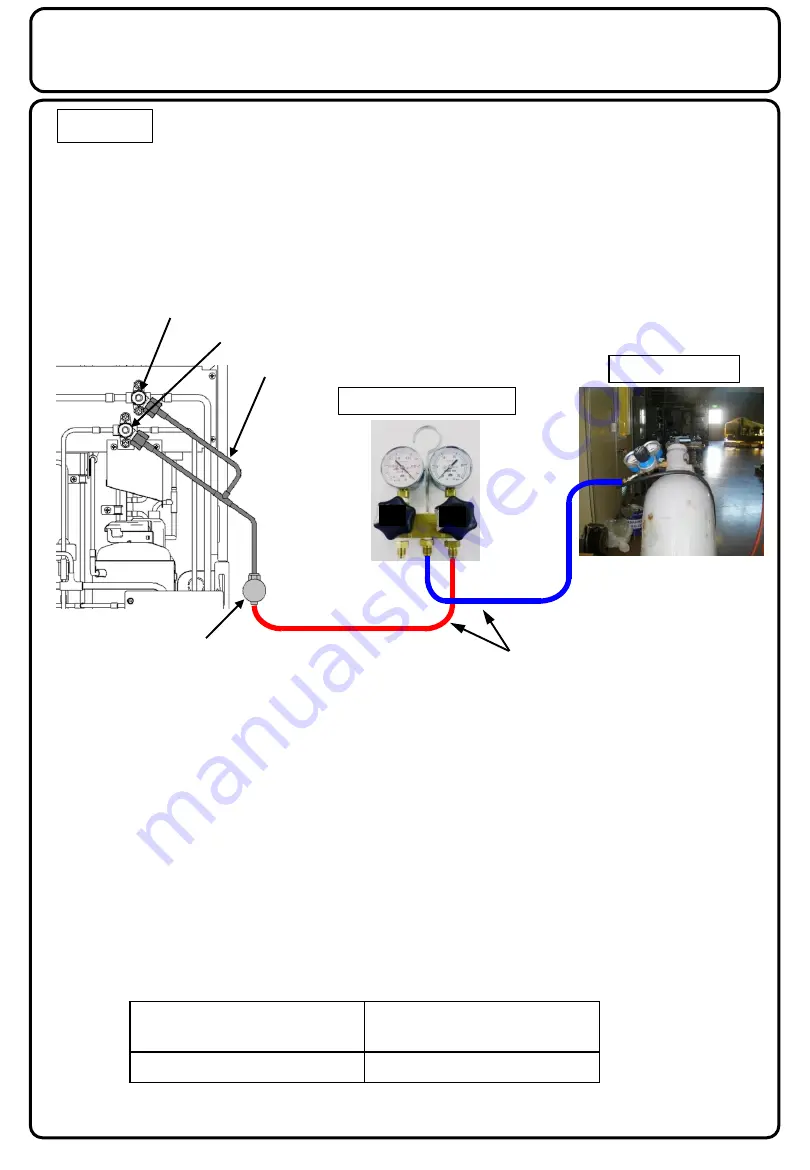
9
Airtight Test Procedure
(Execute this test after competing piping work and airtight test but before starting
heat insulation work)
1. Piping connection
1) Connect the joint valve of the service piping (SPK-TU125) and the manifold gauge set
exclusively for CO
2
refrigerant by using a CO
2
charge hose or 1/4" pipe.
2) Connect a nitrogen cylinder and the manifold gauge set by using a CO
2
charge hose or
1/4" pipe.
2. Airtight test
1) Set the evacuation mode in accordance with " Evacuation Mode".
2) When carrying out an airtight test of interconnecting piping and load-side equipment
(such as showcase and unit cooler), set up the service valves with the front seat.
After replacing components of the refrigeration unit and when performing an airtight test of
the refrigeration unit, use the Mid-position. (The access ports are open.)
However, at this time, avoid applying the high-pressure side airtight test pressure to
the low-pressure side.
Note:
Airtight test of the refrigeration unit was completed at the time of factory
shipment. Pressure testing should only be carried out by personal / companies
who have necessary certification. Consider carefully local regulations and
EN378.
Design pressure in Factory
Caution
Make sure to close the vacuum valve of CO
2
manifold gauge set.
Consider special local regulations and consider Installation of all
equipment have to be in accordance to pressure directive 2014/68/EU
and European norm EN378.
Service piping
Joint valve
Nitrogen cylinder
Charging
valve
CO
2
charge hose or 1/4" pipe
CO
2
manifold gauge set
Low side
gauge
High side
gauge
High pressure part
Low and intermediate
pressure parts
12MPa
8MPa
Low pressure service valve
High pressure service valve
Содержание OCU-CR200VF5
Страница 37: ...37 Exploded View ...
Страница 38: ...38 Exploded View ...