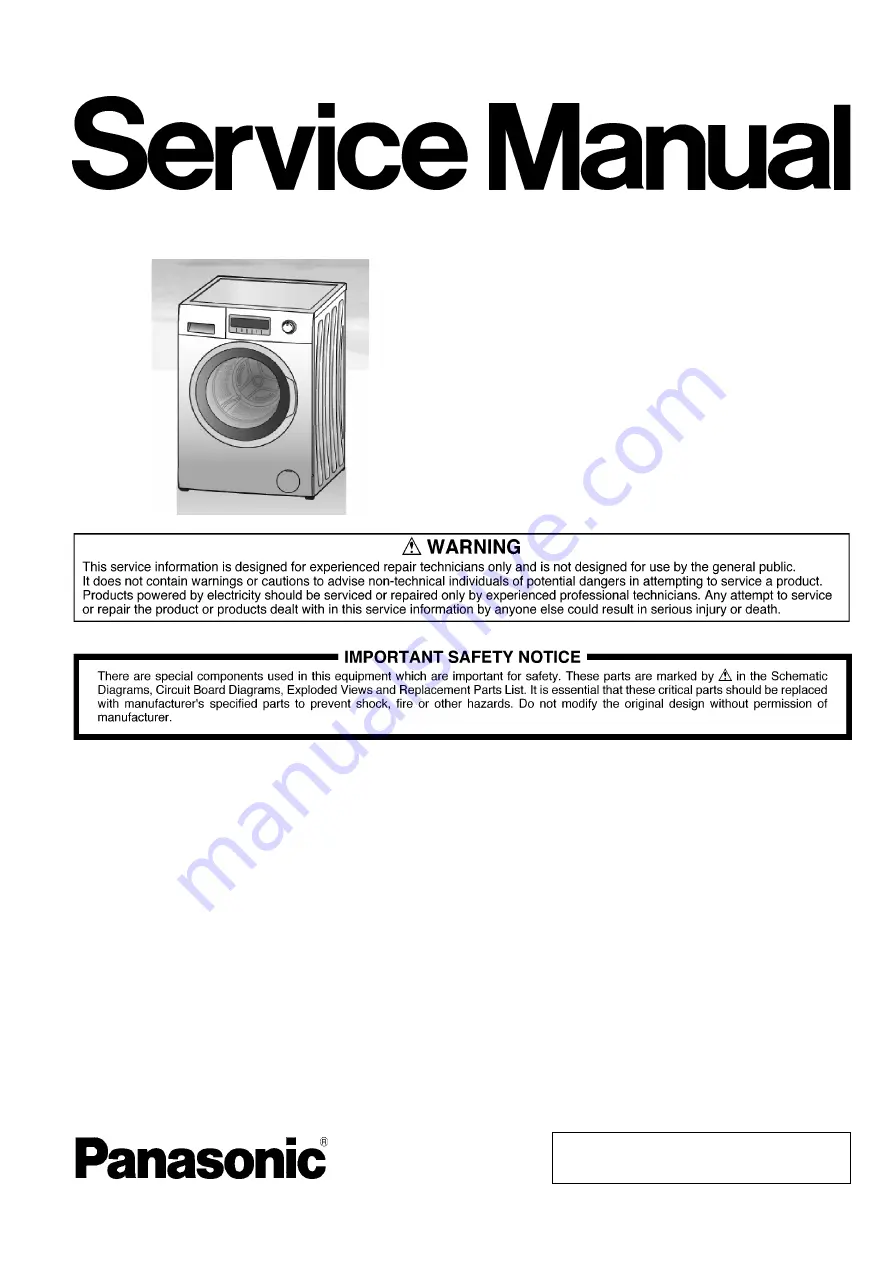
© Panasonic Corporation 2015 Unauthorized copy-
ing and distribution is a violation of law.
Order No. VES1504006CE
Drum Type Washing Machine
Model No.
NA-147VC6WPL
Model No.
NA-147VC6WGN
Model No.
NA-147VC6WNR
Model No.
NA-147VC6WFR
Product Color : White
Destination : France, Poland, Estonia, Latvia, Lithua-
nia, Holland, Belgium, Czech, Hungary,
Romania, Slovakia, Croatia, Serbia, Slo-
venia, Bosnia-Herzegovina, Sweden,
Norway, Finland, Denmark
TABLE OF CONTENTS
PAGE
PAGE
1 Safety Precautions
-----------------------------------------------
2
2 Specifications
-----------------------------------------------------
3
3 Location of Controls and Components
-------------------
5
4 Installation Instructions
----------------------------------------
6
5 Operating Instructions
------------------------------------------
8
6 Test Mode
----------------------------------------------------------
10
7 Service Mode
-----------------------------------------------------
12
8 Troubleshooting Guide
----------------------------------------
13
9 Torque Values
----------------------------------------------------
14
10 Disassembly and Assembly Instructions
---------------
15
11 Component Specifications
-----------------------------------
26
12 Wiring Connection Diagram
---------------------------------
32
13 Exploded View and Replacement Parts List
-----------
34
Содержание NA-147VC6WPL
Страница 2: ...2 ...
Страница 4: ...4 2 3 Dimension in millimetres NA 147VC6 ...
Страница 5: ...5 3 Location of Controls and Components ...
Страница 9: ...9 5 2 Program Details ...