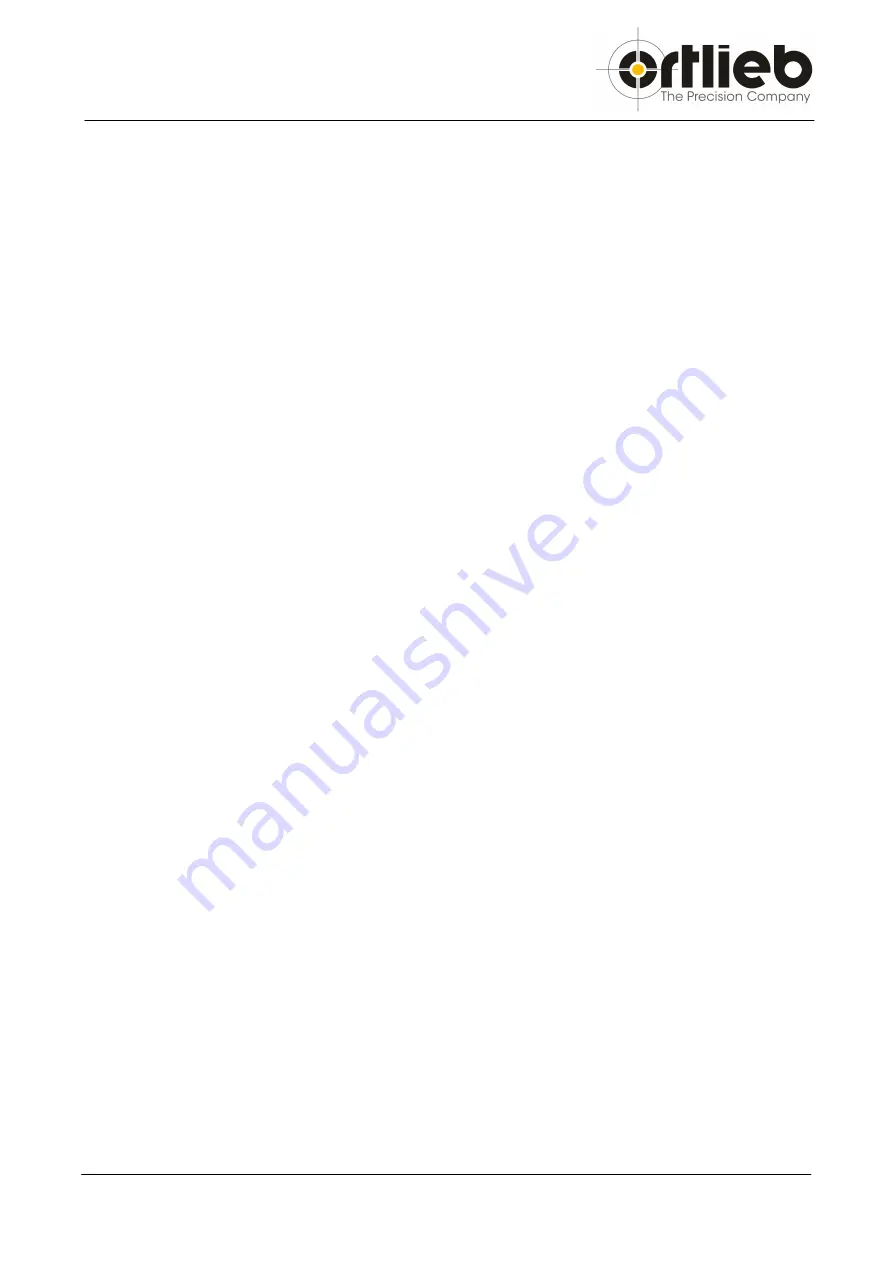
5. General Safety Instructions
16
Ortlieb Präzisionssysteme GmbH & Co. KG • Jurastr.11 • 73119 Zell unter Aichelberg • Germany
e-mail: [email protected] • www.ortlieb.net
5.1 Checklist for Installation
(Rubber Clamping Segment TGR + draw-bolt TGZ)
1.)
TGR and TGZ are grounded and paired in the testing facility. TGR + TGZ are not
individually interchangeable. This guarantees stroke position
±
0.1 mm when TG is
exchanged.
2.)
Tool –“Eject” max. 0.5 mm (0.3mm up to TG30). The tool is only drawn in securely by the
tool gripper TG in this range. Ensure that the clamping reserve is min. 2 mm and max. 3
mm.
3.)
Check the clamping force. The max. pull-in force, Fz max. , must not be exceeded.
4.)
Tool clamping must not be one-sided. Guide the disc spring stack accurately.
5.)
Spindle receiver must meet DIN 69063 standard and Ortlieb TG installation dimensions.
Taper pre-load 0.1-0.4 mm, depending on size.
(Distance between spindle and tool plane surfaces).
Functional surfaces hardened min. 1mm deep to HRc 60 +2.
6.)
When clamping the tool, there must not be any pressure (blow-out) present before the
taper pre-load. Otherwise the tool may not be able to be moved into the end position.
TGR would sustain damage.
7.)
Observe the control operation.
Insert the tool until it reaches the limit stop at the TGZ plane surface, then clamp it.
Clamping must not de done too soon, as otherwise the TGR can not pull-in the tool.
8.)
Tool change: Gripper – eject – unclamp - blow-out. Make sure that the tool and spindle
are clean. If chips are drawn in, TGR will sustain damage. (One-sided overloading of the
TGR clamping segments).
9.)
If one TGR- segment breaks, the tool will nevertheless be clamped safely. However the
TG (TGR + TGZ ) must be exchanged immediately as a complete unit.