machine components does not produce twisting.
3.9
Securement:
In many applications, it may be necessary to restrain, protect, or guide
the Hose to protect it from damage by unnecessary flexing, pressure surges, and contact
with other mechanical components. Care must be taken to insure such restraints do not
introduce additional stress or wear points.
3.10
Proper Connection of Ports:
Proper physical installation of the Hose Assembly requires
a correctly installed port connection insuring that no twist or torque is transferred to the
Hose when the Fittings are being tightened or otherwise during use.
3.11
External Damage:
Proper installation is not complete without insuring that tensile loads,
side loads, kinking, flattening, potential abrasion, thread damage, or damage to sealing
surfaces are corrected or eliminated. See instruction 2.10.
3.12
System Checkout:
All air entrapment must be eliminated and the system pressurized
to the maximum system pressure (at or below the Hose maximum working pressure)
and checked for proper function and freedom from leaks. Personnel must stay out of
potential hazardous areas while testing and using.
3.13
Routing:
The Hose Assembly should be routed in such a manner so if a failure does
occur, the escaping media will not cause personal injury or property damage. In addition,
if fluid media comes in contact with hot surfaces, open flame, or sparks, a fire or explosion
may occur. See section 2.4.
4.0
HOSE AND FITTING MAINTENANCE AND REPLACEMENT INSTRUCTIONS
4.1
Even with proper selection and installation, Hose life may be significantly reduced without
a continuing maintenance program. The severity of the application, risk potential from a
possible Hose failure, and experience with any Hose failures in the application or in similar
applications should determine the frequency of the inspection and the replacement for
the Products so that Products are replaced before any failure occurs. A maintenance
program must be established and followed by the user and, at minimum, must include
instructions 4.2 through 4.7.
4.2
Visual Inspection Hose/Fitting
: Any of the following conditions require immediate shut
down and replacement of the Hose Assembly:
• Fitting slippage on Hose,
•
Damaged, cracked, cut or abraded cover (any reinforcement exposed);
• Hard, stiff, heat cracked, or charred Hose;
• Cracked, damaged, or badly corroded Fittings;
• Leaks at Fitting or in Hose;
• Kinked, crushed, flattened or twisted Hose; and
• Blistered, soft, degraded, or loose cover.
4.3
Visual Inspection All Other:
The following items must be tightened, repaired, corrected
or replaced as required:
• Leaking port conditions;
• Excess dirt buildup;
• Worn clamps, guards or shields; and
• System fluid level, fluid type, and any air entrapment.
4.4
Functional Test
: Operate the system at maximum operating pressure and check for
possible malfunctions and leaks. Personnel must avoid potential hazardous areas while
testing and using the system. See section 2.2.
4.5
Replacement Intervals
: Hose assemblies and elastomeric seals used on Hose Fittings
and adapters will eventually age, harden, wear and deteriorate under thermal cycling
and compression set. Hose Assemblies and elastomeric seals should be inspected and
replaced at specific replacement intervals, based on previous service life, government
or industry recommendations, or when failures could result in unacceptable downtime,
damage, or injury risk.
See section 1.2.
4.6
Hose Inspection and Failure:
Hydraulic power is accomplished by utilizing high-pressure
fluids to transfer energy and do work. Hoses, Fittings, and Hose Assemblies all contribute
to this by transmitting fluids at high pressures. Fluids under pressure can be dangerous
and potentially lethal and, therefore, extreme caution must be exercised when working
with fluids under pressure and handling the Hoses transporting the fluids. From time to
time, Hose Assemblies will fail if they are not replaced at proper time intervals. Usually
these failures are the result of some form of misapplication, abuse, wear, or failure to
perform proper maintenance. When Hoses fail, generally the high-pressure fluids inside
escape in a stream which may or may not be visible to the user. Under no circumstances
should the user attempt to locate the leak by “feeling” with their hands or any other part
of their body. High-pressure fluids can and will penetrate the skin and cause severe
tissue damage and possibly loss of limb. Even seemingly minor hydraulic fluid injection
injuries must be treated immediately by a physician with knowledge of the tissue damaging
properties of hydraulic fluid.
If a Hose failure occurs, immediately shut down the equipment and leave the area until
pressure has been completely released from the Hose Assembly. Simply shutting down
the hydraulic pump may or may not eliminate the pressure in the Hose Assembly. Many
times check valves, etc., are employed in a system and can cause pressure to remain in
a Hose Assembly even when pumps or equipment are not operating. Tiny holes in the
Hose, commonly known as pinholes, can eject small, dangerously powerful but hard to
see streams of hydraulic fluid. It may take several minutes or even hours for the pressure
to be relieved so that the Hose Assembly may be examined safely.
Once the pressure has been reduced to zero, the Hose Assembly may be taken off
the equipment and examined. It must always be replaced if a failure has occurred.
Never attempt to patch or repair a Hose Assembly that has failed. Consult the nearest
Parker distributor or the appropriate Parker division for Hose Assembly replacement
information.
Never touch or examine a failed Hose Assembly unless it is obvious that the Hose no
longer contains fluid under pressure. The high-pressure fluid is extremely dangerous
and can cause serious and potentially fatal injury.
4.7
Elastomeric seals:
Elastomeric seals will eventually age, harden, wear and deteriorate
under thermal cycling and compression set. Elastomeric seals should be inspected and
replaced.
4.8
Refrigerant gases:
Special care should be taken when working with refrigeration systems.
Sudden escape of refrigerant gases can cause blindness if the escaping gases contact
the eye and can cause freezing or other severe injuries if it contacts any other portion of
the body.
4.9
Compressed natural gas (CNG):
Parker CNG Hose Assemblies should be tested after
installation and before use, and at least on a monthly basis per AGA 1-93 Section 4.2
“Visual Inspection Hose/Fitting”. The recommended procedure is to pressurize the Hose
and check for leaks and to visually inspect the Hose for damage.
Caution:
Matches, candles, open flame or other sources of ignition shall not be used
for Hose inspection. Leak check solutions should be rinsed off after use.