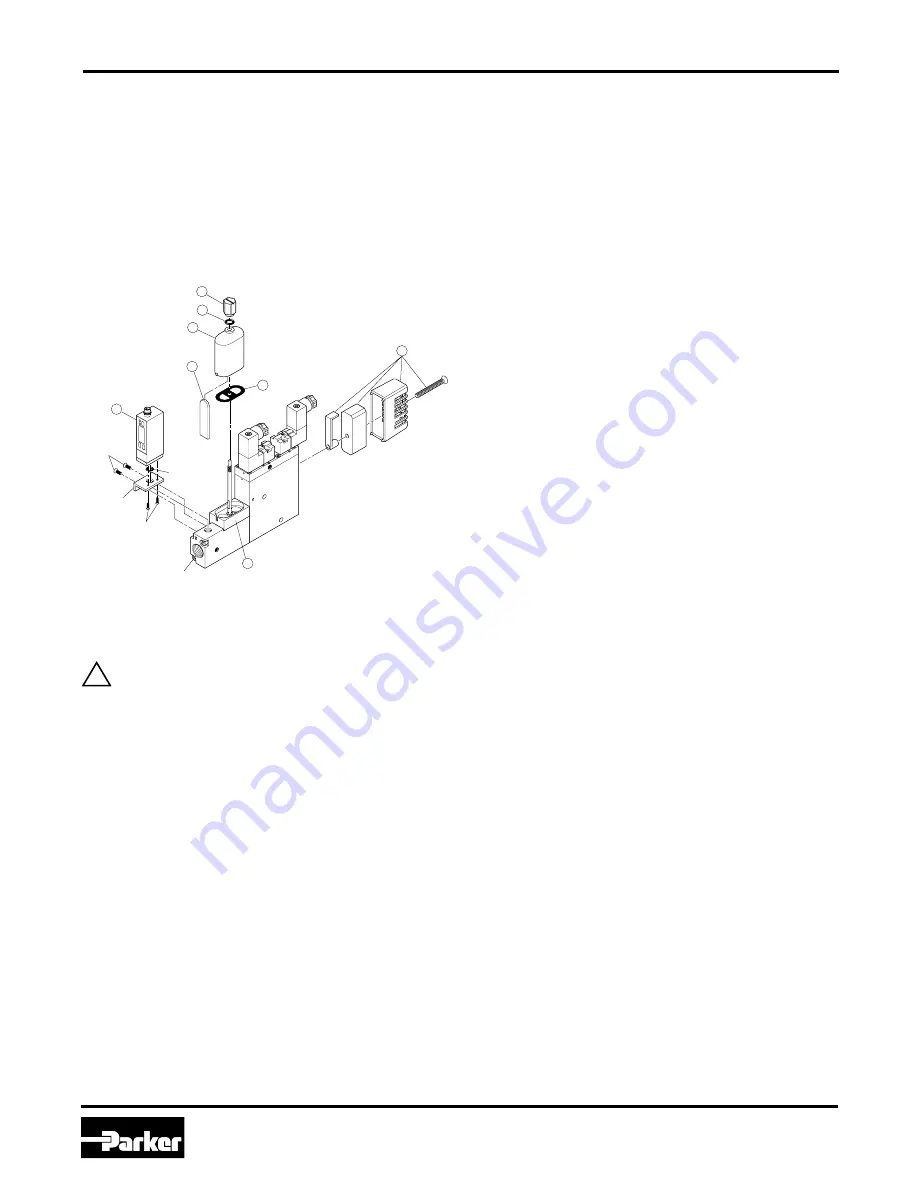
8
VAC-SIF-05
Training & Maintenance Manual
CVX0260B
Parker Hannifin Corporation
Pneumatic Division
Richland, Michigan
www.parker.com/pneumatic
Scheduled Maintenance
Filters –
Periodic maintenance of the vacuum filter is
necessary. The frequency of maintenance depends on the
environment and application. As the filter collects product from
the environment the maximum vacuum level potential and
response time may vary.
