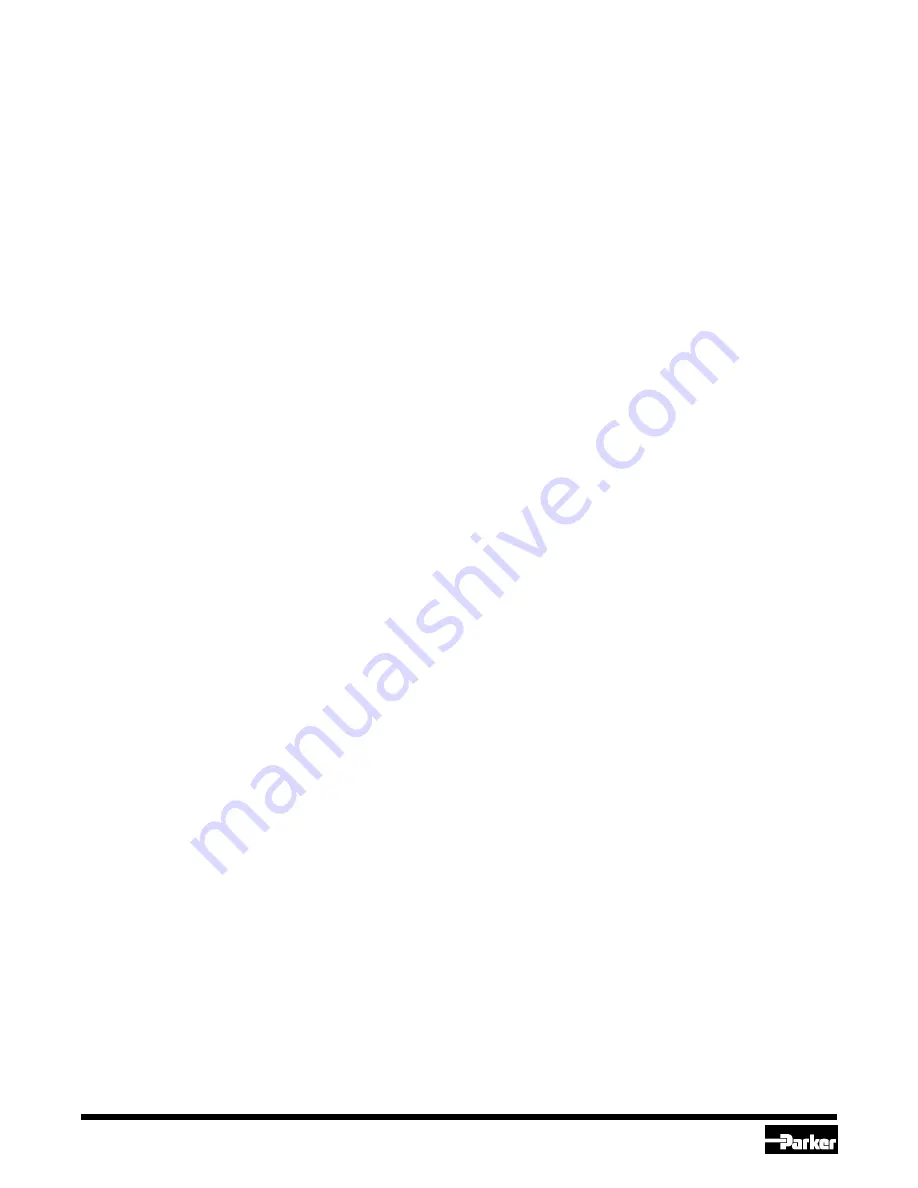
Refrigerating Specialties Division
6
The inlet pressure acts on the diaphragm. When the force
created by the pressure exceeds the force of the range spring,
the diaphragm is lifted off of the valve seat and flow occurs
through the valve seat, from the regulator inlet to the outlet.
Increased inlet pressure lifts the diaphragm further, allowing
increased flow. Decrease in inlet pressure causes the dia-
phragm to move closer to the valve seat, reducing the flow.
