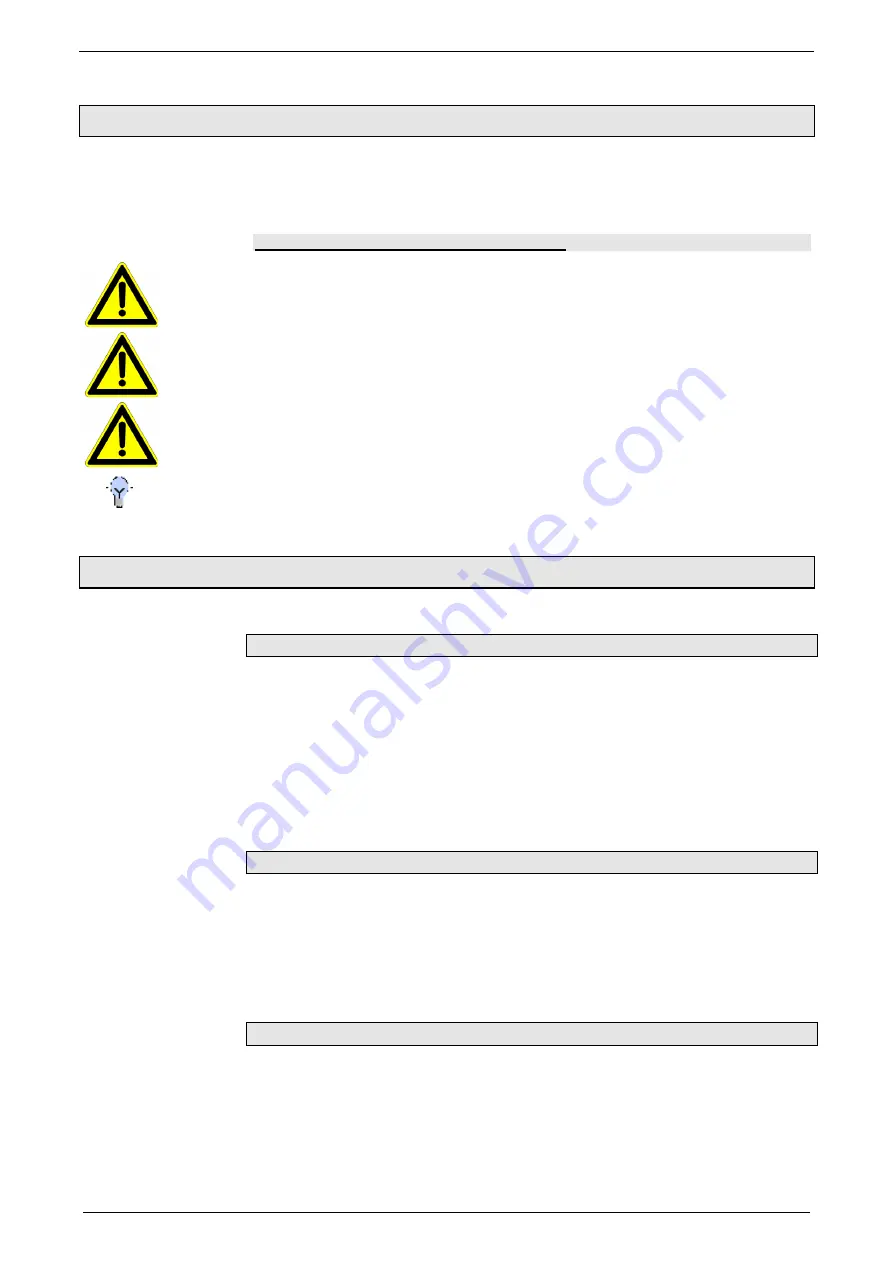
Parker EME
Introduction
192-510014 N04 March 2010
7
1.2.3.
Identifying Residual Dangers and Hazardous Areas
If there are still residual dangers present to persons or property from the linear
actuator in spite of operating it in a safe manner, the user must make reference to
these residual dangers through signs and written rules requiring appropriate
procedures.
The following safety signal words are used:
Danger
Indicates that an imminent hazardous situation may lead to death or serious bodily harm -if
not prevented using appropriate safety measures-.
Warning
Indicates a potentially hazardous situation which, if not avoided using appropriate safety
measures, could result in serious or minor injury.
Caution
Indicates a potentially hazardous situation which, if not avoided using appropriate safety
measures, may result in minor injury or damage.-
Hint
Provides important information about the product, how to handle the product or about the
part of the manual to which particular attention must be paid.
1.2.4.
Working safely
Heed the Instructions
The information (such as instructions and notes) contained in this manual must be
heeded for all work involved in installing, commissioning, setting up, operating,
changing operating conditions and modes, servicing, inspecting and repairing the
unit.
The manual must be available close to the linear module during the performance of
all tasks.
It is impermissible to operate the liner module if it is not in perfectly functional
condition.
Operating personnel.
The following jobs must only be performed by appropriately trained and authorized
personnel:
Installation and set-up tasks on the linear actuator
Attaching safety transmitter switches (initiators)
Connecting the drive and testing the motion direction
Instructions for Special Hazards
The linear module must be fixed or supported in accordance with the indications in
this manual.
The operator must ensure that operation of the linear module does not cause any
danger.
If the linear module moves in hazardous areas, these areas can be safeguarded
with safety transmitter switches.