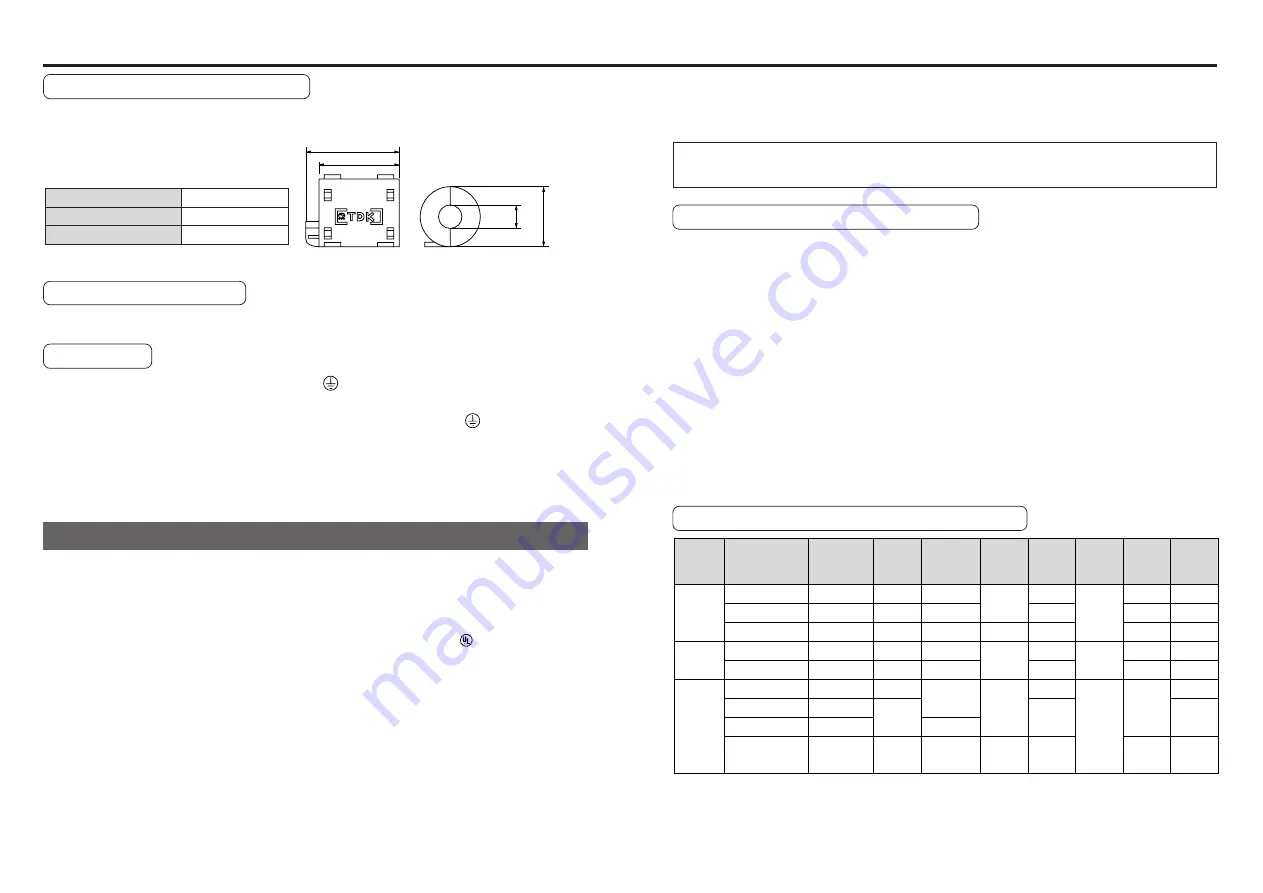
– B45 –
– B44 –
<Caution>
Fix the signal line noise filter in place to eliminate excessive stress to the cables.
Ground-Fault Breaker
Install a type B ground fault breaker (RCD) at primary side of the power supply.
Grounding
(1) Connect the protective earth terminal ( ) of the driver and the protective earth
terminal (PE) of the control box without fail to prevent electrical shocks.
