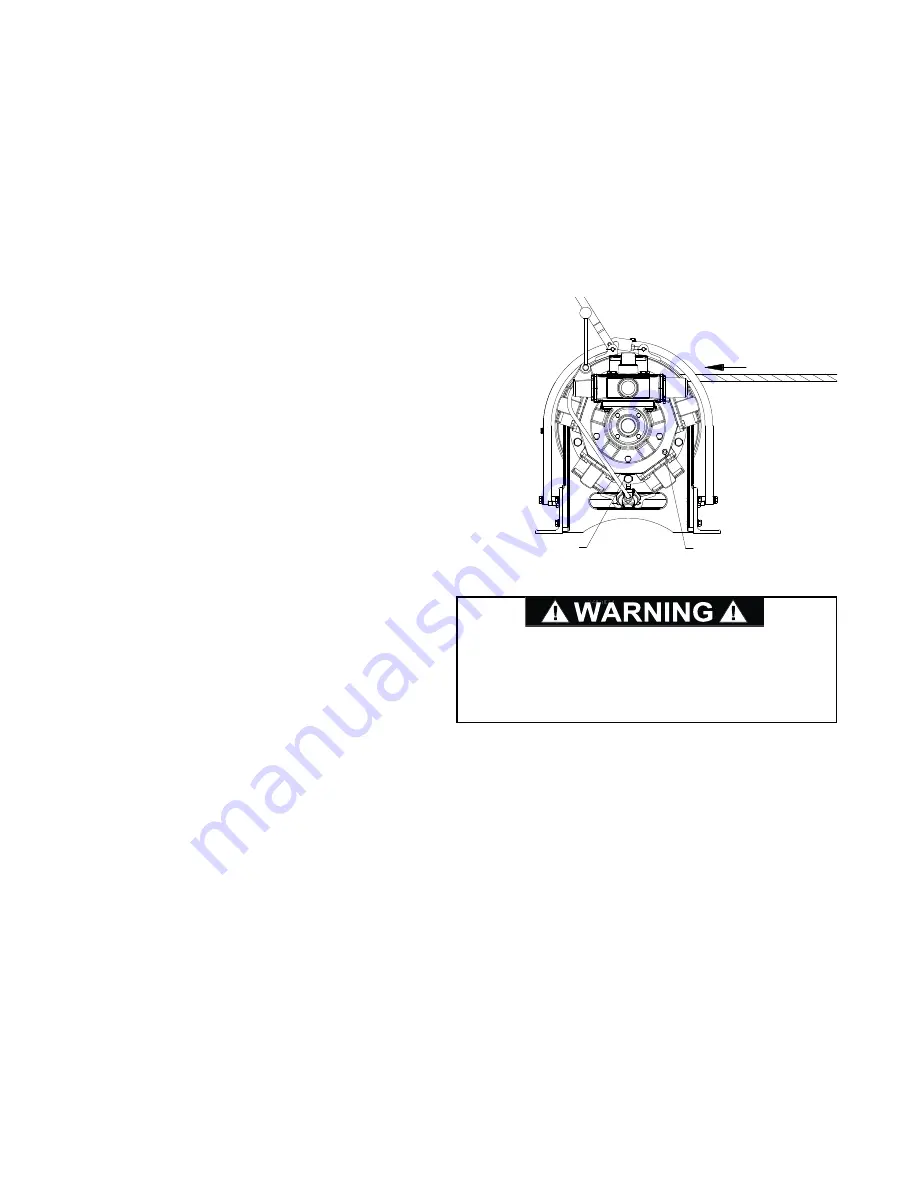
12
A regular program of preventive maintenance for your
planetary hoist is required to minimize the need for emer-
gency servicing and promote safe, reliable hoist opera-
tion.
The user of Braden hoist products is responsible for hoist
inspection, testing, operator training and maintenance
noted below with frequency dependent upon the severity
of the hoist duty cycle and the thoroughness of the pre-
ventive maintenance program.
Field experience, supported by engineering tests, indi-
cate the three service procedures listed below are the
most critical to safe, reliable hoist operation and MUST
be observed.
•
Regular Gear Oil Changes (see notes 1 and 2 below
and page 13 of this manual)
•
Use of Proper Gear Oil – recommended type for pre-
vailing ambient temperatures and additives (see page
14 and 15)
•
Periodic Disassembly and Inspection of All Wear
Components – in compliance with ANSI specification
B30.5c, 1987 and API RP 2D.
1. The air motor case oil should be drained and refilled
with recommended oil after 25 hours initial running
and every 200 hours thereafter or sooner if neces-
sary; for example, if the oil is contaminated by water
in the air line.
2. The winch gear oil should be changed after the first
100 hours of operation or 30 days. The regular gear
oil change intervals may be adopted after the first oil
change.
3. The proper oil level in the motor casing (at level plug
on page 15), must be maintained. The frequency of
replenishment will depend on the application and
usage.
4. The air line filter should be drained at least once each
work shift and examined for clogging of the element.
Moisture in the air line that enters the motor will cause
accelerated motor wear. Moisture traps and air
receivers in the air system will help minimize moisture
in the air reaching the motor.
5. The air line lubricator should be replenished as
required and set to give 6 to 8 drops per minute. If
operation is intermittent, double the rate to 12 to 16
drops per minute.
Pre-use Inspection
(each shift the hoist is used): This
inspection must be performed prior to placing the crane
into service and then as necessary during the day for
extended operation.
1. Check for external oil leaks and repair as necessary.
This is extremely important due to the accelerated
wear that can be caused by insufficient lubricat-
ing oil in the hoist.
The winch drum gear oil level
must be maintained between the maximum and mini-
mum levels. The oil level should be visible in the lower
half of the sight glass or level with the oil level plug on
units without a sight glass. Use only recommended
lubricants. See Recommended Lubricants chart in
this manual. The air motor oil level should be at the
level plug.
2. Check the ratchet and pawl mechanism (if so
equipped) for proper operation and for full engage-
ment of the pawl with the ratchet wheel. Repair or
adjust as necessary.
3. Check air plumbing for damage, such as chafed or
deteriorating hoses and repair as necessary.
4. Visually inspect for loose or missing bolts, pins, keep-
ers or cotter pins and replace or tighten as necessary.
5. Inspect the full length of wire rope, rigging and all
sheaves according to the wire rope rigging, and crane
manufacturer’s recommendations.
6. A warm-up procedure is recommended at each start-
up and is mandatory at ambient temperatures below
+40°F (4°C). The hoist should be operated at low
speeds, hoisting and lowering with no load, several
times to circulate lubricant through the planetary gear
sets.
PREVENTIVE MAINTENANCE
Motor
Oil Level
Motor Oil
Drain
HOIST
Failure to use the proper type and viscosity of plane-
tary gear oil may contribute to intermittent brake clutch
slippage which could result in severe personal injury,
death, or property damage.
Содержание BRADEN BA3A
Страница 2: ......
Страница 25: ...23 THIS PAGE INTENTIONALLY LEFT BLANK...
Страница 26: ...24 WINCH CROSS SECTION...
Страница 35: ...33...
Страница 37: ......