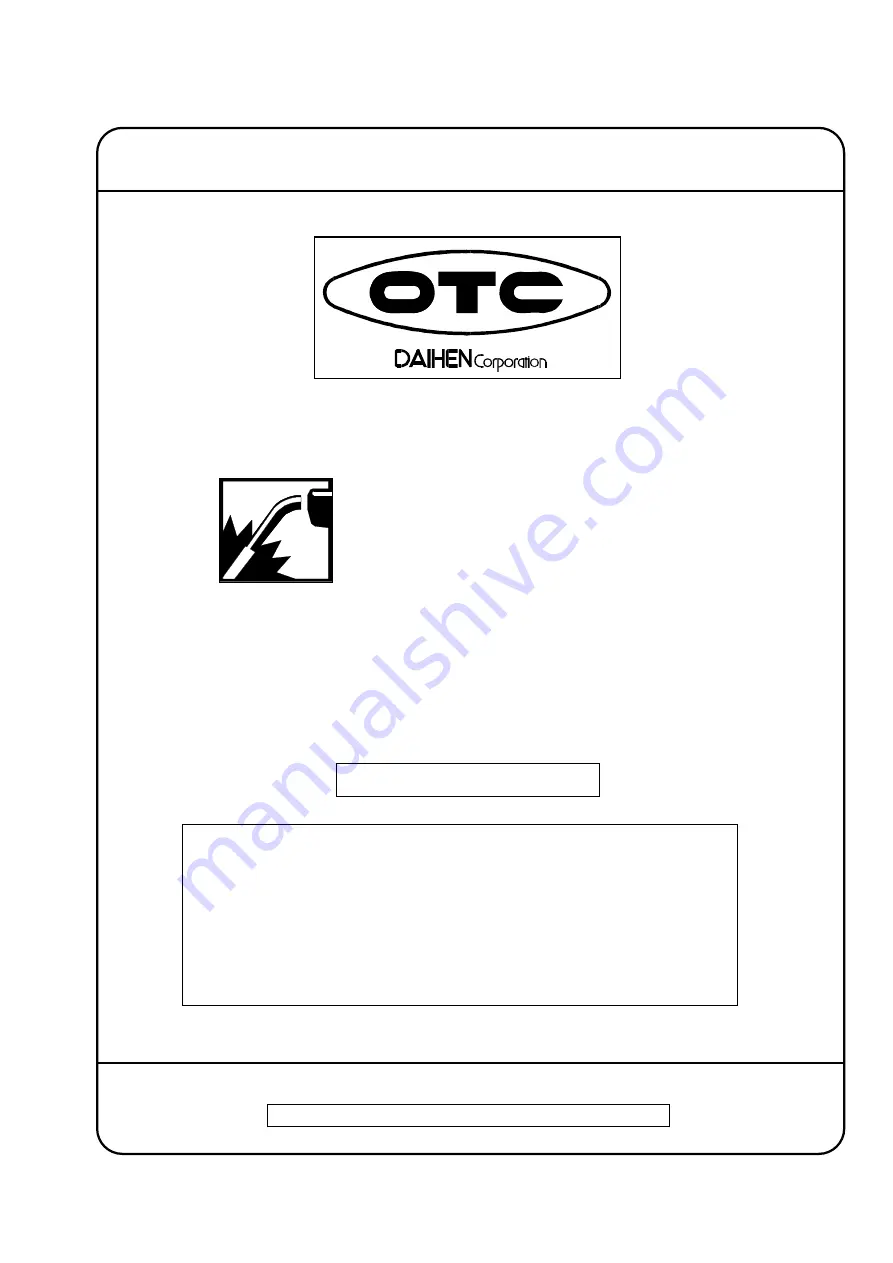
MANUAL NO:P30051
OWNER'S MANUAL
FOR
DIGITAL INVERTER
DP270C
INVERTER CONTROLLED WELDING POWER SOURCE
DO NOT DESTROY
IMPORTANT: Read and understand the entire contents of this
manual, with special emphasis on the safety material throughout
the manual, before installing, operating, or maintaining this
equipment. This equipment and this manual are for use only by
persons trained and experienced in the safety operation of welding
equipment. Do not allow untrained persons to install, operate or
maintain this equipment. Contact your distributor if you do not
fully understand this manual.
DAIHEN Corporation
WELDING PRODUCTS DIVISION
July 8, 2008
Upon contact, advise MODEL and MANUAL NO.
12-2-095-1
MODEL: DP-270C
P30051
MAG