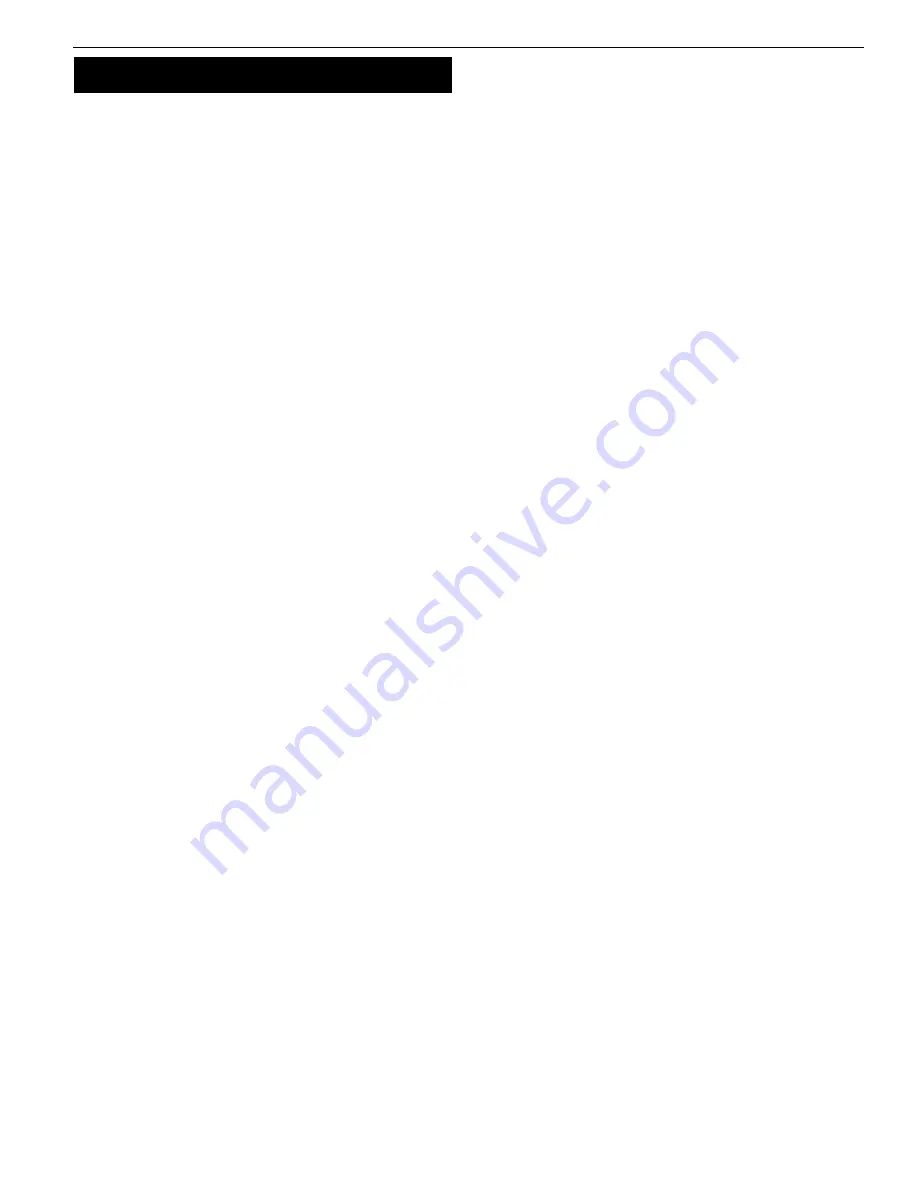
5
Palmgren Operating Manual & Parts List
9683311
OPERATION (CONTINUED)
OIL LEVEL
Refer to Figure 10.
•
The gear box relies on an oil bath to lubricate the sliding surfaces
and transfer heat. The vent bolt (Ref. No. 113) is vented to release
pressure created by the developed heat. Insufficient lubrication
will cause the gears to heat up and wear at an accelerated rate. If
the gear box is overfilled, hot oil will escape through the vent
hole. The gear box is designed to take 10 ounces of 70-95 weight
industrial gear oil.
•
The oil level should remain constant. If the level changes, a de-
fective gasket or seal should be looked for and replaced.
•
If the gear box is worked on, the oil should be replaced to avoid
contamination.
•
Always add fresh oil and replace the oil seasonally, to guard
against breakdown.
