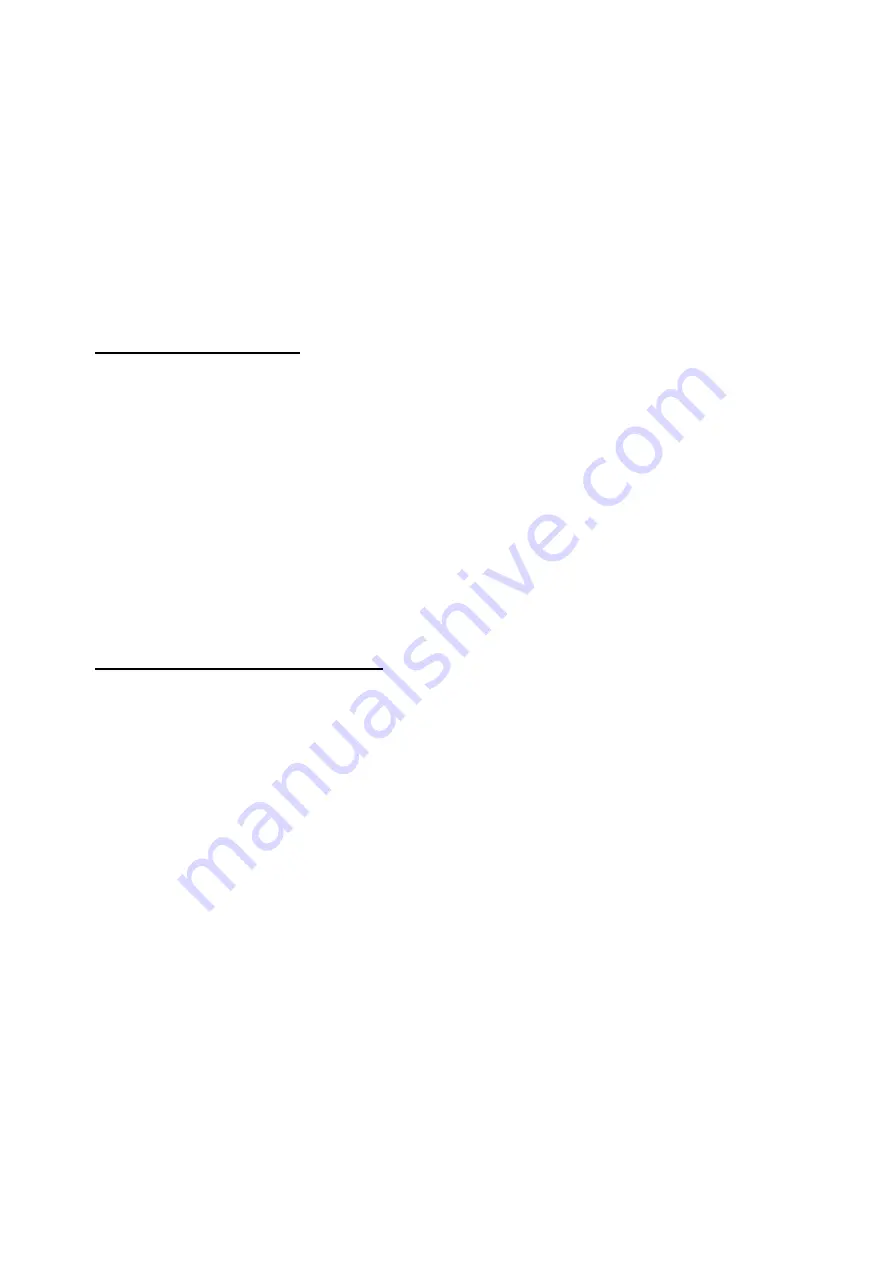
B.89.809 Rev C
10
© Parker Hannifin, 2015
www.parker.com/hfde
System Condition Changes
Changes in the system operating condition, flow, temperature, pressure or vibration can result in previously sedimented
contaminant being retained into the flowing oil. It is also possible that these changes may cause partially contaminated
filter elements to shed particulate into the system. Samples should therefore, be extracted when the system is in a steady
state condition and the result less likely to be distorted by contaminant peaks.
Taking a Sample
Extract a sample while the system is operating under consistently controlled conditions. Adopt a consistent technique.
Spill off at least 200ml of fluid to flush the sampling port of residual contaminant.
Leave bottle capped until ready to extract the sample.
Fill the bottle to approximately 80% and cap immediately after extracting the sample.
Fluid Sample Extraction
Flow Rate
Variations in the sampling flow rate may affect the result from bottle samples. The flow rate through a sampling port from
an operating hydraulic system will vary dependant upon the system pressure, the port restriction and fluid viscosity. For
best trend monitoring, it is necessary to maintain these conditions consistently when extracting Bottle Samples.
Sampling Valves
There are a number of proprietary sampling valves available, which adhere to good theoretical principles. However, they
do tend to generate a level of precision and cost which is unnecessary for trend monitoring.
Sampling points
Sampling points should enable extraction of a sample without changing the system’s condition. Fine control needle valves
are not desirable, as they have a tendency to silt up under some operating conditions, causing the distribution of
contaminants in the fluid to be changed. The sampling port should be protected to maintain cleanliness and thoroughly
flushed before collecting the sample for analysis.
Sample Handling and Preparation
Bottle Cleanliness
It is preferable that bottles have sealing screw caps and both parts are cleaned to a suitable level in accordance with
ISO3722.
The bottle should not contain more than one tenth of the number of particles per 100ml than are expected to be
monitored. Standard Parker Hannifin bottles are supplied clean to ISO 13/11 or better in a Class 10,000 Clean Room and
should not be used to accurately count oils cleaner than ISO 16/14 although they may be used for “trend monitoring” at
lower levels.
NOTE: A Class 10,000 clean room is designed to never allow more than 10,000 particles (0.5 microns or larger) per cubic
foot of air. So as you can quantify this, a typical office buildings' air contains between 500,000 to 1,000,000 particles (0.5
microns or larger) per cubic foot of air.
The bottle should remain capped until time of sample filling and be re-capped immediately afterwards.
Sample Mixing
Sedimentation of contaminant in a sample will occur, the rate of which is dependent upon both the fluid and particle
characteristics.
Methods of sample agitation have not been provided, as they are likely to inconsistently distort the analysis of results.
Samples should be analysed, without delay, once agitated.
Содержание icountBS
Страница 1: ...B 89 809 Rev C Parker Hannifin 2015 www parker com hfde icountBS User Manual GB ...
Страница 29: ...B 89 809 Rev C 29 Parker Hannifin 2015 www parker com hfde NOTE Do not connect IBS directly to the PC ...
Страница 30: ...B 89 809 Rev C 30 Parker Hannifin 2015 www parker com hfde ...
Страница 31: ...B 89 809 Rev C 31 Parker Hannifin 2015 www parker com hfde ...
Страница 32: ...B 89 809 Rev C 32 Parker Hannifin 2015 www parker com hfde ...