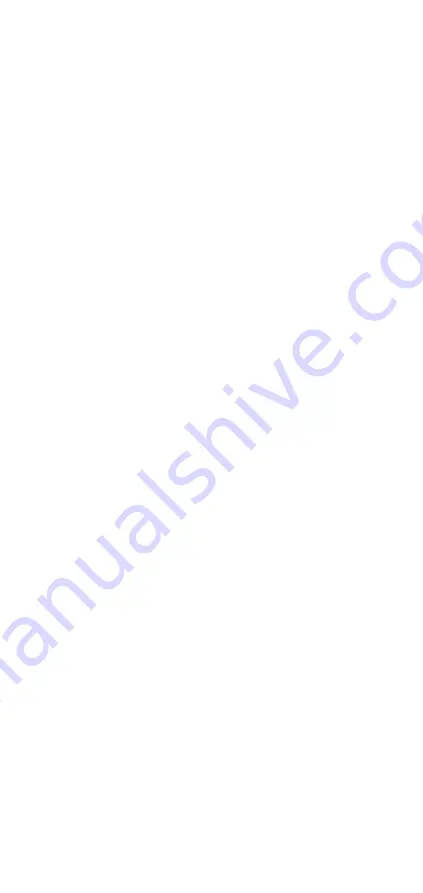
7
2. Using a designated 2-component PU adhesive putty, bond the adapter
(A) assembly
(Fig. 2)
to desired location on the socket
(Fig. 3)
.
3. Wrap thermoplastic socket and adapter firmly with glass reinforced
casting tape, enabling test fitting of the prosthesis
(Fig. 4)
.
4. Drill through housing dummy into cast using a sharp 3 mm drill bit.
Take care to align drill with centerline
(Fig. 5)
.
5. Remove housing dummy (X
1
) and replace with seal (B) / duckbill
valve (C) / mesh filter (D) and then screw in the expulsion housing
(E) / E2 connector (F)
(Fig. 6)
.
Note:
When inserting the housing/connector, make sure that the
seal/valve/mesh is not crooked, otherwise the housing may not hold
vacuum properly.
6. Place large seal (G) / O-ring (H) below housing. Complete assembly
with the plate (I/J/K/L), applying medium strength thread locker to
4-hole screws and torque twice to 10 Nm
(Fig. 7)
.
Note:
Make sure threads are clean and provide full engagement of
screws without resistance. Only use screws supplied with kit.
7. [For L-544611, L-544612 and L-544613] Secure Unity tube to the
connector on the plate (J/K).
Laminated Socket Procedure
1. Drape a layer of ~3 mm PETG or equivalent rigid thermoplastic sheet
over cast positive
(Fig. 8)
. Roughen distal area.
Note:
Distal area must be clean of dirt, dust, and grease, as otherwise
the bonding connection may not work.
2. Screw housing dummy (X
1
) into socket adapter (A)
(Fig. 9)
. Using a
designated 2-component PU adhesive putty, bond the adapter
assembly to desired location directly on thermoplastic layer
(Fig. 10)
.
Take care to fill the center area for a bubble free bond between
housing dummy and thermoplastic layer.
3. Remove housing dummy (X
1
). Place lamination dummy (X
2
) in
adapter
(Fig. 11)
.
4. Tie reinforcement material in groove on socket adapter and do a
second tie between socket and adapter. Apply the reinforcement
material layup to agree with the expected stress
(Fig. 12)
.
5. Apply PVA bag and impregnate laminate with conventional methods
(Fig. 13)
.
6. Tie around lamination dummy with electrical tape to push out the
resin between the PVA bag and dummy. This will produce clean edge
and minimize finishing work
(Fig. 13)
.
7. Once resin has set, drill through lamination dummy (X
2
) into cast using
a sharp 3 mm drill bit. Take care to align drill with centerline
(Fig. 14)
.
8. Remove excess resin, PVA bag and lamination dummy (X
2
). Remove
plaster from inside of socket.
9. Place seal (B) / duckbill valve (C) / mesh filter (D) and then screw in
the expulsion housing (E) / E2 connector (F)
(Fig. 15)
.
Note:
When inserting the housing/connector, make sure that the
seal/valve/mesh is not crooked, otherwise the housing may not hold
vacuum properly.
10. Place large seal (G) / O-ring (H) below housing. Complete assembly
with the plate (I/J/K/L), applying medium strength thread locker to
4-hole screws and torque twice to 10 Nm
(Fig. 16)
.
Note:
Make sure threads are clean and provide full engagement of
screws without resistance. Only use screws supplied with kit.
11. [For L-544611, L-544612 and L-544613] Secure Unity tube to the
connector on the plate (J/K).