Silencer –
Periodic maintenance of the exhaust silencer may
be required. The frequency of maintenance depends on the
environment and condition of the air supply.
Sensor
Sensor
O-Ring
(P5)
Sensor
Mounting
Brkt.
Sensor
Mounting
Brkt. Screws
(M3x5)
Sensor
Mounting
Screws
(M2x6)
Vacuum
Port
Filter
Base
Filter
Element
Filter
Gasket
5
15
6
7
3
Filter
Cap
Filter O-ring
(M8x1.0)
4
Filter
Housing
2
1 Silencer
!
Cautions
• The CVX0260B does not require lubrication to function like
other pneumatic components.
• The CVX0260B functions efficiently at 70 PSI while in
operation. Regulate the inlet air pressure to 70 PSI during
operations.
• Inlet compressed air levels below 70 PSI will yield lower
vacuum levels and could effect the overall performance of
the system.
• Operating pressure must be maintained during an
Emergency Stop Condition for the Emergency Operating
System to maintain the current operating mode of the
vacuum generator.
• Filtrate the inlet air to protect the CVX0260B against
contaminating matter typically found in compressed air
systems ( i.e. rust, water, compressor oil, or other foreign
particles). A standard 40 micron filter is recommended.
• The CVX0260B inlet compressed air must be filtered,
regulated, and periodically maintenance to insure
maximum operating performance and warranty.
• The air economizing functions and check valves require
proper fittings and suction cups to prevent vacuum
leakage. The vacuum ports are 3/8" G or 3/8" NPT female
threads and require appropriate fittings to properly seal the
systems. For NPT fittings, use a dry seal or tape to seal
the fittings throughout the system.
• Primary vacuum filtration is always recommended between
the cups and the vacuum ports of the generator. Collection
of particles and other matter from the work piece will
reduce the maximum vacuum level of the unit over a period
of use. The frequency of the filter maintenance will vary
with each environment and application.
• Each CVX0260B incorporates a small filter housed on the
body to protect the internal components of the generator.
Additional maintenance of this filter will also vary with each
environment and application.
Trouble shooting
(1) Most systems are not closed. Vacuum Systems
can have leaks in the fittings, leaks through the
product, and by seal at the interface of the cup
and the product to be handled. Excessive leakage
may create a situation where the system vacuum
pressure cannot obtain part presence level, “P_3” or
Air Economizing Level “n_1”. Either the leaks in the
system must be eliminated or the sensor settings
will have to be changed to meet the parameters of
the vacuum system.
(2) The Nozzle / Diffuser relationship with the
compressed air is critical for peak performance. All
manufactures state an optimum inlet pressure for
the vacuum generators. Increasing compressed air
pressure above the optimum inlet pressure may
not increase the degree of vacuum and in some
cases may deter the creation of vacuum pressure.
Compressed air pressure less than optimum inlet
pressure will decrease the vacuum pressure and
flow performance of the vacuum generator.
(3) Exhaust flow paths typically have exhaust silencers.
These silencers can become clogged which creates
a backpressure on the Nozzle/Diffuser relationship.
This will decrease the maximum vacuum pressure
and flow performance of a generator.
(4) The CVX0260B unit has a built in Vacuum Filter.
These filters can become clogged which creates a
pressure drop in the system. This pressure drop will
reduce the available vacuum pressure at the cup.
It is the vacuum pressure that holds the part and cup
together. The vacuum generator creates a pressure
differential between the inside of the cup and the outside. It
is this differential pressure, the difference between the inside
pressure (vacuum pressure) and atmospheric pressure
that holds the cup and work piece together. If the generator
cannot create the system vacuum pressure, then it cannot
create enough differential pressure between the inside of the
cup and the work piece to hold the part. The part will either
drop or it will not be picked up.
Trouble shooting a vacuum system has a lot of the same
basic trouble shooting of compressed air systems. What is
the inlet pressure, use of the manual overrides to confirm
valves are “ok”, checking solenoid LED’s for electrical signals.
The main troubleshooting of vacuum systems is to determine
“WHY” the vacuum system pressure is not being created to
hold a part.
Maintenance & Troubleshooting