Thus, the regulator acts to maintain the inlet pressure approxi-
mately constant. If the inlet pressure drops below the regulator
setting, the diaphragm closes off the flow to keep the inlet
pressure from going below the set point, subject to limits of seat
leakage tolerance, or leakage due to dirt particles on the seat
surfaces.
Adjustment, A2BM
Adjust the controller sensitivity to the desired point according
to the manufacturer’s directions. Loosen the pressure adjust-
ing screw lock nut and adjust pressure screw until disengaged
with the valve actuating stem. Run the system until the tem-
perature at the sensing element reaches the desired level.
Adjust the controller (thermostat) setting to a reading that will
cause the cam of the motor to rotate and stop in center cam
position. Turn the adjusting screw to engage the valve actuat-
ing stem, and adjust until the desired inlet pressure for this
temperature and load condition is reached. Turning the adjust-
ing screw in will lower the pressure; turning it out will raise the
pressure. If after several hours of operation the temperature is
not as desired, readjust the pressure adjusting screw slightly.
Once the desired setting is reached, make sure the lock nut is
tightened. The valve will now regulate in response to load
variation to maintain constant temperature.
Installation
All regulators are packed for maximum protection. Unpack
carefully. Check the carton to make sure all flanges and other
items are unpacked. Save the enclosed instructions for the
installer and eventual user.
Do not remove the protective coverings from the inlet and outlet
of the regulator until the regulator is ready to be installed.
Protect the inside of the regulator from moisture, dirt and chips
before and during installation. When welded or brazed flange
connections are used, all slag, scale and loose particles should
be removed from the flange interior before the regulator is
installed between the flanges. It is advisable to install a close-
coupled companion strainer (RSF) at the inlet of the regulator
to help protect it from any foreign material in the system.
The A4 series of regulators will give optimum performance if
mounted in a horizontal line in a vertical position with the
manual opening stem on bottom. Where other positions are
desired, the factory should be consulted: please give applica-
tion and piping details. To function properly, the regulator must
be installed with the arrow on the valve body pointing in the
direction of the fluid flow. Backward flow through the regulator
is uncontrolled and will vary with valve model and the reverse
pressure drop encountered.
Tighten the flange bolts and nuts evenly to provide proper
seating of the flange gasket and to avoid damage to gaskets or
flanges (See Flange Bolt Torque Table). Avoid using the
regulator flange bolts to stretch or align pipe. Even the heavy
body of an A4 can be distorted, causing the precision parts to
bind.
The regulator should be installed in a location where it is easily
accessible for adjustment and maintenance. The location
should be such that the regulator cannot be easily damaged by
material handling equipment. When it is necessary to insulate
the regulator (and companion strainer), the insulation should
be installed to provide access to the regulator (and companion
strainer) for adjustment and maintenance. Do not insulate the
solenoid coil and coil housing. Proper indicating gauges
should be installed to be easily visible to the operating engineer
for system checking and adjusting purposes.
Maintenance and Service
General Procedure:
Dirt in the system is the greatest single cause of regulator
malfunction. All screens or filters should be cleaned or re-
placed when they become dirty. At start-up, it is especially
important that these items are cleaned or changed frequently.
When the RSF close-coupled companion strainer is used,
maintain according to instruction in Bulletin 00-10. Moisture in
halocarbon systems in particular, can cause corrosion or form
ice, causing the piston to freeze in position. Filter-dryers
should be used and maintained for halocarbon systems.
Before deciding to disassemble a regulator for servicing, the
following investigations should be made:
Check the manual opening stem; it should be turned in for
automatic operation.
Check the cam and cam follower alignment. There should be
clearance between the cam and follower on both sides.
Check for smooth actuating stem movement with cam rotation.
The packing nut should be tight enough to prevent moisture
penetration and loose enough to permit smooth stem stroking.
Check regulator pressure range; if wrong, range spring must
be replaced.
Check other system components for proper operation.
Check hand valves in the system to make sure they are open
or closed as required and the system is receiving liquid or gas,
as the case may be.
Before disassembly of regulator, make certain that all refriger-
ant has been removed (pumped out) from the regulator and its
companion strainer where one is used.
Read Safety Bulletin RSBCV.