•
The seal between the gearbox and the cover plate is a gasket
(Ref. No. 115N). If cover plate is removed, the surface should be
cleaned and a new gasket should be applied.
•
After the first fifty hours of use, the gear box should be drained
and refilled with industrial gear oil.
BLADE GUIDES
Band saw blade has to be twisted relative to the plane in which it
rotates. Blade must be properly positioned relative to the workbed.
Blade guides hold the cutting portion of the blade in a plane which
is perpendicular to both the workbed and the stationary vise and
keeps the blade in line with its natural path around the blade
wheels.
Inner guide bearings on the left and right guide assemblies keep
the blade in line with the blade wheels. Outer guide bearings keep
the blade against the inner bearings.
Entire guide assembly is positioned at the factory to produce the
proper twist and should not need adjustment, however, the posi-
tion of blade guides should be checked often.
NOTE:
Since the blade position is related to both bed and the vise
jaws, the relative position of the jaw to the bed is important. When
assembled, the stationary jaw must be perpendicular to the surface
of the workbed.
CHECKING BLADE GUIDES
Refer to Figure 10.
1. Check that the blade teeth are perpendicular to the machined
surface of the base.
2. Spread the blade guides as far apart as possible.
3. Check that vise jaws are parallel and set for 90° cutoff.
4. Position the vise jaws to have the maximum separation that will
not interfere with the blade guides.
5. With the head in horizontal position, use a square against face
of rear vise jaw and check that jaw is 90° to the side of blade.
6. Check that the blade is in line with tracking and drive wheels
(Ref. Nos. 175 and 124).
7. Raise the head.
8. Look straight on at the cutting edge of the blade.
9. Make sure that the blade sides are parallel to the sides of the
bearings.
10. Make sure the bearings (Ref. No. 133) touch the blades and can
still be rotated by hand.
ADJUSTING GUIDE BEARINGS
Refer to Figure 10.
If the blade is not perpendicular to the bed or not in line with the
blade wheels, adjustment is necessary.
NOTE:
There should be .000-.001” clearance between the blade and
the guide bearings.
The guide bearings are adjusted using an eccentric location sys-
tem. The inner guide bearings are fixed and cannot be adjusted.
The outer guide bearings are mounted to eccentric shafts (Ref. No.
136) and can be adjusted.
1. Loosen hex nuts (Ref. No. 137) with a wrench. Rotate the eccen-
tric shaft to locate bearings in desired positions.
2. Maintain eccentric shaft position and tighten hex nuts.
CHECKING THRUST BEARINGS
Refer to Figure 10.
The thrust bearings (Ref. No. 133) should be .003-.005” (average
thickness of a piece of paper) away from back of blade.
The thrust bearings are adjusted by moving the guide bracket.
ADJUSTING GUIDE BRACKETS
Refer to Figure 10.
If the bearings are positioned properly and the blade is not square,
one or both blade guide brackets (Ref. Nos. 163 and 132) must be
adjusted.
1. Loosen the socket head bolts (Ref. No. 161).
2. Adjust the bracket to the correct position.
3. Tighten the socket head bolts.
4. Check the guide bearings. Repositioning the blade guide
bracket can alter the previous adjustments. Readjust if necessary.
BLADE SELECTION
Using the proper blade is important for setting up the correct cut-
ting conditions. Blades are made differently depending on the spe-
cific application intended for the blade. Some simple rules can still
be applied to almost all blades.
•
Always remember to have at least three teeth in contact with
the work during a cut. When three teeth are in contact, the
blade cannot straddle the work. This prevents a tooth that en-
ters the cut from encountering more material than it can re-
move.
•
“Shocking” occurs when blade teeth contact too much material.
This can strip the teeth from the blade. When cutting harder
materials, the suggested minimum number of teeth in contact
is six because “shocking” on harder materials has a more detri-
mental effect on the blade. Optimum number of teeth in con-
tact with workpiece distributes blade forces among more teeth
to increase cutting efficiency and reduces blade wear.
•
Optimum range is from 6 – 12 teeth in contact for soft materi-
als, up to 12 – 24 teeth in contact for harder materials.
•
Always have maximum number of teeth in contact with work to
prevent gullets of teeth from being clogged.
•
When choosing a blade, overall size of the work is not as
important as the thickness average. Thickness average is the
average width of material which blade will contact during
each cut. Figure 8, page 8 describes how thickness average
should be calculated.