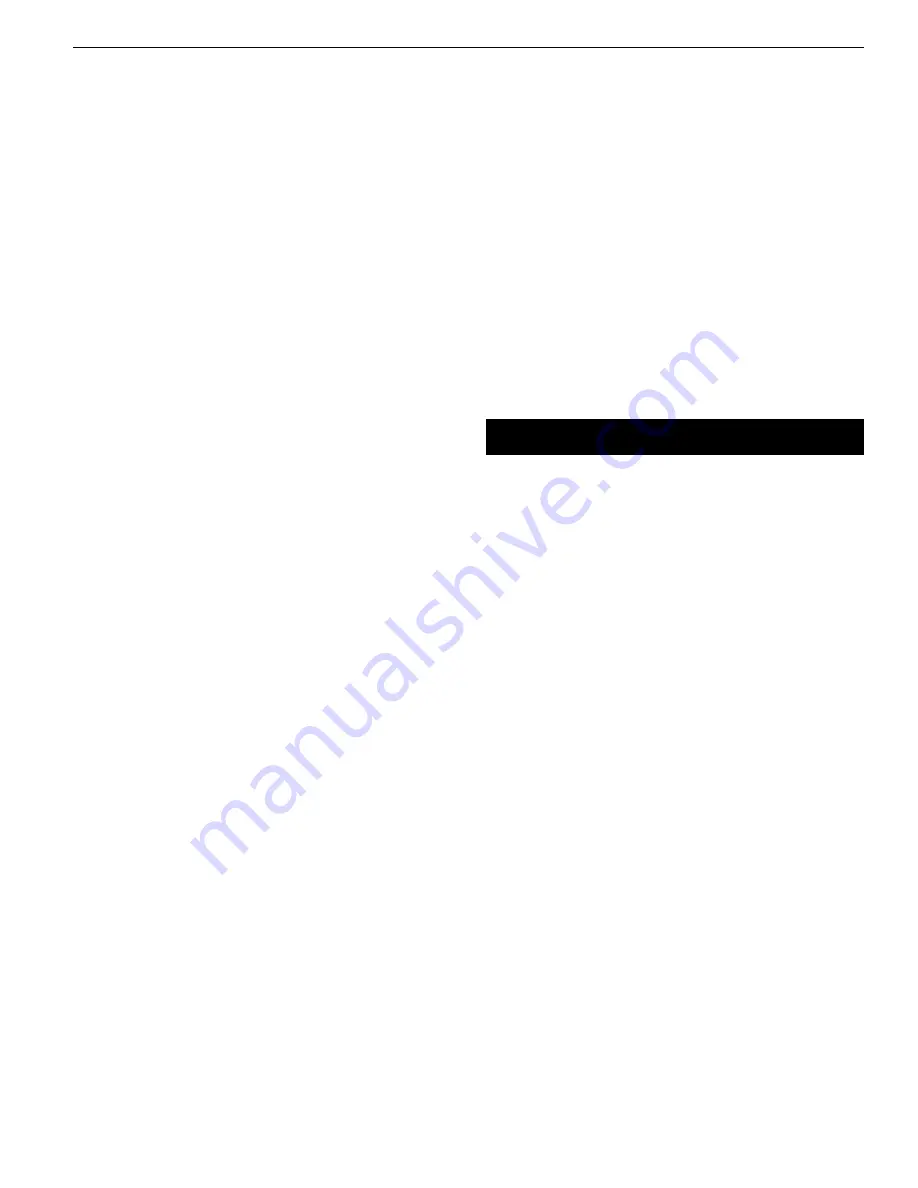
3
SAFETY RULES (CONTINUED)
BE PREPARED FOR JOB
•
Wear proper apparel. Do not wear loose clothing, gloves, neck-
ties, rings, bracelets or other jewelry which may get caught in
moving parts of machine.
•
Wear protective hair covering to contain long hair.
•
Wear safety shoes with non-slip soles.
•
Wear safety glasses complying with United States ANSI Z87.1.
Everyday glasses have only impact resistant lenses. They are
NOT safety glasses.
•
Wear face mask or dust mask if operation is dusty.
•
Be alert and think clearly. Never operate power tools when
tired, intoxicated or when taking medications that cause
drowsiness.
PREPARE WORK AREA FOR JOB
•
Keep work area clean. Cluttered work areas invite accidents.
•
Do not use power tools in dangerous environments. Do not use
power tools in damp or wet locations. Do not expose power
tools to rain.
