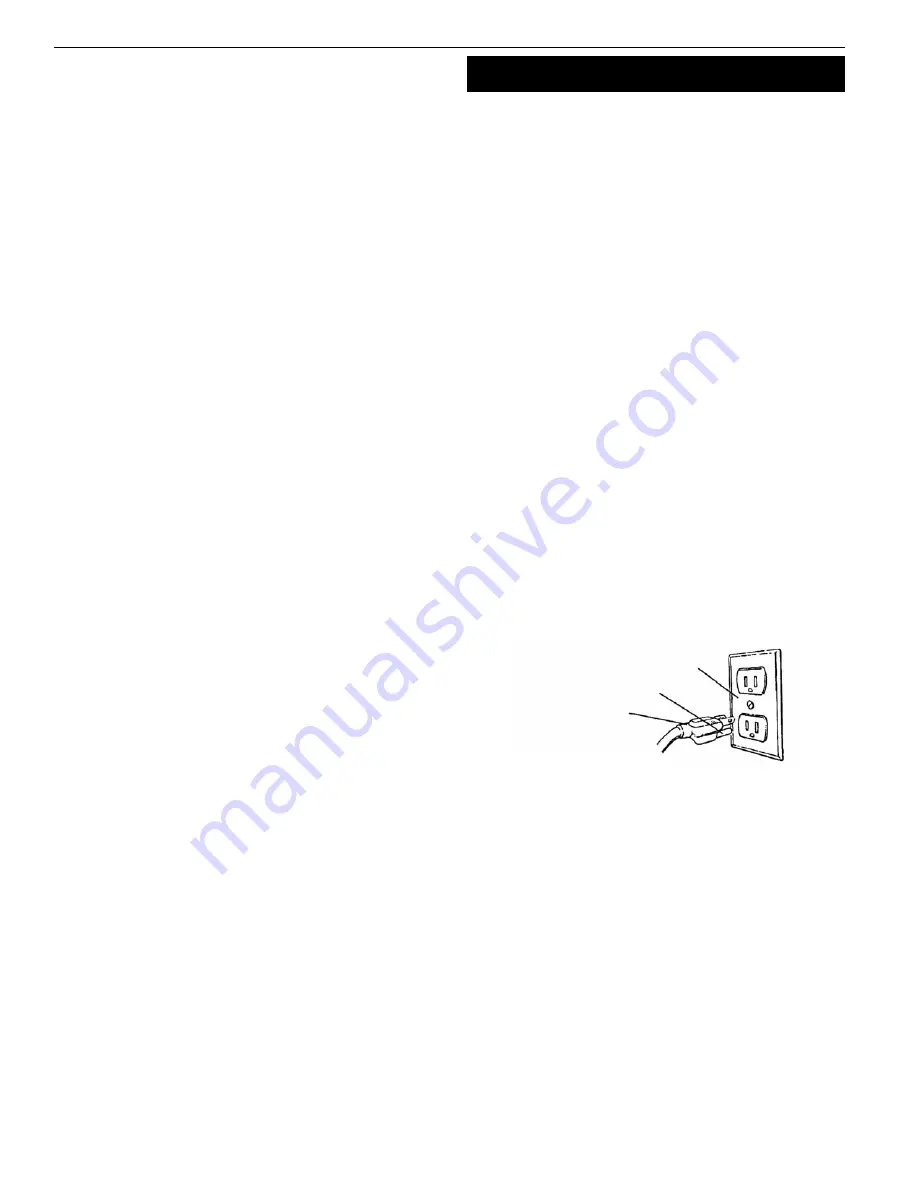
4
MOUNT TABLE (80156)
Refer to Figure 7.
•
Attach crank handle (Ref. No. 22) to shaft of worm gear (Ref. No.
20), rotate worm gear to remove slack, and shoulder crank han-
dle with set screw (Ref. No. 21). Attach crank handle knob (Ref.
No. 23) to handle.
•
Slide table (Ref. No. 13) into hole in table arm. Secure table with
table locking handle (Ref. No. 11).
MOUNT HEAD ASSEMBLY
Refer to Figure 9.
WARNING:
Although compact, the drill press head assembly is
heavy. Two people are required to mount the drill press head
assembly onto the column.
•
Slide drill press head assembly onto top of column.
•
Position head so that it is centered over base.
•
Secure head by tightening the set screws (Ref. No. 36) on the
right side of the head casting.
MOUNT QUILL FEED HANDLE ASSEMBLY
Refer to Figure 8.
•
Place key (Ref. No. 32) into keyway of pinion (Ref. No. 33).
•
Place quill feed handle assembly (Ref. No. 34) over pinion.
