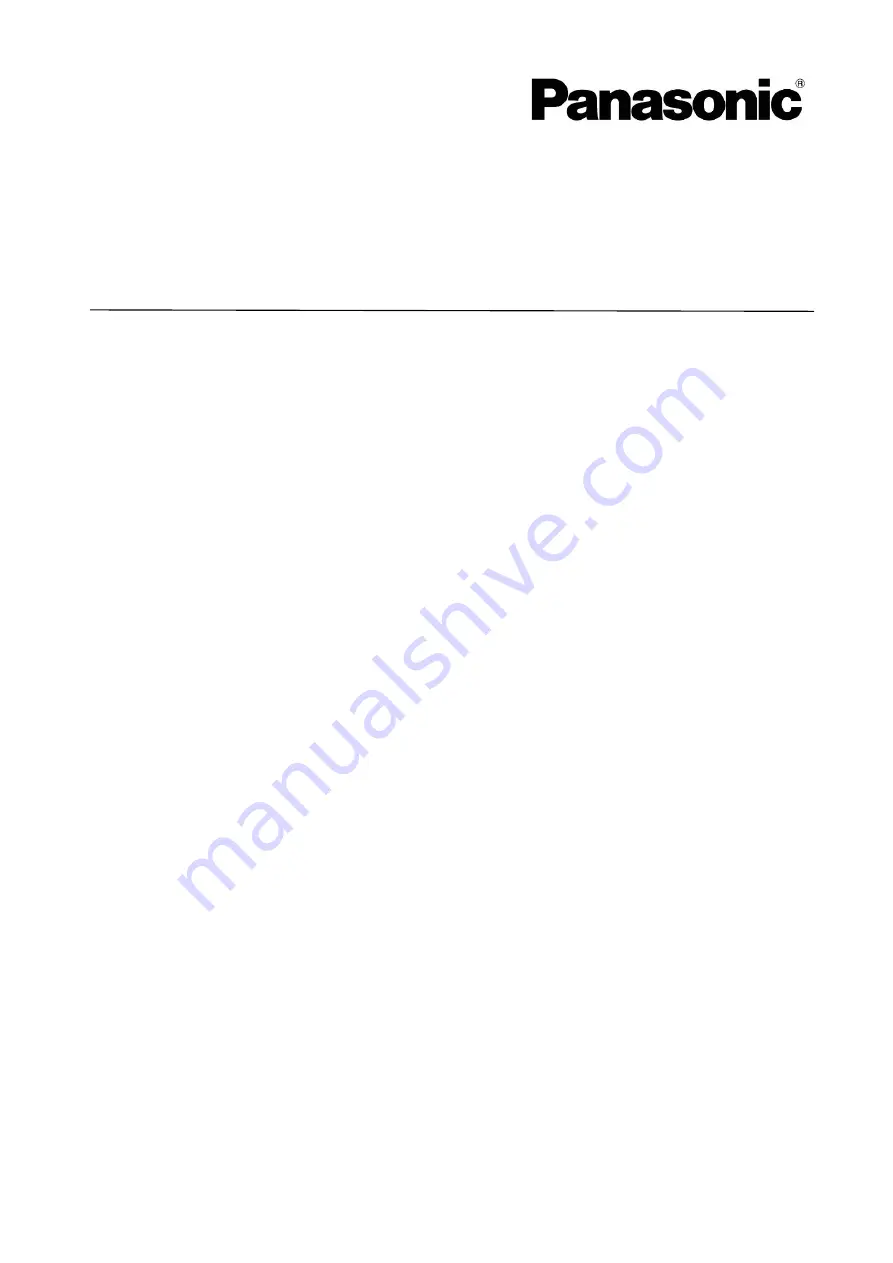
● Thank you for your purchase of Panasonic welding power source.
●Before operating this product, please read the instructions carefully and save this
manual
for future use.First of all, please read “Safety precautions” or “Safety manual”.
● SPEC. No.
:
YC-400TX3HJF
Panasonic Welding Systems (Tangshan) Co., Ltd.
Model No.
YC-400TX
Operating Instructions
TSM50310-01
IGBT controlled DC TIG Arc Welding Power
Source
Содержание YC-400TX
Страница 25: ...22 14 Circuit diagram ...
Страница 28: ...25 16 Outline drawing ...