•
Work area should be properly lighted.
•
Proper electrical receptacle should be available for tool. Three-
prong plug should be plugged directly into properly grounded,
three-prong receptacle.
•
Extension cords should have a grounding prong and the three
wires of the extension cord should be of the correct gauge.
•
Keep visitors at a safe distance from work area.
•
Keep children out of workplace. Make workshop childproof. Use
padlocks or master switches to prevent any unintentional use
of power tools.
TOOL SHOULD BE MAINTAINED
1. Always unplug tool prior to inspection.
2. Consult manual for specific maintaining and adjusting
procedures.
3. Keep tool lubricated and clean for safest operation.
4. Remove adjusting tools. Form habit of checking to see
that adjusting tools are removed before switching
machine on.
5. Keep all parts in working order. Check to determine that
the guard or other parts will operate properly and per-
form their intended function.
6. Check for damaged parts. Check for alignment of mov-
ing parts, binding, breakage, and mounting or any other
condition that may affect a tool’s operation.
7. A guard or other damaged part should be properly
repaired or replaced. Do not perform makeshift repairs.
(Use parts list provided to order replacement parts.)
KNOW HOW TO USE TOOL
•
Use right tool for job. Do not force tool or attachment to do a
job for which it was not designed.
•
Disconnect tool when changing drill bit or cutter.
•
Avoid accidental start-up. Make sure that the tool is in the OFF
position before plugging in.
•
Do not force a tool. It will work most efficiently at the rate for
which it was designed.
•
Keep hands away from moving parts and cutting surfaces.
•
Never leave tool running unattended. Turn the power off and
do not leave tool until it comes to a complete stop.
•
Do not overreach. Keep proper footing and balance.
•
Never stand on tool. Serious injury could occur if tool is tipped
or if drill bit is unintentionally contacted.
•
Know your tool. Learn the tool’s operation, application
and specific limitations.
•
Use recommended accessories (refer to page 13). Use of
improper accessories may cause risk of injury to persons.
•
Handle workpiece correctly. Protect hands from possible injury.
•
Turn machine off if it jams. Drill bit or cutter jams when it digs
too deeply into workpiece. (Motor force keeps it stuck in the
work.)
•
Clamp workpiece or brace against column to prevent rotation.
•
Feed work into a bit or cutter against the direction of rotation
of bit or cutter.
•
Use recommended speed for mill drill accessory and workpiece
material.
CAUTION:
Think safety! Safety is a combination of operator com-
mon sense and alertness at all times when tool is being used.
A
AS
SS
SE
EM
MB
BL
LY
Y
Refer to Figures 3, 6, 7, 8 and 10.
CAUTION:
Do not attempt assembly if parts are missing. Use this
manual to order replacement parts.
MILL DRILL INSTALLATION
Mill drill must be mounted to a flat level surface. Use shims or
machine mounts if necessary. Do not mount machine in direct sun-
light. Heat caused by sunlight may deform plastic parts on
machine.
If stand is used, be sure to bolt mill drill to stand and level stand to
floor to minimize vibration. Use hex head bolts, hex nuts and level-
ing pads (Figure 10, Ref. Nos. 8, 11 and 12) to align the mill drill.
Tighten all nuts and bolts that may have loosened in shipping.
Secure mill drill base to stand or bench.
ASSEMBLE STAND (OPTIONAL)
Refer to Figure 10.
•
Place both supports (Ref. No. 5) upside down on floor.
•
Attach feet (Ref. No. 9) and plate (Ref. No. 7) to each support
using hex head bolts, washers and hex nuts (Ref. No. 2, 3 and 4).
Finger tighten fasteners at this time.
•
Repeat on other side of supports with feet and plate (Ref. No.
14).
•
Turn unit right side up.
•
Install left and right panels (Ref. Nos. 6 and 13). Gently spread
supports so that tabs on panels fit into slots located on sup-
ports.
•
Secure all fasteners from steps 2 and 3.
•
Place chip pan (Ref. No. 1) on top of supports, locating the bot-
tom rail of the chip pan inside the supports.
•
Secure chip pan to supports using hex head bolts and flat
washers (Ref. Nos. 2 and 3).
MOUNT MILL DRILL TO STAND
Refer to Figure 10.
Place mill drill on stand with mounting holes aligned. Bolt mill drill
base to stand with four hex head bolts and four flat washers (Ref.
Nos. 3 and 10).
Palmgren Operating Manual & Parts List
80161 & 70104