(2) Do not make a joint connection to the protective earth terminals ( ). 2 terminals are
provided for protective earth.
<Note>
For driver and applicable peripheral equipments, refer to P.B14 "Driver and List of Ap-
plicable Peripheral Equipments" .
Conformity to UL Standards
Observe the following conditions of (1) and (2) to make the system conform to UL508C
(File No. E164620).
(1) Use the driver in an environment of Pollution Degree 2 or 1 prescribed in IEC60664-
1. (e.g. Install in the control box with IP54 enclosure.)
(2) Install a circuit breaker or fuse which are UL recognized (Listed marked) between
the power supply and the noise filter without fail.
For the rated current of the circuit breaker or fuse, refer to P.32, "Driver and List of
Applicable Peripheral Equipments" of Preparation.
Use a copper cable with temperature rating of 60˚C or higher.
Tightening torque of more than the max. values (M4:1.2N
•
m, M5: 2.0N
•
m) may break
the terminal block.
(3) Over-load protection level
Over-load protective function will be activated when the effective current exceeds 115%
or more than the rated current based on the time characteristics. Confirm that the effec-
tive current of the driver does not exceed the rated current. Set up the peak permissible
current with Pr5E (Setup of 1st torque limit) and Pr5F (Setup 2nd torque limit).
7. Conformity to EC Directives and UL Standards
Noise Filter for Signal Lines *
Install noise filters for signal lines to all cables (power cable, motor cable, encoder cable
and interface cable)
* In case of D-frame, install 3 noise
filters at power line.
39
±
1
34
±
1
30
±
1
13
±
1
Mass: 62.8g
Option part No.
Manufacturer's part No.
Manufacturer
DV0P1460
ZCAT3035-1330
TDK Corp.
8. Built-in Holding Brake
In the applications where the motor drives the vertical axis, this brake would be used to
hold and prevent the work (moving load) from falling by gravity while the power to the
servo is shut off.
Use this built-in brake for "Holding" purpose only, that is to hold the stalling status.
Never use this for "Brake" purpose to stop the load in motion.
Output Timing of BRK-OFF Signal
• For the brake release timing at power-on, or braking timing at Servo-OFF/Servo-Alarm
while the motor is in motion, refer to the technical reference. (DV0P4210)
• With the parameter, Pr6B (Setup of mechanical brake action while the motor is in
motion), you can set up a time between when the motor enters to a free-run from
energized status and when BRK-OFF signal turns off (brake will be engaged), when
the Servo-OFF or alarm occurs while the motor is in motion.
<Notes>
1. The lining sound of the brake (chattering and etc.) might be generated while running
the motor with built-in brake, however this does not affect any functionality.
2. Magnetic flux might be generated through the motor shaft while the brake coil is ener-
gized (brake is open). Pay an extra attention when magnetic sensors are used nearby
the motor.
Specifications of Built-in Holding Brake
4.9
44.1
147
44.1
147
196
490
2156
39.2
137
196
137
196
392
1470
DC2V
or more
DC1V
or more
DC2V
or more
0.25
0.30
0.35
0.29
0.41
0.74
0.81
0.90
10 or less
20 or less
15 or less
15 (100)
or less
50 (130)
or less
MSMD
MAMA
MQMA
MSMA
50W, 100W
200W, 400W
750W
100W
200W, 400W
1.0kW
1.5kW, 2.0kW
3.0kW
4.0kW, 5.0kW
0.29 or more
1.27 or more
2.45 or more
0.29 or more
1.27 or more
4.9 or more
7.8 or more
11.8 or more
16.1 or more
0.002
0.018
0.075
0.03
0.09
0.25
0.33
1.35
35 or less
50 or less
70 or less
50 or less
60 or less
50 or less
80 or less
110 or less
Permissible
total work
x 10
3
J
Permissible
work (J) per
one braking
Releasing
voltage
Exciting
current
DC A
(at cool-off)
Releasing
time
ms*
Engaging
time
ms
Rotor
inertia
x 10
–4
kg
•
m
2
Static
friction
torque
N
•
m
Motor
output
Motor
series
(Continues to next page)