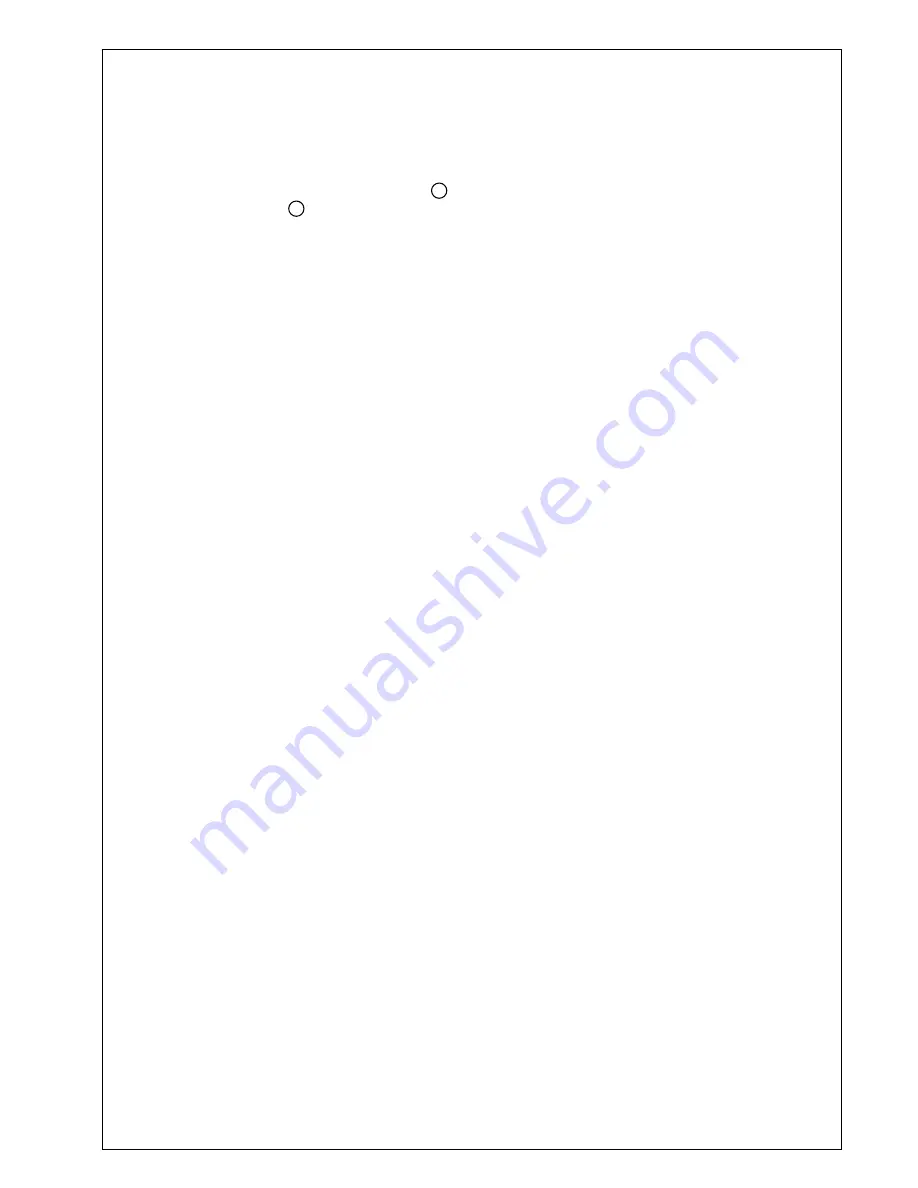
No.SX-DSV01676
- 45 -
R2
Motor Company, Matsushita Electric Industrial Co., Ltd.
12-4 Conformity to UL Standards
Observe the following conditions of 1) and 2)
to make the system conform to UL508C (File No. E164620).
1) Use the servo drive in environment of Pollution Degree 2 or 1 prescribed in IEC-60664-1.
(E.g. Install in the control box with IP54).
2)
Connect a UL recognized (UL Listed, marked) circuit breaker or UL recognized fuse
(UL Listed, marked) between the power and the noise filter without fail.
For rated current of the circuit breaker/fuse, refer to section 12-3, List of peripheral Equipments.
Use a cable of copper conductor with temperature rating of 60degrees or more.
Terminal block might be damaged when a tightening torque of screw exceeds the max. value
(M4: 1.2N·m, M5: 2.0N·m).
3) Overload protection level
Overload protection function will be activated according to the time characteristics, when effective
current exceeds 115% or more of the rated current. Confirm that the effective current of the drive has
not exceeded the rated current. Set up the peak permissible current with Pr.5E (1
st
torque limit) and
Pr.5F (2
nd
torque limit).
13. Compliance with SEMI F47 standard
- The control power supply of AC200V type servo drive is applicable to SEMI F47 voltage sag immunity
standard.
- This function is useful when it is used for semiconductor manufacturing equipment.
(Note)
(1) This function is not applicable to a AC100V single-phase type servo drive.
(2) When momentary power failure occurs in main power, torque may fall for a moment.
(3) Make sure to mount the servo drive on the actual equipment, and validate its compliance with the
SEMI F47 standard.
UL
UL
Phone: 800.894.0412 - Fax: 888.723.4773 - Web: www.clrwtr.com - Email: [email protected]