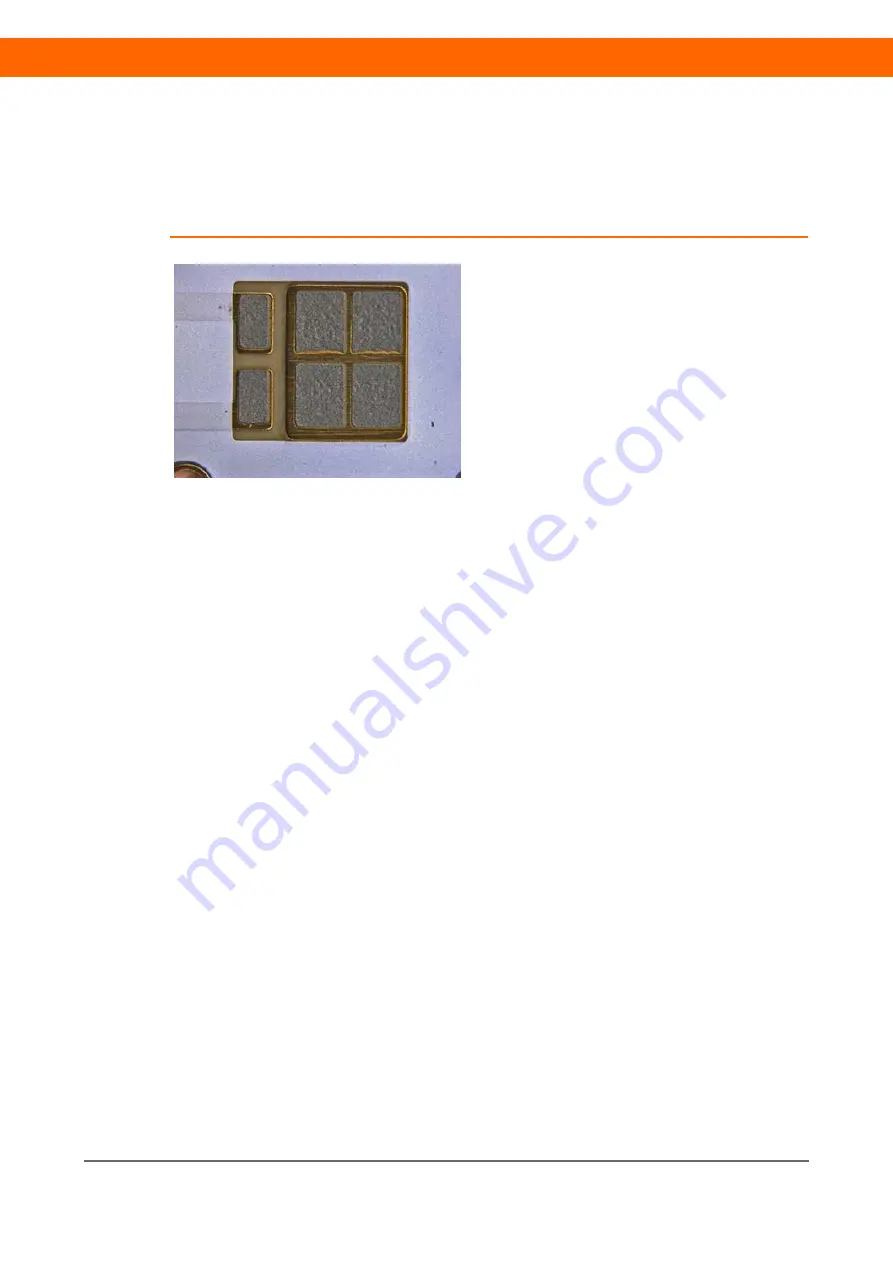
www.osram-os.com
16 / 18
2020-06-04 | Document No.: AN149
Solder stencil
In the SMT process, solder paste is normally applied by stencil printing. The
design of the printing stencil and an accurate working process greatly influence
the applied amount and quality of the paste deposit. Figure 20 shows an
example of a printed circuit board with good solder paste printing.
Figure 20: Example of good solder paste printing
Proper solder paste printing increases the solder quality. Effects such as solder
bridges, solder balling, solder spray and/or other soldering defects are largely
determined by the design of the stencil apertures and the quality of the stencil
printing (e.g. positioning, cleanliness of the stencil, etc.). For the OSRAM
OSTAR
®
Projection Power a stencil thickness of 120 μm is recommended. A
uniform solder joint thickness is also recommended in order to produce reliable
solder joints and obtain an appropriate optical alignment.
For the paste printing process OSRAM Opto Semiconductors has successfully
used the standard SAC 305 Type 3 solder paste (HERAEUS F640 SAC 305
Type 3). For process evaluation, process control and failure prevention it is
recommended to check the solder paste volume with SPI (Solder Paste
Inspection) regularly.
Reflow soldering
Since the OSRAM OSTAR
®
Projection Power is generally compatible with
existing industrial SMT processing methods, current populating techniques can
be used for the mounting process. The individual soldering conditions for each
LED type in accordance with to JEDEC can be found in the respective data
sheet. A standard reflow soldering process with forced convection under
standard N
2
atmosphere (<500 ppm O
2
) is mandatory for mounting the
component, in which a typical lead-free SnAgCu metal alloy is used as solder.
Figure 21 shows the temperature profile for lead-free soldering with the
recommended peak temperature of 245 °C. In this context, it is recommended
to check the profile on all new PCB materials and designs. As a good starting
point, the recommended temperature profile provided by the solder paste
manufacturer can be used. The maximum parameters and temperature for the
profile as specified in the data sheet should not, however, be exceeded.