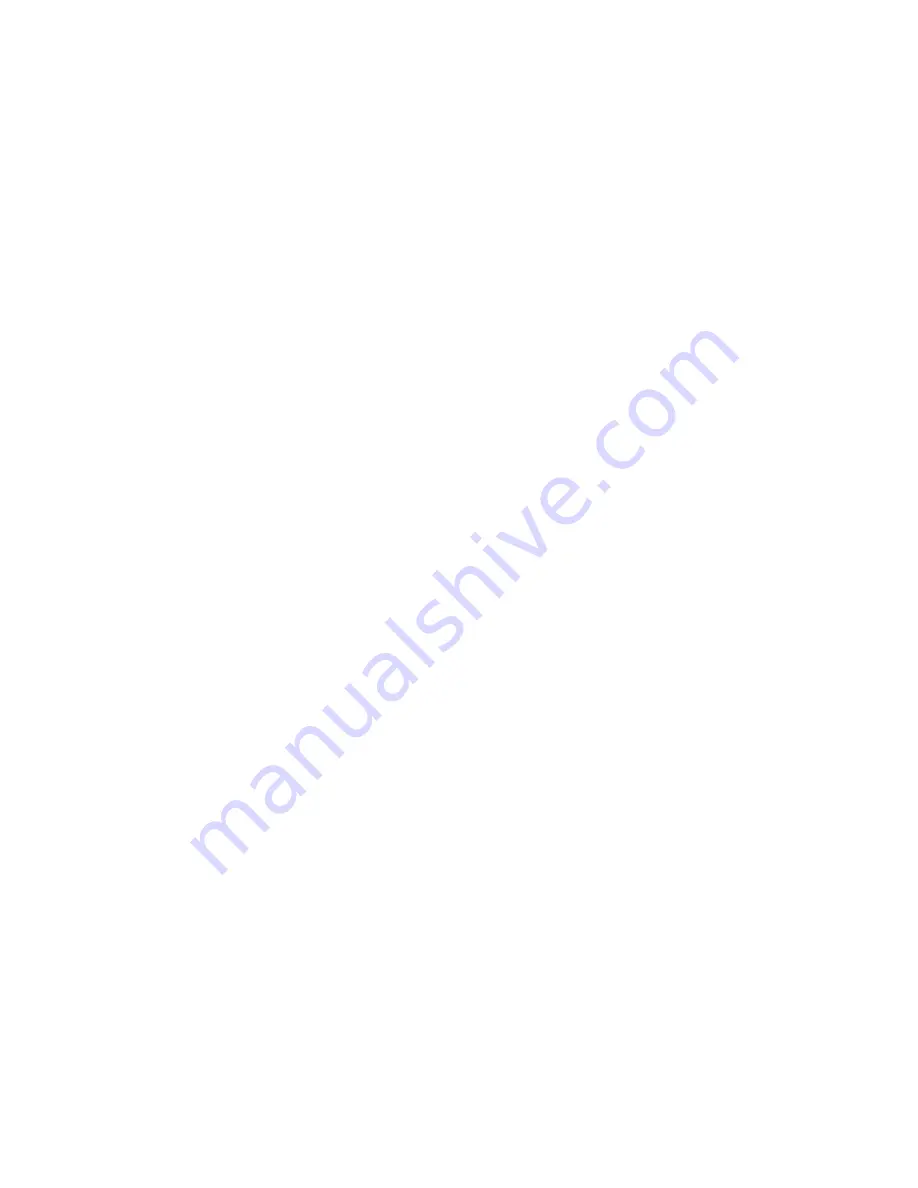
TROUBLESHOOTING OPERATING CONDITIONS:
Below are listed a few operating conditions that may cause repeated stalling of your
brush cutter, and suggestions on how to correct them.
GRASS TOO LONG OR THICK
: If cutting heavy vegetation, you may need to slow travel
speed or make smaller passes (less than full cut) to prevent overloading and stalling the unit.
Although the brush cutter is not designed for mowing grass, by monitoring blade sharpness
and travel speed this can be accomplished.
BRUSH TOO BIG IN DIAMETER:
The brush cutter is NOT designed to cut trees larger than 7"
(178mm) in diameter. If brush is smaller than 7" (178mm) in diameter and the cutter is stalling,
check sharpness of the blades (see "Maintenance") and cut using the procedure described
earlier in this section for "CUTTING LARGE BRUSH AND SMALL TREES".
BRUSH TOO THICK OR HEAVY:
If cutting heavy or thick brush, you may need to slow travel
speed or make smaller passes (less than full cut), to prevent overloading. If the blades seem to
be unable to handle the volume of brush, slow down the travel speed until the unit reaches full
speed before proceeding.
SCALPING THE GROUND or BOTTOMING OUT:
Be aware of changes in the terrain. Stay
alert for drop-off’s and holes. Check the terrain and the deck position before restarting and
continuing cutting.
STRIKING FOREIGN OBJECTS:
Stay alert for rocks, fencing, abandoned wells, septic tanks
or other foreign objects. If the brush cutter comes into contact with a foreign object, stop the
unit, shut off the engine and disconnect the hydraulic couplers from the skid steer. Inspect
the unit and repair any damage before restarting and continuing cutting. (Never try to weld
or straighten damaged blades.) Inspect the work area for any other items, and if they are too
large to be removed from the area, they should be flagged clearly.
NOTE: GS SERIES (30-45 GPM) CUTTERS ONLY: When blades are bent or damaged
they will become wedged between the blade carrier plates. This will cause excessive
vibration and the blades must be replaced before proceeding (see “Maintenance”).
OPERATING INSTRUCTIONS
12158 12-20-17-2
18
75728
Содержание Bradco Extreme Duty Ground Shark Series
Страница 4: ...2 75728...
Страница 6: ...THIS PAGE IS INTENTIONALLY BLANK 4 75728...
Страница 34: ...THIS PAGE IS INTENTIONALLY BLANK 32 75728...