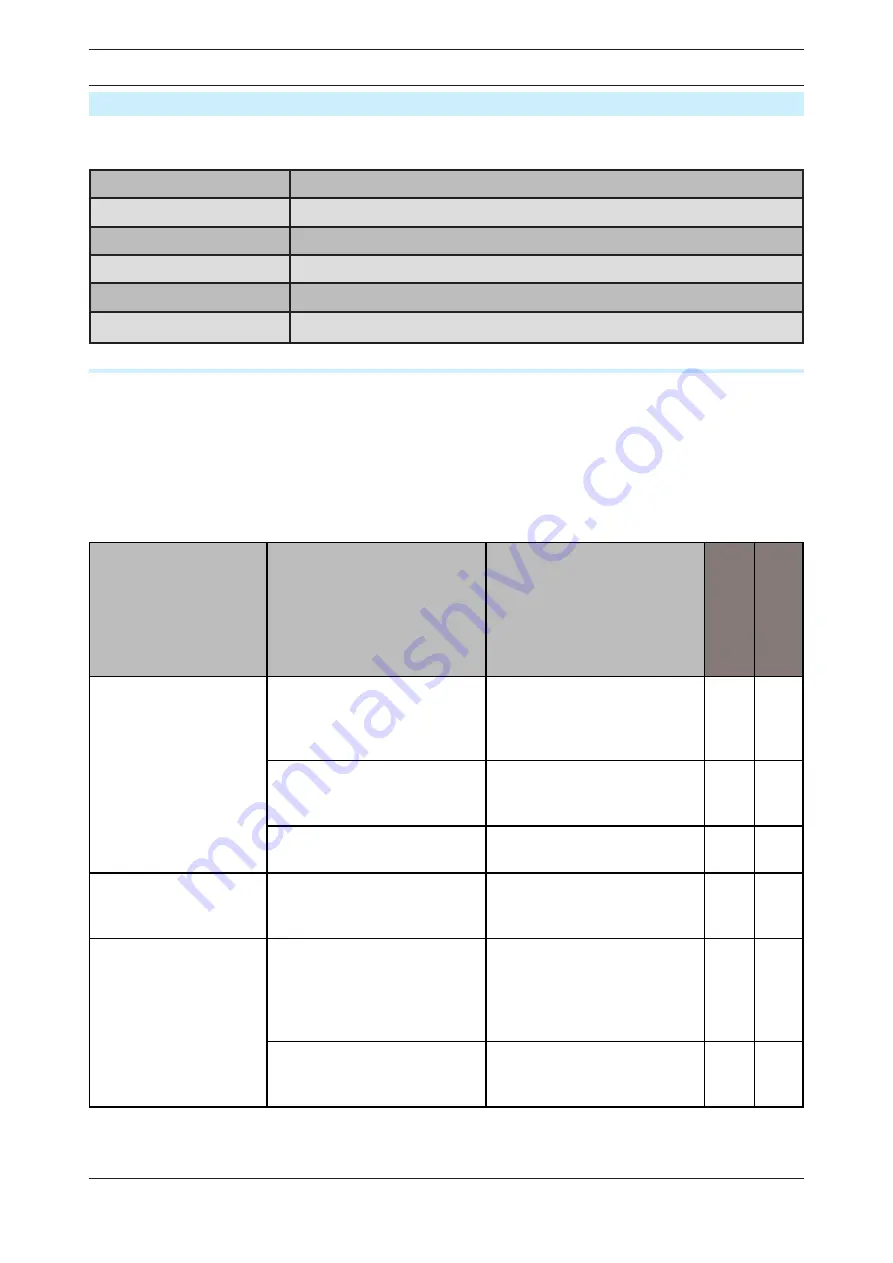
EN
| User Manual
Identify and eliminate faults
44
KA-MT 10-95/D3
Identify and eliminate faults
The following table provides information on what designatory abbreviations are to be used for
the various components. These designations are also found in the technical documentation.
Used abbreviation
Component
PI
Pressure gauge
PDI
Differential pressure gauge
V1–V2 (Y2–Y1)
Main valves (solenoid valves)
V3–V4 (Y3–Y4)
Expansion valves (solenoid valves)
V5–V6
Check valves
Summary of faults
There are different fault types. In the case of most electrically caused faults (e.g. short circuit,
defective fuse, etc.) the expansion valve closes and the regeneration is interrupted. In the
case of some process faults, the dryer will continue to operate for some time. Other faults on
the dryer become noticeable e.g. due to unusual noises and ran pressures.
The following table shows who is allowed to remedy a fault: the owner’s specialist personnel
or the manufacturer’s service engineer.
Table of possible faults
Fault
Possible cause
Remedy
Specialised
personnel
Service
technician
Excessive dam pres-
sure during regener-
ation
Muffl er or fi lter element of
the muffl er is contaminated.
Check muffl ers or fi lter
elements for contamination,
clean if nec., and poss.
renew.
•
•
Expansion valve V3/V4 does
not open correctly.
Check expansion valve for
contamination, if nec. clean/
renew.
•
•
Dust sieves are contami-
nated.
Clean or renew dust sieves.
•
•
Vessel pressure is too
low
Excessive differential pres-
sure on the upstream fi lter.
Check differential pressure
on the upstream fi lter, if.
nec. renew fi lter element.
•
No pressure build-up
The compressed air system
upstream of the dryer is not
pressurised.
Check whether the
compressed air system
upstream of the dryer is
pressurised. Remove any
faults.
•
Solenoid valve Y1/Y2 does
not open correctly.
Check supply voltage, ca-
ble, contacts and solenoid;
replace, if necessary.
•
•