•
Secure handle assembly with tap head screw (Ref. No. 36) and
plate (Ref. No. 35).
•
Thread quill feed knob (Ref. No. 37) into quill feed handle
assembly.
INSTALL CENTER PULLEY ASSEMBLY
Refer to Figures 8 and 9.
•
Loosen belt tension knobs (Fig. 8, Ref. No. 38) and use handle
(Fig. 8, Ref. No. 43) to move motor toward front of drill press.
•
Open cover of pulley housing (Fig. 9, Ref. No. 2) and insert cen-
ter pulley assembly (Fig. 8, Ref. No. 8) into the head casting.
•
Choose a speed from Figure 5 or the pulley housing speedchart
and connect spindle pulley to center pulley with front drive
belt (Fig. 8, Ref. Nos. 2, 7 and 8). Connect center pulley to motor
pulley with rear drive belt (Fig. 8, Ref. Nos. 8, 54 and 55).
NOTE: Front drive belt is type 254J4 and rear drive belt is type
290J4.
•
Turn handle (Fig. 8, Ref. No. 43) to move motor toward rear of
drill press and tighten belt tension knob (Fig. 8, Ref. No. 38).
MOUNT DRILL CHUCK AND ARBOR
Refer to Figure 8.
•
Be sure spindle taper, arbor taper and chuck taper are clean
and dry.
•
Use the provided chuck key (Ref. No. 31) to adjust the jaws of
the chuck (Ref. No. 30) until they are recessed inside the drill
chuck body.
•
Place drill chuck on a workbench face down. Arbor (Ref. No. 29)
has a short taper and a long taper. Place short taper into top of
drill chuck and tap with a rubber or wooden mallet.
•
Slide arbor into the spindle (Ref. No. 24) while slowly rotating
drill chuck. Spindle has a rectangular pocket in which the tang
fits into. Once tang is oriented correctly, drill chuck will not
rotate without turning the spindle.
•
Tap the end of drill chuck with a rubber or wooden mallet to
seat it into the spindle.
Hardware (Two M8 x 125 hex head bolts, M8 lock washers, M8 hex
nuts and four M8 flat washers) has been provided for mounting
the drill press to a wood base plate. This is recommended if you
intend to place the drill press on a mobile base. The minimum
recommended size of the wood base plate is
3
⁄
4
x 24 x 24”.
INSTALLATION
Refer to Figures 2, 3 and 4.
MOUNT DRILL PRESS
•
Drill press must be mounted to flat level surface. Use shims or
machine mounts if necessary. Do not mount drill press in direct
sunlight.
•
Be sure to bolt drill press to floor or bench securely to prevent
tipping and minimize vibration.
•
Tighten all nuts and bolts that may have loosened during
shipment.
POWER SOURCE
The motor is designed for operation on the voltage an frequency
specified. Normal loads will be handled safely on voltages not more
than 10% above or below the specified voltage.
Running the unit on voltages which are not within the range may
cause overheating and motor burn out. Heavy loads require that the
voltage at motor terminals be no less than the voltage specified.
GROUNDING INSTRUCTIONS
WARNING:
Improper connection of equipment grounding con-
ductor can result in the risk of electrical shock. Equipment should
be grounded while in use to protect operator from electrical shock.
Check with a qualified electrician if grounding instructions are not
understood or if in doubt as to whether the tool is properly
grounded.
This tool is equipped with an approved 3-conductor cord rated up
to 300V and a 3-prong grounding type plug rated at 115V (See
Figure 2) for your protection against shock hazards.
Grounding plug should be plugged directly into a properly
installed and grounded 3-prong grounding-type receptacle, as
shown (Figure 2).
Do not remove or alter grounding prong in any manner. In the
event of a malfunction or breakdown, grounding provides a path
of least resistance for electrical shock.
WARNING:
Do not permit fingers to touch the terminals of plug
when installing or removing from outlet.
Plug must be plugged into matching outlet that is properly
installed and grounded in accordance with all local codes and
ordinances. Do not modify plug provided. If it will not fit in outlet,
have proper outlet installed by a qualified electrician.
Inspect tool cords periodically, and if damaged, have repaired by
an authorized service facility.
Green (or green and yellow) conductor in cord is the grounding
wire. If repair or replacement of the electric cord or plug is neces-
sary, do not connect the green (or green and yellow) wire to a live
terminal.
Where a 2-prong wall receptacle is encountered, it must be
replaced with a properly grounded 3-prong receptacle installed in
accordance with National Electric Code and local codes and ordi-
nances.
Palmgren Operating Manual & Parts List
80155 and 80156
Figure 2 – 3-Prong Receptacle
Properly Grounded Outlet
Grounding Prong
3-Prong Plug