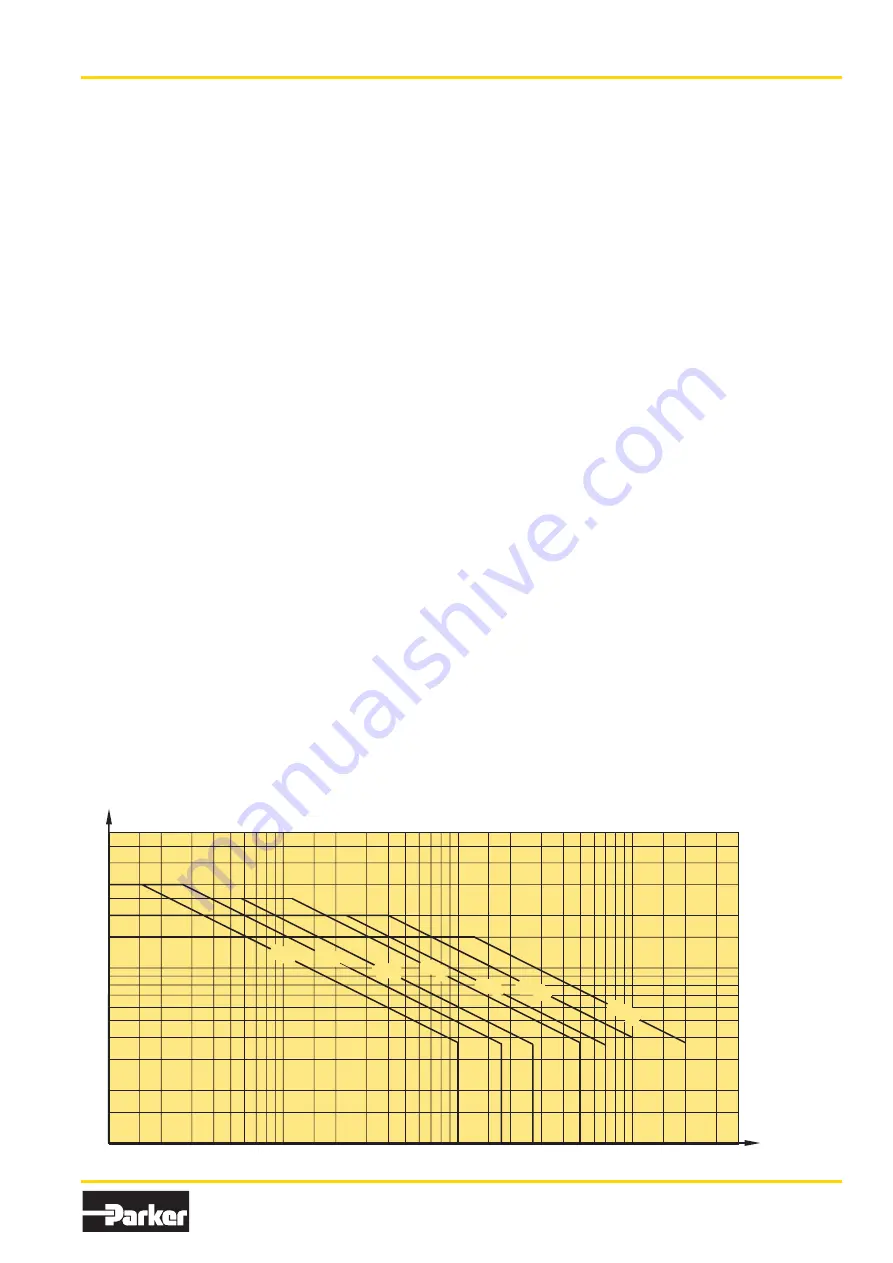
15
P1D
Cylinder
05.03
www.parker.com/euro_pneumatic
4,0
3,0
2,0
1,5
1,0
0,5
0,4
0,3
0,2
0,1
1
2
3 4 5
10
20
30 40 50
100
200 300
500
1000
2000
Ø32
Ø40
Ø50
Ø63
Ø80
Ø100
Ø125
Speed [m/s]
Mass [kg]
Material specification
Standard design
Body extrusion
Natural colour, anodised aluminium
End cover
Black anodised aluminium
End cover inserts
POM
End cover nuts/screws
Zinc plated steel 8.8
Piston rod nut
Zinc plated steel
Piston rod
Stainless steel, X 10 CrNiS 18 9
Scraper ring
PUR
Piston rod bearing
POM
Piston
POM
Piston bearing
POM
Magnetic ring
Plastic bound magnetic material
Piston bolt
Zinc plated steel
Piston seal
PUR
O-rings
Nitrile rubber, NBR
End-of-stroke washers
PUR
Cushioning seals
PUR
Cushioning screws
LCP
P1D Clean
Transparent moulding
Silicone
Transparent cover
ABS
Screws, sensor system
Stainless steel, A2
Upper seal and lower
seal, protective cover
Santopren
Sealing plugs
PA
Piston rod nut
Stainless steel, A2
P1D Flexible Porting
Connection hardware Ø32-63
POM
Elbow fittings Ø32-63
PA
Straight fittings on body extrusion Ø32-63
PA
Straight fittings in ports
Nickel plated brass
Seal, connection hardware
Nitrile rubber NBR
P1D Tie-Rod
Tie-rods
Stainless steel, X 10 CrNiS 18 9
Design variants
Low temperature design
Seals/scraper ring
Polyurethane PUR
Piston
Anodised aluminium
Piston/piston rod bearing UHMWPE plastic
High temperature design
Seals/scraper ring
Fluorocarbon rubber, FPM
Piston
Anodised aluminium
Piston/piston rod bearing Bronze filled PTFE
Low pressure hydraulics
Seals/scraper ring
Nitrile rubber, NBR
Piston
Anodised aluminium
Piston/piston rod bearing UHMWPE plastic
Cylinders for dry rod operation
Seals/scraper ring
FPM/HDPE
Option
Piston rod material
Hard-chromium plated steel, Fe 490-2 FN
Acid-proof steel, X 5 CrNiMo 17 13 3
Hard-chromium plated stainless steel,
X 10 CrNiS 18 9
Cushioning characteristics
The diagram below is used for dimensioning of cylinders related
to the cushioning capacity. The maximum cushioning capacity
shown in the diagram assumes the following:
• Low load, i.e. low pressure drop across the piston
• Equilibrium speed
• Correctly adjusted cushioning screw
• 6 bar at cylinder port
The load is the sum of internal and external friction, plus any
gravitational forces. At high relative load (pressure drop
exceeding 1 bar), we recommend that for any given speed, the
mass should be reduced by a factor of 2.5, or for a given mass,
the speed should be reduced by a factor of 1.5. This is in relation
to the maximum performance given in the diagram