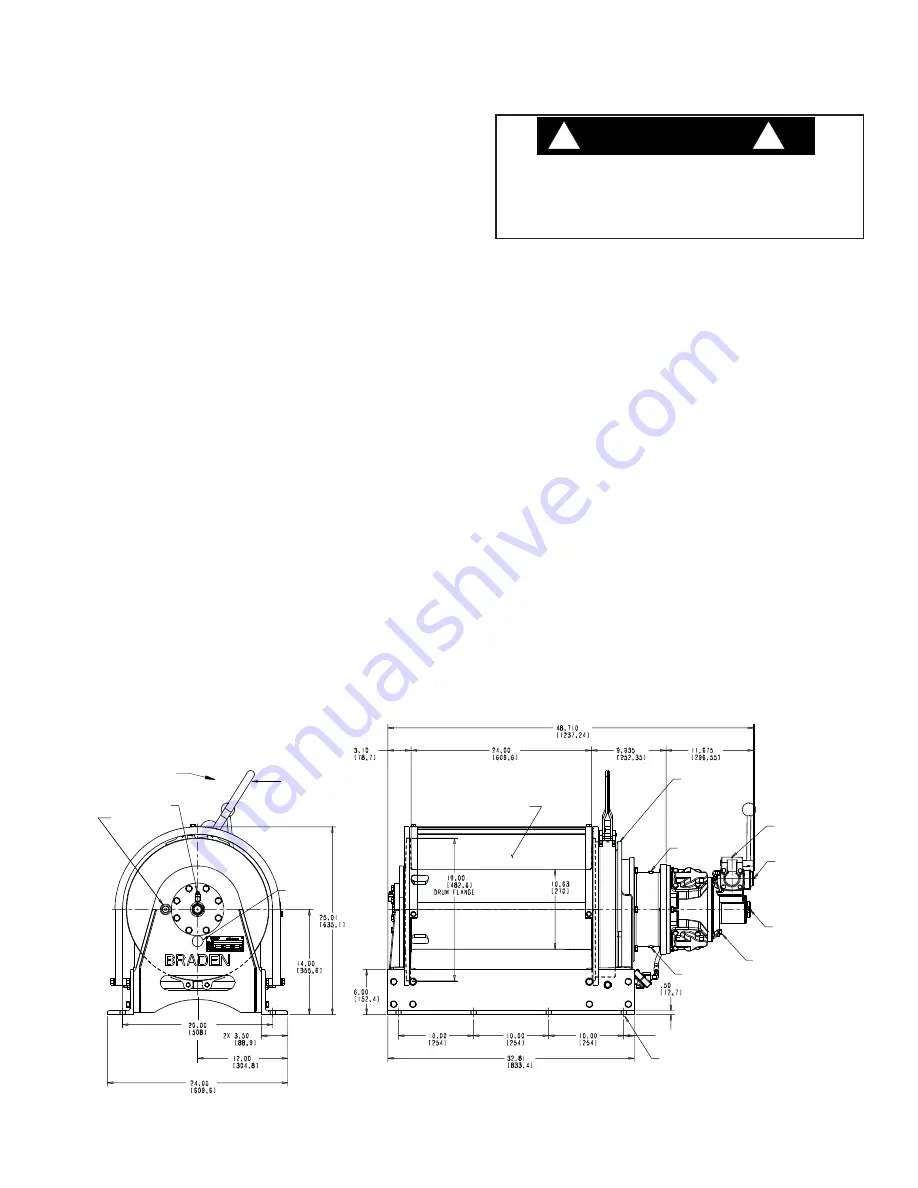
9
INSTALLATION
GENERAL REQUIREMENTS
1. The hoist must be mounted with the centerline of the
drum in a horizontal position. The mounting plane can
be rotated to any position around this centerline, pro-
viding the vent plug is positioned above the oil lev-
el. The vent plug must always be located above the
horizontal centerline of the hoist drum. If the hoist is
mounted on a pivoting surface, be sure the vent re-
mains above the centerline at all times. If necessary,
reposition the bearing support.
2. When mounting the winch, Grade 8, or better quality,
bolts and nuts are required. All mounting holes in the
hoist base must be used.
3. It is important that the hoist be mounted on a surface
that will not fl ex when the hoist is in use, since this
could bind the working parts of the hoist. Also, be
sure the hoist is mounted on a fl at surface. If neces-
sary, use shim stock to insure proper mounting. The
mounting surface should be fl at within ± .062 in. (1.5
mm).
4. Make certain that the hoist drum is centered behind the
fi rst sheave and the fl eet angle is not more than 1½
degrees or less than 1/2 degrees. The hoist should
also be mounted perpendicular to an imaginary line
from the center of the drum to the fi rst sheave to en-
sure even spooling. (ref page 7).
With the standard 24 inch wide (61 cm) winch drum,
the maximum distance to the fi rst sheave (1/2 degree
fl eet angle) is 115 ft. (35 m), and the minimum dis-
tance (1 ½ degree fl eet angle) is 38.2 ft. (11.7 m).
5. The air supply must be clean and free from moisture.
An airline fi lter and mist lubricator should be incorpo-
rated in the air supply line, located immediately before
the motor. The fi lter should have a moisture trap and
provide 20 micron fi ltration. If the rated performance
of the motor is to be obtained, all valves and pipework
must be of adequate size. For short pipe runs (up to 2
meters) the supply line should be the same size as the
motor ports and larger for longer runs. Valves should
be fi tted as close as possible to the motor.
6. Before connecting to the air supply blow out the air
lines to remove any loose scale, swarf or abrasive
dust which may be present.
7. When
fi rst running the motor, some light oil should be
injected into the inlet connection to ensure adequate
lubrication until the airline lubrication is established.
9. Ensure winch and air motor crankcase have been
8illed to the proper level with recommended oil.
9. Ensure dust shipping cups and plugs have been re-
moved from all air motor ports before operating the
winch.
DO NOT
install any detents or latching mechanism
that could hold the control valve in an actuated or run-
ning position when the operator releases the control
handle.
CAUTION
WARNING
!
!
HAND BRAKE
LEVER
VENT
OIL FILL &
ACCESS HOLE
OIL DRAIN
ACCESS HOLE
GUARD EXPANDED METAL
NOT SHOWN FOR CLARITY
STEEL STAMP
MODEL NO. &
SERIAL NO.
THIS LOCATION
OIL FILL
MOTOR INLET PORT
1” - 11 1/2 NPT
VALVE EXHAUST PORT
1” - 11 1/2 NPT
MOTOR EXHAUST PORT
1 1/4 - 11 1/2 NPT
OIL DRAIN
MOTOR OIL LEVEL PLUG
8X .688 DIA.
MOUNTING HOLES
1.41
(35,7)
HOIST
All bolts must be Grade 8 or better 5/8 in.with hard washer under the nut. Torque to chart specifi cation on Page 13.
Содержание Braden BA2A
Страница 2: ...2...
Страница 25: ...25 THIS PAGE INTENTIONALLY LEFT BLANK...
Страница 26: ...26 WINCH CROSS SECTION...